Tiempo y movimiento recuperados
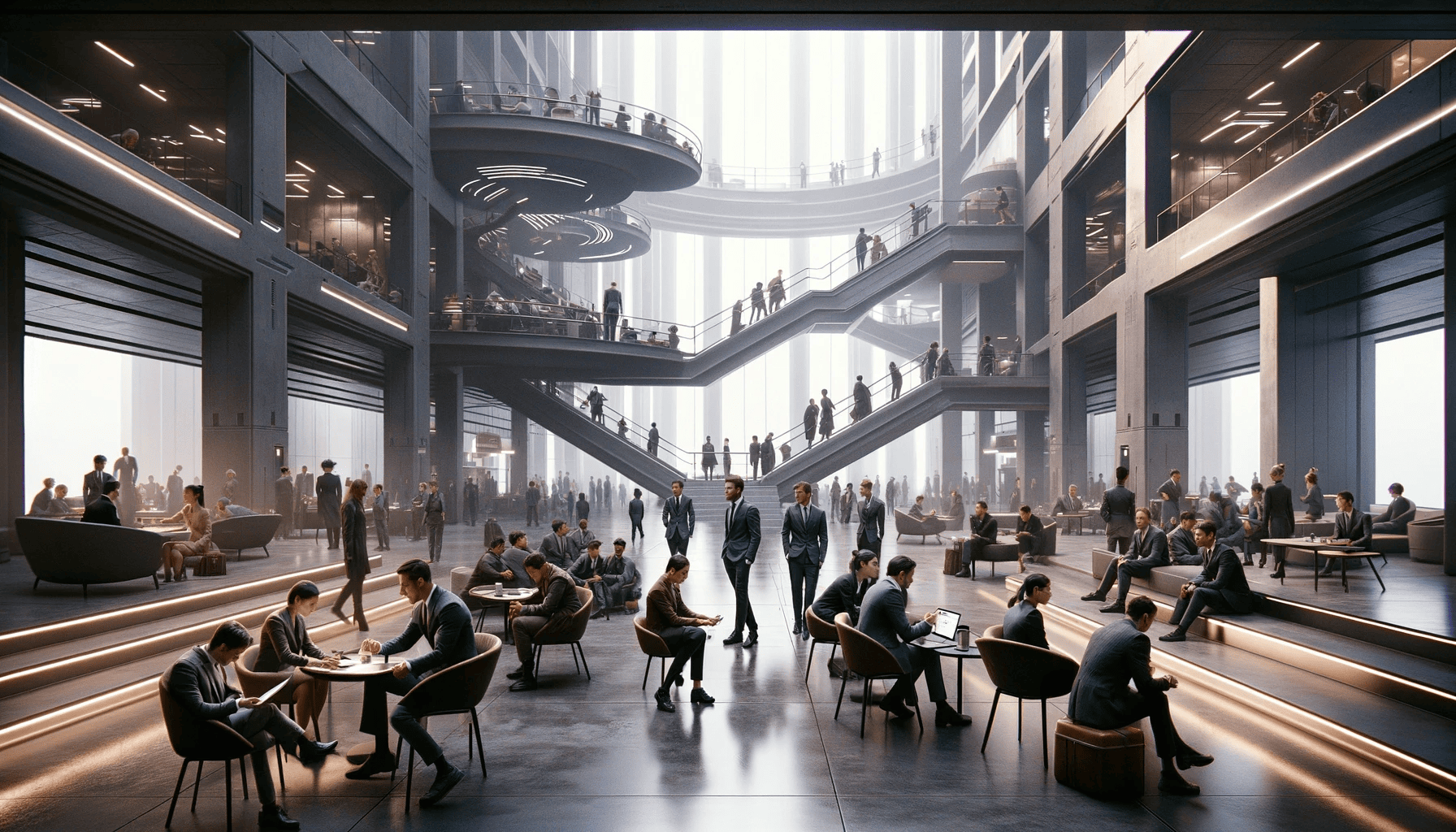
La estandarización es la muerte de la creatividad.
La regimentación de tiempo y movimiento impide la mejora continua.
La jerarquía sofoca el aprendizaje.
La manufactura estadounidense está en la agonía de la revolución, y suposiciones como estas se están convirtiendo en la nueva sabiduría convencional sobre el trabajo. Este nuevo evangelio establece a Frederick Winslow Taylor y sus estudios de tiempo y movimiento como el villano. Afirma que la calidad, la productividad y el aprendizaje dependen de la capacidad de la dirección para liberar a los trabajadores de las restricciones coercitivas de la burocracia. Insiste en que las normas detalladas, implementadas con gran disciplina en una organización jerárquica, alienarán inevitablemente a los empleados, envenenarán las relaciones laborales, sofocarán la iniciativa y la innovación y obstaculizarán la capacidad de una organización para cambiar y aprender.
Pero, ¿qué pasa si, como creo, este nuevo credo está equivocado? ¿Qué pasa si se puede diseñar la burocracia para fomentar la innovación y el compromiso? ¿Qué pasaría si la estandarización, entendida y practicada correctamente, demostrara ser una fuente de aprendizaje y motivación continuos?
En Fremont, California, una empresa conjunta GM-Toyota llamada New United Motor Manufacturing Inc., NUMMI, para abreviar, ha logrado emplear una forma innovadora de regulación del tiempo y movimiento de Taylor en la fábrica no solo para crear productividad y calidad de clase mundial, sino también para aumentar los trabajadores motivación y satisfacción. Además, los procedimientos intensamente tayloristas de NUMMI parecen alentar más que desalentar el aprendizaje organizacional y, por lo tanto, la mejora continua.
Este resultado parece sorprendente porque durante décadas nuestras actitudes hacia el trabajo han sido moldeadas por una cadena de razonamientos que nos ha llevado a esperar (y nos ha garantizado que conseguiríamos) un círculo vicioso de creciente coerción gerencial y recalcitrancia de los empleados. El razonamiento es algo así:
- Cuando las tareas son rutinarias y repetitivas, la eficiencia y la calidad requieren procedimientos de trabajo estandarizados.
- Los altos niveles de estandarización privan a los trabajos de su interés intrínseco, lo que reduce la motivación y la creatividad.
- El trabajo desmotivador conduce a un comportamiento disfuncional de los empleados, como ausentismo, alta rotación, mala atención a la calidad, huelgas e incluso sabotaje.
- El comportamiento contraproducente de la fuerza laboral requiere una gestión más autoritaria, más capas jerárquicas e incluso niveles más altos de estandarización.
En resumen, el taylorismo conduce inevitablemente al descontento de la fuerza laboral y a la beligerancia sindical, lo que a su vez conduce inevitablemente a niveles más altos de exceso burocrático. La organización del trabajo se basa en la lógica deshumanizadora de la coerción y el cumplimiento reacio. Mientras tanto, la calidad, los beneficios y la satisfacción laboral se ven afectados.
La experiencia de NUMMI va directamente en contra de este pensamiento. Esto se debe a que el segundo paso de esta cadena de razonamiento es falso. Normas formales de trabajo desarrolladas por ingenieros industriales e impuestas a los trabajadores son alienante. Pero los procedimientos diseñados por los propios trabajadores en un esfuerzo continuo y exitoso por mejorar la productividad, la calidad, las habilidades y la comprensión pueden humanizar incluso las formas más disciplinadas de burocracia. Además, NUMMI demuestra que la jerarquía puede proporcionar apoyo y experiencia en lugar de una mera estructura de mando.
Lo que demuestra el experimento NUMMI es que la jerarquía y la estandarización, con todas sus ventajas conocidas para la eficiencia, no necesitan basarse en la lógica de la coerción. En cambio, pueden basarse en la lógica del aprendizaje, una lógica que motiva a los trabajadores y aprovecha su contribución potencial a la mejora continua.
En la práctica, la «burocracia del aprendizaje» de NUMMI alcanza tres objetivos. En primer lugar, sirve a la administración mejorando la calidad y la productividad generales. En segundo lugar, sirve a los trabajadores involucrándolos en el diseño y el control de su propio trabajo, aumentando su motivación y satisfacción en el trabajo y alterando el equilibrio de poder entre mano de obra y dirección. En tercer lugar, sirve a los intereses de toda la organización (la dirección y la fuerza de trabajo) mediante la creación de un sistema formal para fomentar el aprendizaje, captar y comunicar la innovación e institucionalizar la mejora continua.
La peor planta del mundo
NUMMI se encuentra en lo que una vez fue la planta de ensamblaje de General Motors en Fremont, California, a 35 millas al sureste de San Francisco, que abrió sus puertas en 1963 y fabricó camiones GM y Chevy Malibu y Century. En la antigua planta de GM-Fremont, el trabajo se organizó siguiendo las líneas tradicionales de Taylorist, con más de 80 ingenieros industriales estableciendo normas de línea de montaje que la dirección hizo todo lo posible para imponer a la fuerza de trabajo, con resultados predecibles.
Con el paso de los años, GM-Fremont se convirtió en lo que un gerente llamó «la peor planta del mundo». La productividad era una de las más bajas de todas las plantas transgénicas, la calidad era abismal y el abuso de drogas y alcohol era desenfrenado tanto dentro como fuera del trabajo. El absentismo era tan alto que la planta empleaba a 20% más trabajadores de los que necesitaba para garantizar una fuerza laboral adecuada en un día determinado. El local de United Auto Workers se ganó una reputación nacional por su militancia; de 1963 a 1982, las huelgas salvajes y los enfermizos cerraron la planta cuatro veces. La acumulación de quejas no resueltas a menudo superaba las 5.000.
GM-Fremont tenía baja productividad, calidad abismal, abuso de drogas y alcohol y absentismo de más de 20%.
GM-Fremont alcanzó su máximo empleo de 6.800 trabajadores por hora en 1978. Las cifras se redujeron constantemente a poco más de 3.000 cuando GM finalmente cerró la planta en febrero de 1982.
Ese mismo año comenzaron las conversaciones entre GM y Toyota sobre una posible empresa conjunta. En febrero de 1983, las dos compañías llegaron a un acuerdo de principio para producir una versión del Toyota Corolla, renombrada como Nova, en la planta de Fremont, utilizando el sistema de producción de Toyota. GM se encargaría del marketing y las ventas; Toyota se encargaría del diseño de productos, la ingeniería y las operaciones diarias. La nueva entidad, NUMMI, fabricaría y montaría el coche. A partir de 1986, la planta también fabricó Corolla FxS. En 1988, tanto el Nova como el FX se retiraron gradualmente, y Fremont comenzó a construir Corollas, Geo Prizms y, a finales de 1991, camiones Toyota.
Los objetivos de las dos empresas eran complementarios. GM quería aprender sobre el sistema de producción de Toyota. También obtuvo un subcompacto de alta calidad para su división Chevrolet en un momento en que la cuota de mercado de GM se estaba erosionando rápidamente. Toyota quería ayudar a desactivar el problema comercial construyendo automóviles en los Estados Unidos. Para ello, necesitaba aprender sobre los proveedores estadounidenses.
Toyota afirmó más tarde que también había querido «ganar experiencia con los sindicatos estadounidenses», pero al principio Toyota no quería tener nada que ver con el UAW. Sucedió que no había alternativa. GM no les ofreció ninguna otra instalación, y el UAW tenía el control de facto de Fremont. Además, GM temía una reacción violenta de los sindicatos en otras plantas si intentaba crear la empresa conjunta como una tienda no sindical.
En septiembre de 1983, NUMMI y el sindicato firmaron una carta de intenciones en la que se reconocía al UAW como único agente de negociación de la fuerza laboral de NUMMI, especificando los salarios y prestaciones prevalecientes en la industria automovilística y estipulando que la mayoría de la fuerza laboral sería contratada entre los trabajadores despedidos de GM-Fremont. A cambio, el UAW acordó apoyar la implementación de un nuevo sistema de producción y negociar un nuevo contrato.
NUMMI se organizó formalmente en febrero de 1984. Toyota contribuyó$ 100 millones de capital y GM suministró la planta de Fremont. La contratación comenzó en mayo. Todos los solicitantes pasaron tres días de simulaciones de producción, exámenes escritos, discusiones y entrevistas. Los gerentes y los dirigentes sindicales evaluaron conjuntamente a los candidatos para los puestos de trabajo por hora: líder del equipo y miembro del equipo. El sindicato también desempeñó un papel en la selección de directivos, excepto los 16 que vinieron directamente de GM y un grupo de unos 30 gerentes y coordinadores de producción de Toyota que vinieron de Japón. El CEO, Tatsuo Toyoda, trajo consigo el prestigio de la familia fundadora de la empresa.
Durante los 20 meses siguientes, NUMMI contrató a 2.200 trabajadores por hora, 85% de la antigua planta de GM-Fremont, entre ellos la antigua jerarquía sindical. (Casi ninguno de los empleados asalariados de GM-Fremont fue contratado de nuevo. En cualquier caso, muchos se habían trasladado hacía mucho tiempo a otras plantas transgénicas). Dado que GM-Fremont había contratado poco durante varios años antes de su cierre, la edad media de la nueva fuerza de trabajo era de 41 años. La mayoría tenía estudios secundarios. Cerca de 26% eran hispanos, 20% negro y 15% femenino.
El primer grupo de 450 jefes de equipo y todo el equipo directivo de NUMMI asistieron a un programa de capacitación de tres semanas en la planta de Toyota en Japón, Takaoka, en el que se inspiró NUMMI. Estas personas ayudaron a montar la nueva planta y a formar a los trabajadores.
El sistema de producción NUMMI requería que la gente trabajara más duro que en GM-Fremont. Los trabajos en la antigua planta ocupaban a un trabajador experimentado unos 45 segundos de cada 60. La norma de NUMMI se acerca a los 57 segundos de 60. Y como los trabajadores tienen que cumplir con estándares de calidad y eficiencia mucho más altos, tienen que trabajar no solo más duro sino también de forma más inteligente.
El sistema de producción NUMMI no solo hizo que la gente trabajara más arduamente, sino que también les hacía trabajar de forma más inteligente.
A finales de 1986, la productividad de NUMMI era superior a la de cualquier otra instalación de GM y más del doble que la de su predecesora, GM-Fremont. De hecho, la productividad de NUMMI era casi tan alta como la de Takaoka, a pesar de que sus trabajadores eran, en promedio, diez años más viejos y mucho menos experimentados con el sistema de producción Toyota. Calidad, según las auditorías internas de GM, encuestas a clientes y Informes del consumidor era mucho más alta que en cualquier otra planta transgénica y, de nuevo, casi tan alta como la de Takaoka.
Igualmente importante, el absentismo ha caído de entre 20% y 25% en la antigua planta de GM-Fremont a un constante 3% a 4% en la NUMMI; el uso indebido de sustancias es un problema mínimo; y la participación en el programa de sugerencias ha aumentado constantemente de 26% en 1986 a 92% en 1991. Cuando GM-Fremont cerró sus puertas, tenía más de 2.000 quejas pendientes. A finales de 1991, se habían presentado unas 700 quejas ante la NUMMI en total en el transcurso de ocho años. La proporción global de empleados que se describen a sí mismos como «satisfechos» o «muy satisfechos» ha aumentado progresivamente a más del 90%%.
En 1990, Toyota anunció que invertiría$ 350 millones en una línea de montaje adicional para construir un camión Toyota para el mercado estadounidense. Así que NUMMI contrató a 650 trabajadores por hora, además de los 3.100, más 400 asalariados, que ya estaban empleados. Los primeros camiones salieron de la línea en agosto de 1991.
Miedo, selección, socialización
El notable cambio de rumbo de NUMMI plantea una pregunta obvia: ¿cómo es posible convertir una planta de peor a mejor calidad y de una productividad sombría a superlativa en el transcurso de unos meses? Las respuestas más obvias no son del todo satisfactorias.
Por ejemplo, el miedo. La planta de GM-Fremont cerró en 1982 y las personas recontratadas por NUMMI no volvieron a trabajar hasta 1984. Dos años de desempleo pueden producir una gran cooperación. De hecho, algunos trabajadores de NUMMI creen que la dirección utiliza deliberadamente el espectro del cierre de otra planta como una amenaza velada para mantener a la gente a raya. Sin embargo, el presidente del comité de negociación sindical señala que, si bien el cierre de la antigua planta obviamente hizo que los trabajadores fueran más receptivos al nuevo enfoque de NUMMI, un retorno a los viejos métodos de gestión coercitiva habría producido un rápido retorno a los viejos patrones de comportamiento antagónico de la fuerza laboral.
Voces desde la fábrica: extractos de entrevistas con gerentes, trabajadores y dirigentes sindicales
Nunca olvidaré cuando GM me contrató por primera vez hace muchos años. El gerente de personal que nos contrató llevó a los... trabajadores que empezaban ese día a una habitación y explicó: «Ustedes nuevos empleados han sido contratados de la misma manera que nosotros requisamos papel de lija. Te pondremos de nuevo en la calle cuando ya no te necesiten». ¿Cómo diablos puedes esperar fomentar una fuerza laboral leal y productiva cuando empiezas a escuchar cosas así? En NUMMI, el mensaje cuando llegamos a bordo era «Bienvenidos a la familia». —Líder de equipo
Una vez que empiezas a trabajar como un equipo real, ya no serás solo un conocido del trabajo. Cuando realmente confías en tus compañeros de trabajo, confías en ellos, te sientes orgulloso de lo que pueden hacer juntos y luego te vuelves leal a ellos. Eso es lo que hace que la tasa de absentismo sea tan baja aquí. Cuando me levanto por la mañana, sé que no hay nadie que me reemplace si me siento mal o con resaca o lo que sea... En NUMMI, sé que mi equipo me necesita. —Líder de equipo
El trabajador promedio está definitivamente más ocupado en NUMMI que en Fremont. Ese es el objetivo del sistema de producción NUMMI y la forma en que vincula el trabajo estandarizado, sin inventarios y sin defectos de calidad. Los equipos de trabajo de NUMMI no son como los equipos autónomos de los que lees en otras plantas. Aquí no somos autónomos, porque todos estamos muy unidos. Pero no es que nos estén presionando a trabajar más duro, porque son los trabajadores los que hacen que todo funcione; somos nosotros los que hacemos que el trabajo estandarizado y el kaizen sugerencias. Dirigimos la planta, y si no funciona bien, la detenemos. En GM-Fremont, solo teníamos nuestros pequeños trabajos. Trabajaríamos muy rápido para construir un colchón de reserva para poder tomarnos un descanso unos minutos para fumar un cigarrillo o charlar con un amigo. Ese tipo de juego de «date prisa y espera» hizo que el trabajo sea realmente agotador. Había material y piezas terminadas por todas partes, y la mitad estaba defectuosa de todos modos. Estar constantemente ocupado sin ser molestado y sin sobrecargar de trabajo elimina mucho del dolor del trabajo. Trabajas más duro en NUMMI, pero te lo juro, te vas a casa al final del día sintiéndote menos cansado, ¡y te sientes muchísimo mejor contigo mismo! —Líder de equipo
En nuestra formación laboral estandarizada, nuestros maestros nos dijeron que deberíamos acercarnos a nuestros compañeros de equipo y sugerirles formas de mejorar sus puestos de trabajo. Demonios, ¿me ves intentando eso con un miembro del equipo que mide 1,80 metros y pesa 250 libras? Me levantarías del suelo si intentara que... el trabajo estandarizado es una broma por lo que veo. Se supone que debemos ir a la gerencia y avisarles cuándo tenemos segundos extra de sobra. ¿Por qué iba a hacer eso cuando todo lo que sucederá es que me quitarán mis segundos libres y me trabajarán aún más que antes? Prefiero hacer el trabajo de la forma en que ya me siento cómodo. No soy tonto. —Miembro del equipo
Nuestra suposición en NUMMI es que la gente viene a trabajar para hacer un día de trabajo justo. Hay excepciones, y sería estúpido ignorarlas. Pero 90% de las personas, si les das la oportunidad de trabajar de forma más inteligente y mejorar sus puestos de trabajo, y si descubren que al hacerlo han creado tiempo libre para sí mismos, buscarán espontáneamente cosas nuevas que hacer. Tengo cientos de ejemplos. No creo que la gente trabaje más en NUMMI que en otras plantas. No físicamente de todos modos. Pero el desafío mental es mucho mayor. —Gerente de departamento
No creo que los ingenieros industriales sean tontos. Son simplemente ignorantes. Cualquiera puede ver a otra persona hacer un trabajo y presentar sugerencias de mejora que suenan bien... Y es aún más fácil encontrar el procedimiento ideal si ni siquiera te molestas en observar al trabajador en el trabajo, sino hacerlo desde tu oficina, en papel. Casi cualquier cosa puede verse bien así. Incluso cuando hacemos nuestro propio análisis en nuestros equipos, algunas de las ideas más tontas pueden pasar por alto antes de probarlas.
Hay muchas cosas que entran en un buen diseño de trabajo... La persona que realmente hace el trabajo es la única que puede ver todos los factores. Y en Estados Unidos, los ingenieros nunca han tenido que trabajar en el suelo, como en Japón. Así que no saben lo que no saben... Hoy nosotros impulsar el proceso y, si necesitamos ayuda, el ingeniero estará allí al día siguiente para trabajar en ello con nosotros. —Líder de equipo
Una cosa que me gusta mucho del estilo Toyota es que pondrán una máquina para evitar que te agachas. La filosofía de Toyota es que el trabajador debe usar la máquina y no al revés... Estaría bien que los robots funcionaran a la perfección, y los ingenieros siempre parecen imaginar que lo harán. Pero no lo hacen, así que el trabajador acaba siendo utilizado por la máquina. En NUMMI, acabamos de instalar un robot para instalar el neumático de repuesto, lo que realmente ayuda al trabajador, porque siempre fue un trabajo muy agotador. Nos llevó un tiempo, y tuvimos que plantearlo en las reuniones de seguridad y discutir sobre ello. Y salieron adelante. Eso nunca sucedería en GM-Fremont: nunca se veía la automatización simplemente para ayudar al trabajador. —Oficial de la UAW
En el futuro vamos a necesitar líderes sindicales con más conocimientos técnicos y de gestión. Ahora estamos mucho más involucrados en decidir cómo funciona la planta. Eso amplía nuestras capacidades. La gerencia viene a pedirnos nuestra opinión... El viejo enfoque era mucho más simple: «Tú tomas la maldita decisión y me afligiré si quiero». Ahora tenemos que entender cómo funciona el sistema de producción, tomarnos el tiempo para analizar las cosas, formular propuestas mucho más detalladas. Este sistema realmente nos permite tomar tanto poder como sepamos qué hacer con él. —Oficial de la UAW
Ahora, cuando trato de explicar [NUMMI] a viejos compañeros de UAW de otras plantas... se dan cuenta de que me veo obligado a decir todo esto porque cerraron nuestra planta y no tuve otra opción. Creen que seguir el concepto de equipo y todo lo demás era el precio que teníamos que pagar para recuperar nuestros trabajos. Les explico que la planta es más limpia, más segura, tenemos más voz sobre temas importantes y tenemos una oportunidad real de fortalecer nuestra fuerza como sindicato. Les explico que nuestros miembros pueden ampliar su comprensión del sistema de fabricación y aumentar su autoestima, y que la formación que hemos recibido en fabricación, resolución de problemas, calidad, etc. puede ayudarles a alcanzar su máximo potencial y sacar más provecho de sus vidas. Les explico que en un sistema como este, los trabajadores tienen la oportunidad de hacer una contribución real a la sociedad; no tenemos que dejar que los gerentes piensen todo. Pero estos tipos simplemente no lo ven. Tal vez sea porque no han experimentado personalmente la forma en que funciona NUMMI. Cualquiera que sea la razón, ven que todo esto debilita al sindicato. Alguien como Irving Bluestone probablemente entiende lo que estamos haciendo. Tuvo la idea hace mucho tiempo: si el trabajador tiene derecho a votar por el presidente de los Estados Unidos, debería tener derecho a participar en las decisiones en la planta de la tienda. —Oficial de la UAW
En los viejos tiempos, teníamos que preocuparnos de que la dirección jugara sus juegos, y el sindicato estaba ahí para defendernos. Pero ahora, con el sindicato asumiendo su nuevo papel, no es tan sencillo como antes, y tenemos que preocuparnos tanto por los juegos de dirección como por los juegos sindicales. No quiero el tipo de músculo de unión que solíamos tener. Podrías salirte con la suya con casi cualquier cosa en la vieja planta, porque el sindicato te sacaría del apuro. Fue una locura. Pero no fue productivo. —Miembro del equipo
Hay gente aquí que te dirá que odian este lugar. Todo lo que digo es que las acciones hablan más que las palabras. Si la gente estuviera descontenta, no habría forma de que construyéramos un vehículo de la más alta calidad. No tendrías una planta tan limpia. Seguirías teniendo los problemas con las drogas que teníamos antes. Aún tendrías todos los gritos y gritos. No puedes forzar todo eso. Y prueba esto: ve a cualquiera de los baños y verás que no hay graffiti. Si la gente tiene un problema con su gerente, no tiene que decírselo en la pared del baño. Pueden decírselo a la cara. Y las primeras palabras del jefe serán: «¿Por qué?» Algo ha pasado aquí en NUMMI. Cuando estaba en GM, recuerdo que hace unos años recibí un premio de mi capataz por venir a trabajar durante 40 horas completas en una semana. ¡Un certificado! En NUMMI, he tenido una asistencia perfecta durante dos años. —Líder de equipo
Una segunda posibilidad es que la dirección eliminara a los problemáticos en el proceso de recontratación. Pero, de hecho, NUMMI volvió a contratar a toda la jerarquía sindical y a muchos militantes conocidos. En general, muy pocos solicitantes fueron excluídos. El sindicato incluso ganó una segunda oportunidad para algunos que no pasaron las pruebas de drogas la primera vez.
Una tercera respuesta es que NUMMI utilizó un proceso de socialización integral durante la contratación para inculcar un nuevo conjunto de valores en la nueva fuerza de trabajo. Ciertamente, NUMMI hizo todo lo posible para dar forma y alterar las actitudes tanto de los trabajadores como de los directivos. Por ejemplo, la empresa trató de socavar las divisiones habituales entre los trabajadores y la dirección eliminando las instalaciones especiales de estacionamiento y comedor para los gerentes e introduciendo un código de vestimenta idéntico (uniformes) para todos. La gerencia también dedicó mucha atención a cada alquiler individual y les dio la bienvenida personalmente a la empresa que iba a construir «los mejores vehículos de Estados Unidos».
Por mucho que estos tres factores —el miedo al desempleo, la selección y la socialización— hayan contribuido al resultado final, no explican adecuadamente el éxito continuo de NUMMI ni su capacidad para permitir que los trabajadores obtengan una motivación mejorada y una mayor satisfacción de un sistema que los coloca en una situación más reglamentado y burocrático y les hace trabajar más duro y más rápido. La parte más crítica de esa explicación reside en el propio sistema de producción y en las políticas y prácticas que lo respaldan.
El sistema de producción NUMMI
La idea de una producción sistema es en sí misma una novedad en muchas fábricas estadounidenses. Todas las fábricas cuentan con técnicas, procedimientos y políticas de producción, pero no suelen comprender tanto un sistema como una acumulación ad hoc de respuestas a demandas cambiantes y a menudo contradictorias del negocio y del diseño. El sistema de producción de NUMMI es un conjunto finamente afinado y magníficamente integrado, refinado por Toyota a lo largo de décadas de experiencia en fabricación.
Las técnicas básicas son familiares al menos de nombre. La línea de montaje es una operación justo a tiempo que elimina el trabajo en curso y hace que la garantía de calidad sea responsabilidad de cada estación de trabajo. La aplicación de kaizen, o mejora continua, incluye un programa de sugerencias extraordinariamente activo, un perfeccionamiento constante de los procedimientos y la designación de equipos kaizen especiales para estudiar sugerencias individuales o llevar a cabo proyectos de mejora específicos. Cada máquina y cada proceso están diseñados para detectar automáticamente fallos de funcionamiento, piezas faltantes y ensamblajes incorrectos. Cada trabajo se analiza cuidadosamente para lograr la máxima eficiencia y calidad. La rotación de puestos es estándar; los trabajadores reciben formación cruzada en todas las asignaciones de equipo y, a continuación, se les permite pasar de una tarea a otra. La nivelación de producción planificada elimina las variaciones en los programas diarios y semanales.
Este sistema es esencialmente el mismo que usa Toyota en Japón, el mismo que muchos fabricantes estadounidenses están empezando a adoptar ahora. Pero el enfoque de NUMMI se distingue en dos aspectos: primero, su fuerte compromiso con el contexto social en el que se realiza el trabajo y, en segundo lugar, su intenso enfoque en el trabajo estandarizado.
El enfoque NUMMI tiene dos características distintivas: un compromiso con el contexto social del trabajo y un enfoque en la estandarización.
En términos de contexto social, NUMMI busca crear una atmósfera de confianza y propósito común. NUMMI mantiene una coherencia excepcional en sus estrategias y principios, construye cuidadosamente el consenso en torno a decisiones importantes y cuenta con programas que garantizan una comunicación adecuada de los resultados y otra información esencial.
La unidad estructural básica es el equipo de producción, del cual NUMMI cuenta con aproximadamente 350 personas, cada una de cinco a siete personas y un líder. La idea es que los equipos pequeños fomenten la toma de decisiones participativa y la vinculación del equipo. Cuatro equipos forman un grupo, liderado por un líder de grupo que representa el primer nivel de gestión.
Más allá de los equipos de producción, el equipo más grande es todo el mundo: todos los trabajadores, jefes de equipo, gerentes, ingenieros y personal de la planta, así como los proveedores de NUMMI. El liderazgo de Toyota quiere que los trabajadores entiendan que la empresa no es propiedad de la gerencia sino de todos juntos. En opinión de NUMMI, el objetivo principal y la responsabilidad de la jerarquía de gestión es apoyar a los equipos de producción con experiencia en la resolución de problemas.
La expresión más sustantiva de esta estrategia de equipo grande es la política de no despido establecida en el acuerdo de negociación colectiva de NUMMI con el sindicato. Reconociendo que «la seguridad laboral es esencial para el bienestar de un empleado», NUMMI acepta «que no despedirá a los empleados a menos que se vean obligados a hacerlo por condiciones económicas severas que amenazan la viabilidad a largo plazo de la Compañía». NUMMI acepta tomar medidas tan drásticas como reducir los salarios de la dirección y asignar trabajos subcontratados previamente a los empleados de la unidad de negociación antes de recurrir a los despidos.
La dirección considera que la política de no despido es un apoyo fundamental para su estrategia general de producción no solo porque refuerza la cultura del equipo, sino también porque elimina el temor de los trabajadores a poner en peligro los puestos de trabajo cada vez que se les ocurre una idea para mejorar la eficiencia.
Los trabajadores llegaron a confiar en este compromiso de no despido cuando, en 1988, las malas ventas del Nova redujeron la utilización de la capacidad a alrededor del 60%.%. Los trabajadores que ya no se necesitaban en la línea de montaje no fueron despedidos sino asignados a equipos kaizen y enviados a clases de formación.
Otro apoyo importante para el concepto de equipo de NUMMI es su sistema de clasificación de puestos radicalmente simplificado. Donde GM-Fremont tenía 18 clasificaciones de oficios calificados, NUMMI tiene dos. Donde GM-Fremont tenía 80 salarios por hora, en NUMMI todos los trabajadores de producción reciben la misma tarifa por hora, actualmente$ 17,85, independientemente de su trabajo, excepto que los jefes de equipo reciben 60 centavos adicionales. No hay bonificaciones basadas en la antigüedad, el rendimiento o el mérito. Por importante que sea el dinero, la equidad sigue siendo más importante para reducir las tensiones y los resentimientos.
La segunda característica distintiva del sistema NUMMI es la estandarización. Por lo general, las empresas estadounidenses abordan el empoderamiento de los equipos al permitir a los equipos una autonomía considerable en la forma en que realizan sus tareas. NUMMI, por el contrario, está obsesionada con los procedimientos de trabajo estandarizados. Considera lo que un gerente de NUMMI ha llamado «la interpretación inteligente y la aplicación de los estudios de tiempo y movimiento de Taylor» como la clave principal de su éxito. La referencia a Taylor puede ser discordante, pero encaja.
Trabajo estandarizado...
En GM-Fremont, los ingenieros industriales realizaban todo el análisis del tiempo y el movimiento y el diseño formal de los trabajos, y los trabajadores tendían a verlos con resentimiento o desprecio. El problema, como lo describió un dirigente sindical, era que la dirección asumió un «derecho divino» a diseñar puestos de trabajo como le pareciera conveniente. Los ingenieros industriales sin experiencia directa del trabajo más allá de la observación de cápsulas se encerraban en una habitación, reflexionaban sobre diversos potenciales del cuerpo humano, meditarían el resultado y promulgarían un diseño de tarea. O eso les pareció a los trabajadores, a quienes nadie consultó a pesar de estar íntimamente familiarizados con las dificultades específicas del trabajo en cuestión.
Normalmente, cuando un ingeniero industrial presentaba uno de estos trabajos diseñados pedánticamente a un supervisor, el supervisor lo aceptaba cortésmente y luego lo descartaba rápidamente en favor de la técnica más tradicional de «patear el culo y tomar nombres». El trabajador, a su vez, solía ignorar tanto al ingeniero como al capataz e hizo el trabajo como él o ella podía, excepto, por supuesto, cuando uno de ellos estaba mirando. Si un ingeniero industrial estaba «observando» (cronómetro y portapapeles en mano), la práctica habitual era reducir la velocidad y hacer que el trabajo pareciera más difícil. Toda la farsa formaba parte de un juego continuo de coerción y evasión. Multiplica este escenario por dos turnos y miles de trabajadores, y el resultado es cualquier cosa pero la producción racional de un coche de alta calidad.
En NUMMI, en contraste radical con el GM-Fremont, los propios miembros del equipo sostienen el cronómetro. Aprenden las técnicas de análisis, descripción y mejora del trabajo. Este cambio en el diseño y la implementación del trabajo estandarizado tiene implicaciones de gran alcance para la motivación y la autoestima de los trabajadores, para el equilibrio de poder entre los trabajadores y la dirección, y para la capacidad de la empresa de innovar, aprender y recordar.
El proceso de diseño del trabajo en sí es relativamente sencillo. Los miembros del equipo empiezan por cronometrar unos a otros con cronómetros, buscando la forma más segura y eficiente de hacer cada tarea a un ritmo sostenible. Escogen el mejor rendimiento, lo desglosan en sus partes fundamentales y, a continuación, exploran formas de mejorar cada elemento. A continuación, el equipo toma los análisis resultantes, los compara con los del otro turno en el mismo puesto de trabajo y escribe las especificaciones detalladas que se convierten en la definición de trabajo estándar para todos los miembros de ambos equipos.
Participar en el trabajo analítico y descriptivo del grupo implica que todos los miembros del equipo se comprometan a realizar cada tarea de forma idéntica. En cierto sentido, por lo tanto, el trabajo estandarizado es simplemente un medio de reducir la variabilidad en el desempeño de las tareas, lo que puede parecer un logro relativamente trivial. De hecho, sin embargo, la reducción de la variabilidad conduce a toda una serie de mejoras interconectadas:
- La seguridad mejora y las lesiones disminuyen porque los trabajadores tienen la oportunidad de examinar sistemáticamente todas las posibles fuentes de tensión y peligro.
- Los estándares de calidad aumentan porque los trabajadores han identificado el procedimiento más eficaz para cada trabajo.
- El control de inventario se hace más fácil y los costes de transporte de inventario disminuyen porque el proceso fluye con mayor fluidez.
- La rotación laboral se vuelve mucho más eficiente y equitativa, lo que hace que las ausencias sean menos problemáticas.
- La flexibilidad mejora porque todos los trabajadores son ingenieros industriales y pueden trabajar en paralelo para responder rápidamente a las demandas cambiantes. Por ejemplo, NUMMI puede convertirse a una nueva velocidad de línea en cuatro a seis semanas, un proceso que podría haber llevado fácilmente de seis meses a un año en GM-Fremont, con sus ingenieros recalculando frenéticamente miles de tareas e intentando imponer los nuevos estándares a los trabajadores. De hecho, GM-Fremont nunca intentó nada tan exigente como un cambio de velocidad de línea. Si los pedidos se rechazaban, GM-Fremont tenía que despedir todo un turno. La nueva capacidad de NUMMI para alterar la velocidad de la línea significa, entre otras cosas, que la planta puede acomodar una caída en los pedidos al ralentizar la producción.
Si los pedidos disminuyen, NUMMI puede ralentizar la línea de producción para producir menos automóviles. En la misma situación, GM-Fremont tuvo que despedir todo un turno.
- El trabajo estandarizado también tiene el beneficio general de dar el control de cada trabajo a las personas que mejor lo conocen. Empodera a la fuerza laboral. No es de extrañar que NUMMI descubriera que los trabajadores se habían adentrado en el proceso con bastante facilidad. Como dijo un gerente: «Entendieron la técnica porque se había hecho a durante años, y les gustó la idea porque ahora tenían la oportunidad de hacerlo por sí mismos».
... y mejora continua
Sin embargo, la ventaja más sorprendente del trabajo estandarizado es que proporciona a la mejora continua una base específica sobre la que basarse. Como dijo un gerente: «No puedes mejorar un proceso que no entiendes». En este sentido, la estandarización es la condición previa esencial para el aprendizaje.
De hecho, la estandarización no es solo un vehículo y una condición previa para la mejora, sino también un estímulo directo. Una vez que los trabajadores han estudiado y perfeccionado sus procedimientos de trabajo, los problemas con los materiales y el equipo salen a la superficie rápidamente. Además, dado que cada trabajador es ahora un experto, cada puesto de trabajo es ahora una estación de inspección y un centro de innovación.
En GM-Fremont, las sugerencias de los trabajadores eran aptas para encontrarse con un muro de ladrillo de indiferencia. En NUMMI, los ingenieros y gerentes deben funcionar como un sistema de apoyo en lugar de un sistema de autoridad. Cuando un equipo no puede resolver un problema por sí solo, puede buscar y obtener ayuda. Cuando un trabajador propone una innovación compleja, los ingenieros están disponibles para ayudar a evaluar la sugerencia y diseñar su implementación.
La diferencia entre el taylorismo tradicional y la versión NUMMI orientada al aprendizaje se asemeja a la diferencia entre el software informático diseñado para ser «a prueba de idiotas» y los tipos de sistemas informáticos que están destinados a aprovechar y mejorar las capacidades de sus usuarios. La primera «descualifica» la tarea del operador hasta tal punto que prácticamente elimina la posibilidad de error, pero también elimina la capacidad del operador para responder a eventos impredecibles, utilizar el sistema de formas novedosas o adaptarlo a nuevas aplicaciones. El sistema a prueba de idiotas puede ser fácil de usar, pero también es estático y aburrido. Los sistemas de apalancamiento exigen al operador. Toman tiempo para aprender y requieren pensamiento y habilidad para usarlos, pero son inmensamente flexibles, receptivos y satisfactorios una vez dominados.
La diferencia es aún más profunda. En GM-Fremont, donde los procedimientos de trabajo estaban diseñados para ser a prueba de idiotas, la relación entre el sistema de producción y el trabajador era contradictoria. Las normas y la jerarquía estaban ahí para coaccionar el esfuerzo de los trabajadores renuentes. Si el sistema funcionaba como se esperaba y el operador era lo suficientemente tratable y poco imaginativo, ambos juntos podrían resultar un producto justo. Sin embargo, era poco lo que el operador podía mejorar, y el papel del sistema era totalmente rígido hasta que se averió, con lo cual todo se detuvo hasta que llegó un especialista.
En NUMMI, la relación de los trabajadores con el sistema de producción es cooperativa y dinámica. En lugar de eludir la inteligencia y la iniciativa del usuario, el sistema de producción está diseñado para aprovechar al máximo el potencial de colaboración latente entre los trabajadores y el sistema.
Los programas de sugerencias ilustran los dos enfoques del diseño de tecnología organizacional. En muchas empresas, los programas de sugerencias son opacos y a prueba de idiotas. Están diseñados principalmente para descartar ideas tontas, y los criterios básicos de revisión, la identidad de los jueces, el estado de las propuestas y los motivos del rechazo son una caja negra para los trabajadores. Como era de esperar, muchos de estos programas avanzan o se extinguieron por completo.
En NUMMI, el programa está diseñado para fomentar un flujo creciente de sugerencias y ayudar a los trabajadores a ver y comprender los criterios, los evaluadores, el proceso, el estado y los resultados. Al igual que un sistema informático diseñado para aprovechar en lugar de deshabilidades, el programa ayuda a los empleados a formar un modelo mental del funcionamiento interno del programa. No es de extrañar que los trabajadores hayan hecho más de 10.000 sugerencias en 1991, de las cuales más de 80% se implementaron.
En sistemas que descapacitan y son a prueba de idiotas, la tecnología controla, de hecho, domina a los trabajadores. En los sistemas diseñados para lo que los expertos llaman usabilidad, el operador aprende y «enseña» la tecnología. Utilizando herramientas analíticas aprendidas, su propia experiencia y la experiencia de líderes e ingenieros, los trabajadores crean un estándar consensuado que enseñan al sistema mediante la redacción de descripciones de puestos. A continuación, el sistema enseña estas normas a los trabajadores, quienes, a continuación, mediante análisis, consultas y consenso más profundos, realizan mejoras adicionales. La reiteración continua de este proceso disciplinado de análisis, estandarización, reanálisis, refinamiento y restandardización crea un sistema de mejora continua intensamente estructurado. Y la característica más destacada de esta burocracia es el aprendizaje, no la coerción.
Esta orientación al aprendizaje captura la imaginación. Personas a las que nadie había pedido resolver un problema, trabajadores que nunca terminaron la escuela secundaria, hombres y mujeres que habían pasado 20 años o más en la industria automotriz sin un solo día de formación fuera del trabajo se vieron atrapados repentinamente en el análisis estadístico del tiempo de inactividad de los equipos, reuniendo a Pareto gráficos. Un trabajador informó que hizo literalmente cien gráficos antes de acertarle uno.
Una mujer del comité de seguridad del taller de carrocería describió cómo aplicó técnicas kaizen a su cocina en casa después de un incendio en su estufa. Analizó el diseño de la cocina, instaló un extintor de incendios y reubicó sus tapas de ollas para poder usarlas para asfixiar las llamas. En resumen, se sometió a sí misma y a su espacio de trabajo a domicilio a los procedimientos formales de resolución de problemas que había aprendido en la planta de NUMMI.
La característica paradójica que tienen en común estas historias es su entusiasmo por una forma de comportamiento disciplinado que tanto la teoría como la práctica pasada parecen descartar. Esta paradoja surge de nuestra incapacidad para distinguir entre lo que los sistemas de producción burocráticos y tayloristas lata ser y lo que, lamentablemente, han sido habitualmente.
La psicología del trabajo
La cadena de razonamiento mediante la cual la normalización disciplinada conduce inevitablemente a la coerción, al resentimiento, a la resistencia y a una mayor coerción parece convertir el taylorismo y la burocracia en lo que el sociólogo Max Weber llamó una jaula de hierro. El taylorismo y la burocracia pueden tener un efecto devastador en la innovación y la motivación, según el razonamiento, pero su eficiencia técnica y su poder para hacer cumplir el cumplimiento parecen ser las herramientas perfectas para tratar con los empleados que se supone que son recalcitrantes. El propio Taylor, al menos ocasionalmente, respaldó esta visión coercitiva del trabajo. La cursiva erizándose, escribió una vez, «Es sólo a través del cumplida estandarización de los métodos, cumplida adopción de los mejores implementos y condiciones de trabajo, y cumplida cooperación que este trabajo más rápido puede estar asegurado. Y el deber de hacer cumplir la adopción de normas y hacer cumplir esta cooperación recae en el gestión solo».
En este contexto, no es de extrañar que la mayoría de los directivos y académicos, al menos en Occidente, hayan llegado a creer que el taylorismo y la burocracia alienarán inevitablemente a los trabajadores y desperdiciarán su potencial humano. Pero la suposición psicológica que subyace a esta expectativa es que los trabajadores son incapaces de demorar la gratificación. Los directivos parecen creer que el rendimiento solo mejorará a medida que el trabajo se parezca cada vez más al juego libre, nuestro modelo de actividad intrínsecamente motivadora. De hecho, es un axioma elemental de la economía que el trabajo es algo que los trabajadores siempre evitarán.
NUMMI demuestra el error de imputar la psicología infantil a los trabajadores. Las entrevistas con los miembros del equipo de NUMMI sugieren, de hecho, que toda esta acumulación histórica de supuestos oculta tres fuentes de motivación adulta que el sistema de producción NUMMI aprovecha con éxito:
En primer lugar, el deseo de excelencia.
En segundo lugar, un sentido maduro del realismo.
En tercer lugar, la respuesta positiva al respeto y la confianza.
El primero de ellos, el deseo de hacer un buen trabajo, el instinto de mano de obra, aparece una y otra vez en las conversaciones con los trabajadores. El sistema de producción NUMMI y la formación que lo acompañaba aumentaban tanto la competencia real de los trabajadores como sus sentimientos de competencia. Los trabajadores hablan mucho de experiencia, orgullo y autoestima. Un funcionario de la UAW nombró «construir un producto de calidad» como uno de los objetivos estratégicos que el sindicato encontró más convincentes en NUMMI. Quizás la historia más sorprendente sobre el orgullo en todas las entrevistas provino de un líder de equipo:
Antes, cuando veía una camioneta Chevy, me reía entre dientes y pensaba: «Te mereces esa porquería si eras lo suficientemente estúpida como para comprar una». Me daba vergüenza decir que trabajaba en la planta de Fremont. Pero cuando estuve en el Acuario de Monterey hace unos fines de semana, dejé mi tarjeta de presentación (los gruñidos incluso tienen tarjetas de visita) en el parabrisas de un Nova estacionado con una nota que decía: «Ayudé a construir esta». Nunca antes me sentía orgullosa de mi trabajo.
Los trabajadores que alguna vez se avergonzaban de sus productos ahora se inclinan a informar a los propietarios de automóviles que «ayudaron a construir este».
El segundo elemento de motivación es un sentido maduro del realismo; en este caso, el entendimiento de que, a menos que NUMMI mejore constantemente su rendimiento, los competidores se llevarán su mercado y los puestos de trabajo de sus trabajadores. Una teoría psicológica útil no puede suponer que los trabajadores estén tan cautivos del principio del placer que su única fuente de motivación sea el placer inmediato de un trabajo intrínsecamente significativo. La evidencia sugiere que al menos algunos de los trabajadores de NUMMI están motivados poderosamente por el simple reconocimiento de que la competencia internacional ahora los obliga a «ganar su dinero a la antigua usanza».
Algunos trabajadores toman una poderosa motivación de saber que tienen que «ganar su dinero a la antigua usanza».
En igualdad de condiciones, el trabajo que es intrínsecamente motivador, a diferencia del mundano y rutinario, es mejor que el trabajo que no lo es, pero los trabajadores de NUMMI reconocen que otras cosas son no iguales, y son realistas en su reconocimiento de haber tenido un sorteo desafortunado en términos de educación y oportunidades. Ven el montaje de automóviles como un trabajo que nunca puede tener mucho valor intrínseco, pero entienden que sus propios niveles de motivación pueden variar de muy negativos, en GM-Fremont, a fuertemente positivos, en NUMMI.
«Lo que tenemos aquí no es una utopía obrera», dijo un trabajador de NUMMI. «Trabajar en una línea de montaje en una fábrica de automóviles sigue siendo un trabajo pésimo... Queremos seguir minimizando las partes negativas del trabajo utilizando el nuevo sistema». A pesar de que este trabajo carece del interés intrínseco que atraería a un trabajador en un domingo libre, por ejemplo, la diferencia entre los niveles de motivación en NUMMI y en el GM-Fremont marca la diferencia entre el nivel de clase mundial y el peor de su clase.
La tercera explicación del aumento de la motivación es el respeto y la confianza que la dirección muestra a los trabajadores en las operaciones en curso de NUMMI. Por ejemplo, cuando la planta comenzó a funcionar, los nuevos gerentes de NUMMI respondieron rápidamente a las solicitudes de los trabajadores y representantes sindicales de artículos como guantes y alfombrillas nuevos, lo que sorprendió a los trabajadores que solían ver que solicitudes como estas se convertían en batallas por prerrogativas de gestión.
Después de unos meses de conseguir todo lo que pedían, los trabajadores y los representantes sindicales empezaron a pensar en formas de corresponder. Finalmente, decidieron que las fuentes de agua cromadas eran innecesarias y le dijeron a la gerencia que habían encontrado algunas de plástico por la mitad del precio. Unas semanas más tarde, la dirección aumentó la apuesta una vez más al dar a los equipos de trabajo sus propias cuentas para que pudieran pedir suministros para los miembros del equipo sin la aprobación previa de la gerencia. Este tipo de comportamiento llevó a los trabajadores a concluir que sí compartían objetivos comunes con la dirección.
Poder y empoderamiento
El sistema de producción NUMMI nos enfrenta a un conjunto de procedimientos formalizados que parecen diseñados no principalmente como instrumentos de dominación sino como elementos de técnica productiva que todos los participantes reconocen como herramientas en su propio interés colectivo. Gestión y apoyo laboral del sistema NUMMI. De hecho, el primer y abrumador hecho que surge de las entrevistas es que nadie en NUMMI quiere volver a los viejos tiempos de GM-Fremont. Sean cuales sean sus críticas y sus posiciones, todos sienten que NUMMI es un entorno de trabajo muy superior.
La política de no despido de NUMMI, los esfuerzos de gestión para crear una atmósfera de confianza y respeto, el sistema de producción NUMMI, especialmente el estímulo de su orientación al aprendizaje, ayudan a explicar esta actitud. Sin embargo, más allá de estas políticas formales, hay dos factores más que ayudan a explicar el éxito de NUMMI con los trabajadores. La primera de ellas, como hemos visto, es la psicología del trabajo. La última pieza del rompecabezas tiene que ver con el poder.
Hay dos tipos de poder a considerar: el poder jerárquico dentro de la organización y el equilibrio de poder entre el trabajo y la dirección. NUMMI adopta un enfoque distintivo para ambos.
En términos de capas jerárquicas, NUMMI es una planta de fabricación estadounidense bastante típica y, en este sentido, así como en los procedimientos de flujo de trabajo, es una organización muy burocrática. La estructura de NUMMI no es plana. Tiene varias capas bien pobladas de mandos intermedios. Pero coherente con la idea de convertir las tecnologías de la coerción en herramientas de aprendizaje, la función jerárquica de NUMMI no es control sino apoyo.
Las decisiones en NUMMI se toman por amplio consenso vertical y horizontal. A primera vista, la toma de decisiones parece ser algo más centralizada que en la mayoría de las fábricas estadounidenses, pero esto se debe a que la toma de decisiones basada en el consenso atrae a niveles cada vez más altos en un diálogo, no porque los niveles más altos ejerzan un mayor control unilateral. Ambos extremos del espectro jerárquico se ven enredados en más discusiones de toma de decisiones de lo que cualquiera de ellos experimentaría en una organización convencional.
El contraste con los enfoques populares del empoderamiento es sorprendente. En una empresa de telecomunicaciones estadounidense, la organización modelo es hoy una planta de 90 trabajadores en equipos autogestionados, todos ellos bajo la dirección de un solo gerente de planta. El antiguo modelo de la empresa incluía una gran cantidad de gerentes intermedios cuya función clave era el mando y el control, por lo que es fácil comprender el efecto inspirador del nuevo enfoque. Pero en NUMMI, los mandos intermedios son capas de experiencia, no de derechos de mando, y si los mandos intermedios tienen autoridad, es la autoridad de la experiencia, el dominio y la capacidad de entrenar.
En cuanto al segundo aspecto del poder, muchos observadores han asumido que la intensa disciplina de las operaciones al estilo Toyota requiere un control administrativo completo sobre los trabajadores y la eliminación de la fuerza laboral independiente y el poder sindical. Pero en NUMMI, el poder de los trabajadores y del sindicato local sigue siendo considerable. En cierto modo, su poder ha aumentado. De hecho, puede ser que el modelo NUMMI solo haya tenido éxito porque de este alto nivel de poder obrero y sindical.
Lo que hace que el sistema de producción NUMMI sea tan eficaz es su capacidad para hacer visibles inmediatamente los problemas de producción y movilizar el poder del trabajo en equipo. Implementadas con confianza y respeto, estas dos características del sistema crean un verdadero empoderamiento. Esgrimidas autocráticamente, tendrían el efecto contrario. El control visible podría convertirse fácilmente en vigilancia ubicua. El trabajo en equipo podría convertirse en un medio de movilizar la presión de los compañeros. Un nivel saludable de desafío podría degenerar en estrés y ansiedad.
Por lo tanto, el sistema de producción NUMMI proporciona a los gerentes un enorme control potencial sobre los trabajadores. Con este poder potencial a mano y bajo presión para mejorar el rendimiento empresarial, existe el peligro real de que la relación tarde o temprano vuelva a caer en el viejo patrón coercitivo.
Pero tal deslizamiento tendría un impacto negativo inmediato y sustancial en el desempeño empresarial, porque la mano de obra respondería de la misma manera. Una fuerza laboral alienada borra la base misma de la mejora continua y seca el flujo de sugerencias de los trabajadores que la alimentan. Y la falta de amortiguadores de inventario significa que los trabajadores desafectados podrían detener fácilmente todo el sistema de producción justo a tiempo. Además del poder positivo de los trabajadores para mejorar la calidad y la eficiencia, el sistema también otorga a los trabajadores un enorme poder negativo para generar disrupción la producción.
El nuevo sistema proporciona a los trabajadores un gran poder positivo para mejorar la producción y un gran poder negativo para interrumpirla.
En otras palabras, el sistema de producción de NUMMI aumenta el poder tanto de la dirección sobre los trabajadores como de los trabajadores sobre la dirección.
Un sistema tan cargado necesita un sólido proceso de gobernanza en el que las voces de la gerencia y el trabajo puedan escucharse claramente y armonizarse eficazmente en cuestiones políticas de alto nivel, así como en cuestiones operativas del equipo de trabajo. El sindicato da voz a los trabajadores.
Cuando, por ejemplo, los trabajadores se sentían frustrados por lo que consideraban favoritismo en la selección de líderes de equipo por parte de la dirección, el sindicato eliminó en gran medida el problema negociando un proceso de selección conjunto de la dirección sindical basado en pruebas objetivas y criterios de desempeño.
Como dijo un funcionario de la UAW: «La clave del éxito de NUMMI es que la dirección renunció a parte de su poder, a algunas de sus prerrogativas tradicionales. Si los directivos quieren motivar a los trabajadores para que contribuyan y aprendan, tienen que renunciar a algo de su poder. Si los gerentes quieren que los trabajadores confíen en ellos, debemos tener entre 50 y 50 años para tomar la decisión. No tomes la decisión y digas: 'Confía en mí'».
Los dirigentes sindicales y la alta dirección se reúnen periódicamente dentro y fuera del sitio para considerar una amplia gama de cuestiones políticas que van mucho más allá del ámbito tradicional de la negociación colectiva. El local sindical ha adoptado el concepto NUMMI y sus objetivos. Sin embargo, su capacidad y voluntad de actuar como vehículo para las preocupaciones de los trabajadores contribuye en gran medida a la eficacia a largo plazo de la organización.
La capacidad de NUMMI para mantener su historial de productividad, calidad y mejora depende ahora de la motivación de los trabajadores, que a su vez se basa en la percepción y la realidad de la influencia, el control y el trato equitativo. Es de interés propio de la dirección que cualquier abuso de las prerrogativas de gestión se impongan sanciones rápidas y determinadas. La contribución del poder positivo del trabajo depende de la realidad de su poder negativo.
De esta manera, el sindicato no solo sirve a los intereses especiales de los trabajadores, sino que también sirve a los objetivos estratégicos más amplios de la empresa al privar efectivamente a la administración del dominio absoluto y ayudar a mantener la disciplina administrativa.
El empoderamiento es un enfoque poderoso y cada vez más popular para revitalizar a las organizaciones moribundas. El caso NUMMI señala dos de los peligros potenciales del empoderamiento y sugiere formas de superarlos.
En primer lugar, el empoderamiento de los trabajadores degenera en explotación si los cambios en el primer nivel de la administración no se ven reforzados continuamente por cambios en toda la jerarquía de gestión. Se necesita una voz fuerte de los empleados para garantizar que las inquietudes del taller se escuchen en todos los niveles de la administración. Sin ella, el nuevo poder de los trabajadores es poco más que el poder de ganar más dinero para la administración.
En segundo lugar, el empoderamiento de los trabajadores degenera en abandono si los equipos de trabajo no obtienen las herramientas adecuadas, la capacitación para su uso y el apoyo en su implementación. El trabajo estandarizado, la formación exhaustiva en la resolución de problemas, una jerarquía de gestión receptiva y las funciones especializadas de apoyo son factores clave para el éxito de las estrategias de empoderamiento.
La disciplina de tiempo y movimiento taylorista y las estructuras burocráticas formales son esenciales para la eficiencia y la calidad de las operaciones rutinarias. Pero estos principios de diseño organizacional no tienen por qué llevar a rigidez y alienación. NUMMI señala el camino más allá de Taylor como villano al diseño de una burocracia verdaderamente orientada al aprendizaje.
— Escrito por Paul Adler