Obtener una visión más clara de la huella de carbono de su empresa
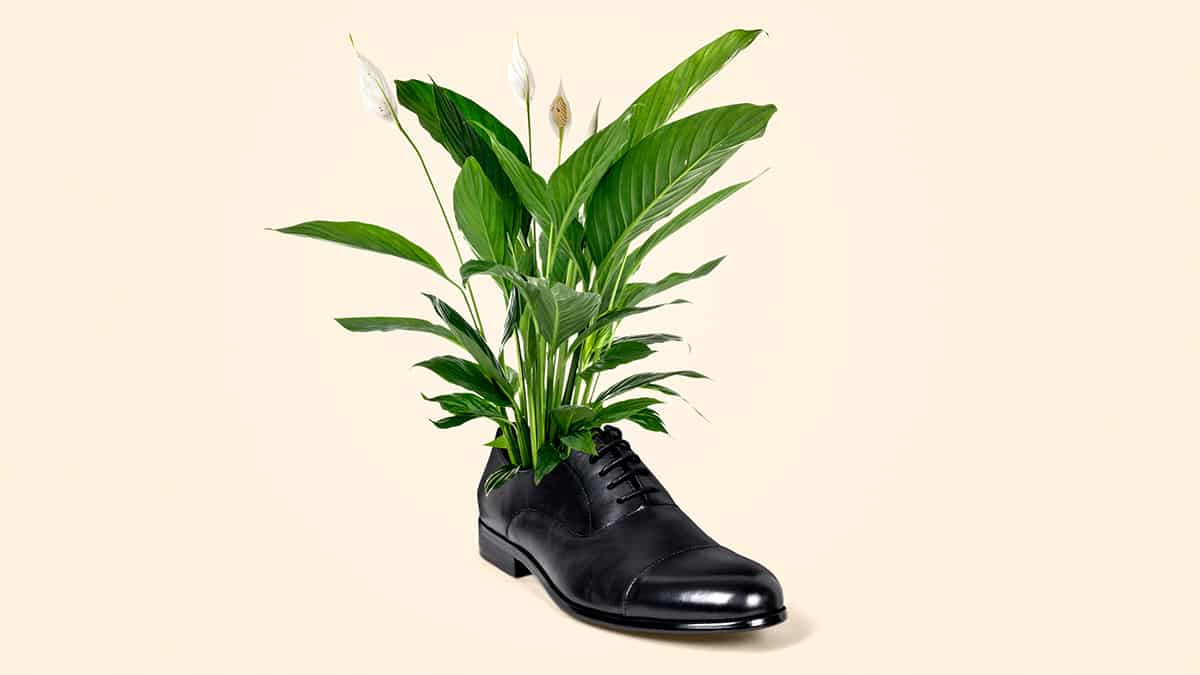
por Robert S. Kaplan,
Resumen:
La contabilidad electrónica de responsabilidad es una nueva técnica que ayudará a los clientes a tener en cuenta la huella medioambiental de un producto en sus decisiones de compra y ayudará a crear una dinámica de competencia que conduzca a reducir la producción de carbono. Este artículo describe dos estudios piloto, realizados por un fabricante asiático de neumáticos y un productor de cemento alemán, que ilustran cómo el enfoque de la responsabilidad electrónica puede lograrlo.
___
A pesar de que la legislación, la regulación y los impuestos climáticos avanzan con lentitud, algunas empresas responden voluntariamente a las expectativas de sus accionistas y clientes, sensibles desde el punto de vista medioambiental, iniciando el proceso para descarbonizar sus cadenas de suministro. Contabilidad electrónica de responsabilidad, presentado en la edición de noviembre de 2021 de Harvard Business Review, permite a las organizaciones basarse en principios contables bien establecidos para abordar las deficiencias actuales a la hora de medir y reducir las emisiones de carbono en las cadenas de suministro complejas.
Los enfoques estándar de medición del carbono, en particular los enfoques recomendados en el Protocolo de gases de efecto invernadero (GHGP) y las evaluaciones del ciclo de vida (LCA) utilizadas para las declaraciones de productos medioambientales (EPD), son cálculos jerárquicos de arriba hacia abajo en los que cada empresa busca estimar las emisiones de todas las demás empresas de su cadena de suministro. Los cálculos son problemáticos, ya que las estimaciones suelen proporcionarlas analistas externos basándose en los datos promedio del sector (secundarios), no en las emisiones reales en las que incurren los numerosos proveedores de la empresa. Los enfoques estándar también exigen que cada empresa reproduzca los cálculos realizados por todas las demás en su cadena de valor, un proceso caro y redundante con conteo múltiple de las mismas emisiones.
Sin embargo, la contabilidad electrónica de responsabilidad evalúa la intensidad de carbono de un producto (por ejemplo, en kg de CO2 por unidad de producto) a través de un recursivo y cálculo descentralizado de la información. Cada empresa solo necesita datos de emisiones de sus proveedores inmediatos y de sus propias operaciones para asignar la intensidad de carbono a la producción de sus productos de venta. A continuación, la empresa comparte la información de carbono del producto integrada con sus clientes inmediatos, quienes realizan los mismos cálculos con los insumos comprados y sus propias operaciones de transmisión en etapas posteriores de la cadena de valor. En conjunto, el enfoque rastrea la huella de carbono total de un producto desde la cuna hasta el cliente, desde la extracción de las materias primas utilizadas en su fabricación hasta las emisiones de procesamiento y transporte, hasta las emisiones de la entrega en la última milla.
De esta forma, y de forma análoga a los cálculos estándar del valor añadido, la contabilidad electrónica hace que cada empresa solo rinda cuentas por sus emisiones directas y por las emisiones ascendentes reales incluidas en los insumos que compra a los proveedores. Cualquier reducción en las emisiones directas de una empresa o en las emisiones de sus proveedores reducirá en consecuencia los balances de carbono de los productos que se vendan y distribuyan a los clientes. Además, los datos de emisiones de todos los productos de cada entidad de una cadena de valor pueden, en principio, agregarse a los informes a nivel empresarial sobre las emisiones totales de carbono compradas, producidas y vendidas, de forma muy parecida a un declaración financiero. Los auditores y los analistas independientes pueden verificar esos informes a nivel de entidad, lo que facilita inversiones más eficaces en financiación ecológica.
Si bien es intuitiva, la contabilidad electrónica de responsabilidad aún no se ha adoptado ampliamente en la práctica, ya que las empresas siguen utilizando los engorrosos e indirectos enfoques de GHGP y LCA. En este artículo, proporcionamos detalles sobre cómo las empresas globales que adoptaron de forma temprana han obtenido y aprovechado la información sobre carbono de los proveedores y sus propias operaciones para mejorar su propia huella de carbono y ofrecer a los clientes la oportunidad de mejorar la suya.
Gestión de las emisiones de carbono
La primera empresa es Giti Tire Group, con sede en Singapur, una de las mayores compañías de neumáticos del mundo, con clientes en más de 130 países e ingresos anuales aproximados de 2500 millones de dólares. Giti utiliza proveedores grandes y conocidos para sus materias primas y productos semiacabados, pero, como la mayoría de las empresas, se basó en los promedios del sector para calcular sus emisiones de alcance 3. Incluso esta información era difícil de encontrar. Una de las principales fuentes de datos sobre los datos de emisiones de la fabricación de neumáticos proviene de una tesis de máster de 2016 de un estudiante en Finlandia. Estos datos estáticos y ahora anticuados siguieron siendo la base de gran parte de las estimaciones de emisiones del propio sector.
Tras conocer el método de responsabilidad electrónica, el CEO de la empresa pidió a Francois Petiot, director de control de calidad de Giti, que desarrollara un proyecto piloto en la filial de la empresa en Indonesia, PTGT. Petiot decidió calcular las emisiones de un solo producto, el neumático de pasajeros estándar, que representaba aproximadamente el 30% de la capacidad de producción de neumáticos de PTGT. Pero incluso esto parecía una tarea abrumadora al principio, ya que el neumático estaba compuesto por más de 200 materias primas.
Para que el desafío fuera manejable, aplicó el» Regla de Willie Sutton», que lleva el nombre del ladrón de bancos que defendió su elección de profesión declarando «ahí es donde está el dinero». Petiot aplicó la regla estimando las emisiones generadas para producir cuatro materiales de entrada clave: caucho sintético, caucho natural, negro de carbón (un polvo parecido al hollín que se utiliza para reforzar el neumático) y acero. En conjunto, estos componentes representaban el 86% del peso del neumático y proporcionaban un punto de partida para consultar los datos iniciales de los proveedores. (Consulte la primera columna de la tabla 1 para ver las entradas de los neumáticos de los turismos según porcentaje del peso).
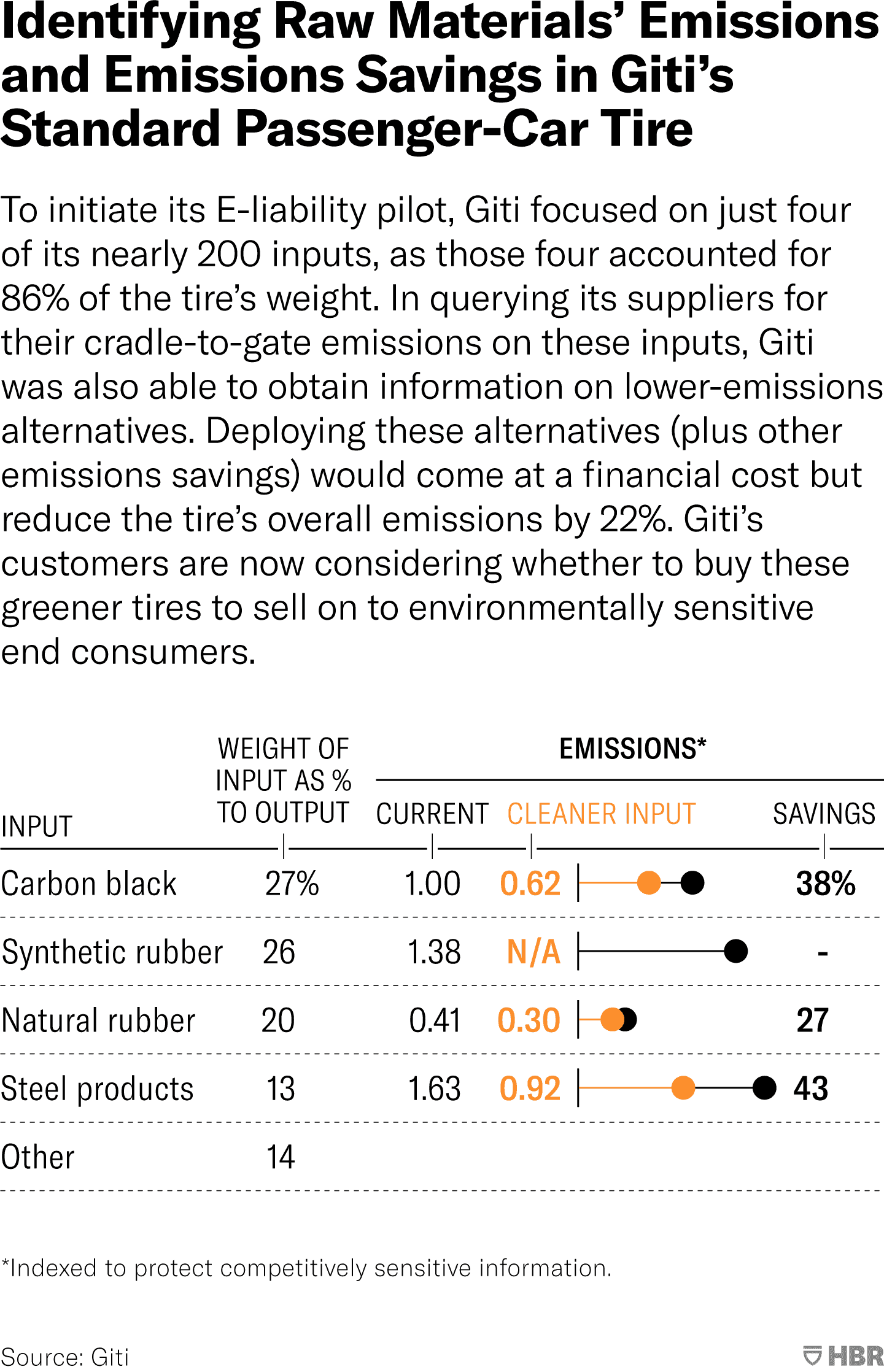
Petiot contrató a tres directivos para el equipo interno del estudio piloto. Elegido por su experiencia específica, pero también por su pasión por la reducción de emisiones y su motivación para contribuir más allá de su trabajo diario, el equipo contactó con los proveedores de las cuatro materias primas clave para explicarles el piloto de responsabilidad electrónica y solicitarles sus datos de emisiones.
Aunque los proveedores estaban dispuestos a cooperar, inicialmente solo unos pocos podían compartir las emisiones específicas de los productos que vendían a PTGT. Por lo demás, el equipo piloto se basó en los factores de emisión anunciados públicamente, normalmente tomados de los proveedores declaraciones de productos medioambientales. El equipo incluyó las estimaciones de los proveedores en una hoja de cálculo dinámica de responsabilidad electrónica. La segunda columna de la tabla 1 proporciona valores indexados de CO2 emisiones de las entradas de neumáticos de turismos.
A continuación, Petiot y su equipo se dedicaron a desarrollar un diagrama de flujo para identificar las principales fuentes de emisiones a la hora de fabricar el neumático de pasajeros. Se centraron en los dos procesos que consumen más energía: la composición (mezclar los materiales que fabrican el neumático) y el curado (aplicar presión y calor para formar el neumático). A continuación, calcularon las emisiones directas de la empresa asociadas a estas actividades, junto con las emisiones inherentes a su consumo de energía.
Como último paso, el equipo asignó las emisiones adquiridas por el proveedor y las emisiones incurridas en el sitio al neumático estándar de un automóvil de pasajeros y calculó el tonelaje de carbono por neumático. Este paso reveló las emisiones por neumático que podían transferirse a los propios clientes de PTGT cuando se vendiera el neumático.
Inicialmente, Petiot esperaba que calcular los datos de emisiones específicos de los neumáticos de PTGT fuera un desafío. Sin embargo, el proyecto piloto solo había durado unos dos meses y Petiot se dio cuenta de que ya habían registrado gran parte de los datos necesarios en las divulgaciones presentadas a los reguladores. La tarea en cuestión no consistía entonces en empezar de cero, sino en comprobar la exactitud de sus datos ya existentes, sobre todo teniendo en cuenta que esas cifras no estaban controladas por ningún organismo de auditoría, y luego, siempre que fuera posible, obtener datos específicos del lote. Este proceso había permitido una primera aproximación al método de responsabilidad electrónica, que podría perfeccionarse posteriormente con datos más precisos de sus proveedores y sus propios procesos.
Con una primera aprobación de la responsabilidad electrónica de un neumático estándar de un turismo, Petiot y su equipo empezaron a identificar las áreas en las que podían reducir las emisiones. «Durante el proyecto piloto, descubrimos que nuestras compras de electricidad y negro de carbono se habían realizado sin visibilidad de sus emisiones de GEI, que no eran óptimas», dijo. «Al medir las emisiones de cada uno de los proveedores, podríamos identificar dónde podrían realizarse cambios para reducir la huella de carbono de nuestros neumáticos».
Cuando sus proveedores se dieron cuenta de que PTGT había invertido activamente en reducir su huella de carbono, empezaron a proponer sus propias alternativas con menos emisiones. El proveedor de productos negros como el carbono sugirió utilizar métodos de producción circulares que redujeran las emisiones un 38% mediante la optimización del uso de los recursos a lo largo del ciclo de vida de los productos. El proveedor de caucho natural podría reducir las emisiones un 27% si cambiara de un proveedor de plantaciones nacionales a uno más productivo en Tailandia. El proveedor de acero podría reducir las emisiones en más de un 43% sustituyendo el mineral virgen que había que fundirse en hornos de oxígeno básico por acero reciclado que se procesaría en hornos de arco eléctrico con bajas emisiones. (Consulte la tercera columna, Ahorro de emisiones, en la tabla 1 para conocer las ventajas de las alternativas de insumos «más limpias»).
El equipo de PTGT también examinó dónde podían reducir las emisiones en cada paso del proceso de fabricación, especialmente en las que consumían mucha energía. El equipo estimó que utilizar energía solar in situ para reemplazar parte de la electricidad de la red reduciría las emisiones de energía compradas un 18%, aunque se trataba de una estimación superior que no incluía las emisiones ascendentes de la fabricación de paneles solares. Y el uso de calderas de gas natural más nuevas y eficientes desde el punto de vista energético podría reducir las emisiones hasta otro 6%.
En total, Petiot y su equipo estimaron que, trabajando con los proveedores y ajustando sus procesos internos, podrían, en una primera pasada, reducir las emisiones de sus neumáticos de pasajeros en aproximadamente un 22%. Empezaron a estudiar las oportunidades con materiales de entrada adicionales, como talón, nailon, poliéster y ciertos productos químicos, lo que amplió la cobertura hasta el 95% de la masa del neumático. Además, como resultado de su proyecto piloto, PTGT inició una colaboración con uno de sus proveedores de acero para obtener cordones de acero de bajas emisiones y alta durabilidad que pudieran reducir el uso de combustibles fósiles a lo largo de la vida útil de un vehículo.
Cuando PTGT llevó los resultados del proyecto piloto a uno de sus principales clientes, el fabricante de automóviles quedó intrigado. Ha pedido a la empresa de neumáticos que amplíe el proyecto piloto a sus fábricas de China que suministran directamente a los coches del fabricante de automóviles. Con ese servicio de atención al cliente, PTGT espera poder hacer de la descarbonización una ventaja competitiva.
Informar sobre las intensidades de carbono del producto
La segunda empresa que estudiamos fue la de Alemania Heidelberg Materials (HM), uno de los principales productores de cemento del mundo. La producción de cemento contribuye en gran medida al calentamiento global, responsable de hasta 8% del CO mundial2 emisiones. HM quería explorar formas de reducir su contribución a esa cifra.
Siguiendo la regla de Willie Sutton, HM se centró en el principal contribuyente a las emisiones relacionadas con el cemento: la conversión de la piedra caliza (CaCO)3) en clínker (CaO), el ingrediente principal del cemento Portland tradicional. Las emisiones del proceso de esta conversión representan dos tercios de las emisiones totales de la producción de cemento Portland. HM, al igual que otros productores de cemento, sustituía cada vez más materiales cementosos con bajo contenido de carbono, como las cenizas volantes y la escoria, por clínker con alto contenido de carbono. Pero HM tuvo que cumplir con varios estándares reglamentarios para tener en cuenta las emisiones incorporadas en estos materiales.
HM ya estaba elaborando declaraciones de productos medioambientales para cumplir con los requisitos reglamentarios de los productos de cemento. Pero porque cada EPD estima el CO2 emisiones de un producto específico, producido en una planta específica, en un período específico, el proceso tarda un tiempo considerable en completarse para cada producto y cualquier cambio en el proceso de producción, el diseño o el abastecimiento requiere la producción y validación de una nueva EPD. El equipo medioambiental de HM quería un sistema de medición de la gestión en tiempo real que reflejara el contenido real de carbono de las recetas actuales de cemento, los procesos de producción, la compra de energía y el abastecimiento de materiales.
HM buscó un sistema de medición alternativo para asignar una parte adecuada de las emisiones a nivel de planta, relacionadas con la energía y compradas a cada una de las producciones de la planta. El sistema siguió un proceso de varios pasos para asignar las emisiones a los productos, similar a un enfoque de cálculo de costes basado en las actividades.
En primer lugar, accedió a los datos existentes sobre las emisiones ascendentes de combustibles, piedra caliza y escoria, los principales insumos comprados, junto con la electricidad. Luego, estimó las emisiones directas de la planta, principalmente las del combustible utilizado para calentar el horno para la reacción química entre la piedra caliza y el clínker, y el CO2 procesar las emisiones de la propia reacción. A continuación, el sistema asignó las emisiones directas e indirectas a tres procesos principales de la planta: producción de clínker, trituración de escorias y molienda de cemento. Como último paso, el sistema asignó las emisiones de los tres procesos a la producción de la planta, utilizando los factores adecuados, como el contenido relativo de clínker o escoria del producto y su tiempo de molienda.
La tabla 2 presenta los datos de tres producciones representativas de cemento, cementos 1 a 3. El cemento 2, que sustituye parte del contenido de clínker por escoria, consume un 15% menos de carbono que el cemento 1, pero necesita más tiempo de secado para lograr toda su resistencia estructural. El cemento 3, que utiliza mucha más escoria en la mezcla de cemento, tiene una intensidad de carbono un 58% más baja que el cemento 1 y tiempos de secado aún más largos que los cementos 1 y 2 para lograr toda su resistencia estructural.
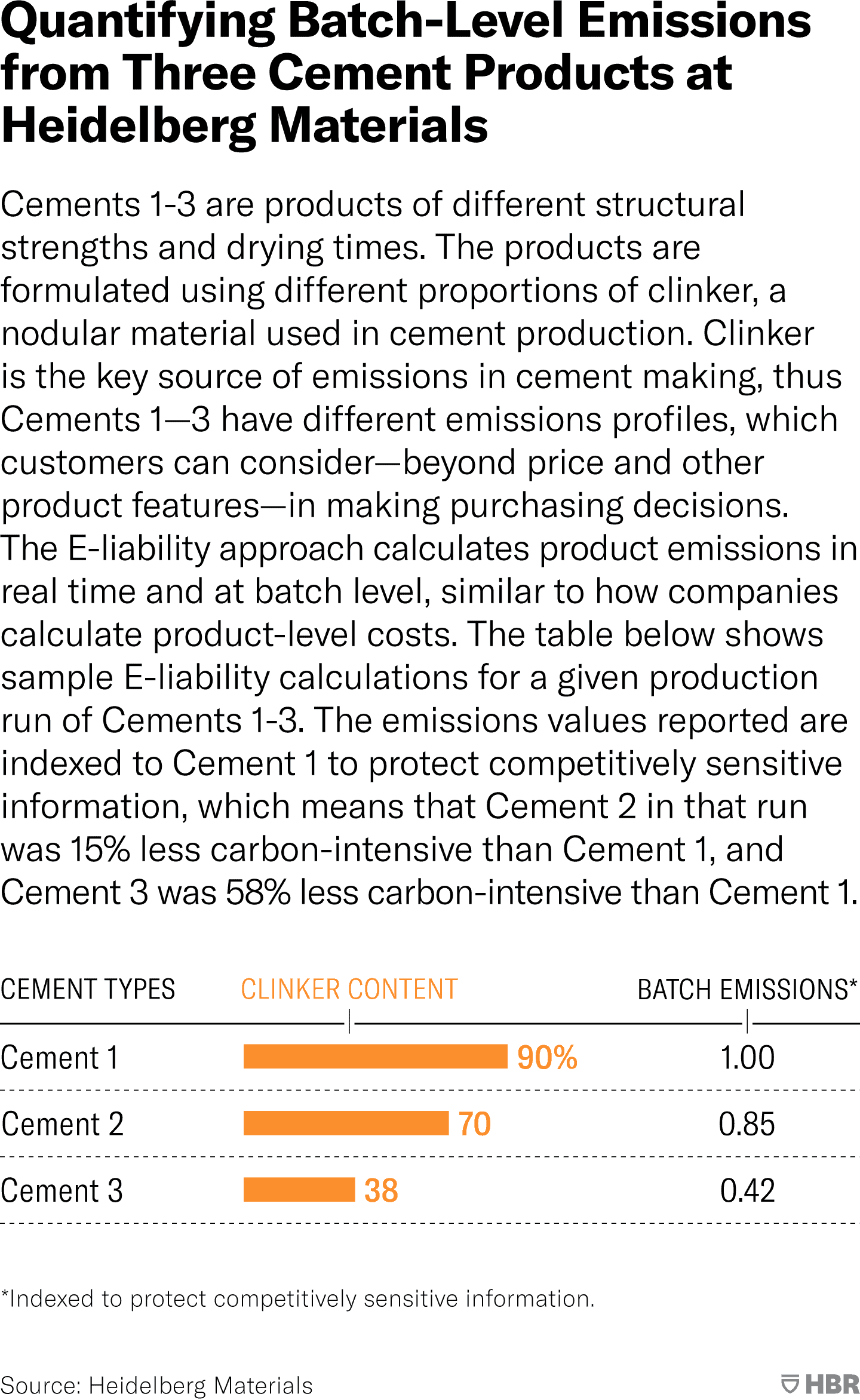
El sistema de contabilidad de carbono permite a HM informar a los clientes de las emisiones creíbles y oportunas a nivel de producto, basándose en el proceso de producción, la receta y el abastecimiento reales del producto. Los clientes pueden entonces tomar decisiones informadas en función del precio del producto, su intensidad de carbono, su tiempo de secado y su rendimiento estructural.
. . .
Estos dos estudios de casos ilustran cómo las empresas pueden implementar el marco de responsabilidad electrónica para hacer más ecológicas sus cadenas de suministro. A medida que la práctica se extienda, se sistematizará progresivamente y, eventualmente, convertirá las emisiones en un factor en las decisiones de compra e inversión de cada empresa, como el precio o la calidad.
La infraestructura necesaria ya se está creando a medida que las principales firmas desarrollan soluciones de software y cadena de bloques que permiten y automatizan los datos de emisiones a nivel de producto, calculados según el método de responsabilidad electrónica, para almacenarse y validarse en cada nodo de la cadena de suministro. La empresa química BASF, por ejemplo, tiene desarrolló una herramienta digital de contabilidad de carbono para calcular la huella de carbono de sus 40 000 productos de venta en función de sus propios procesos de producción y de la intensidad de carbono de sus más de 20 000 insumos químicos diferentes. Los proveedores pueden licenciar la herramienta, a través de un tercero independiente, para calcular la huella de carbono del producto en sus propias operaciones. En un año, una parte considerable de los proveedores de BASF se habían suscrito y utilizaban la herramienta para proporcionar a BASF los principales datos de emisiones.