Más allá de la clase mundial: la nueva estrategia de fabricación
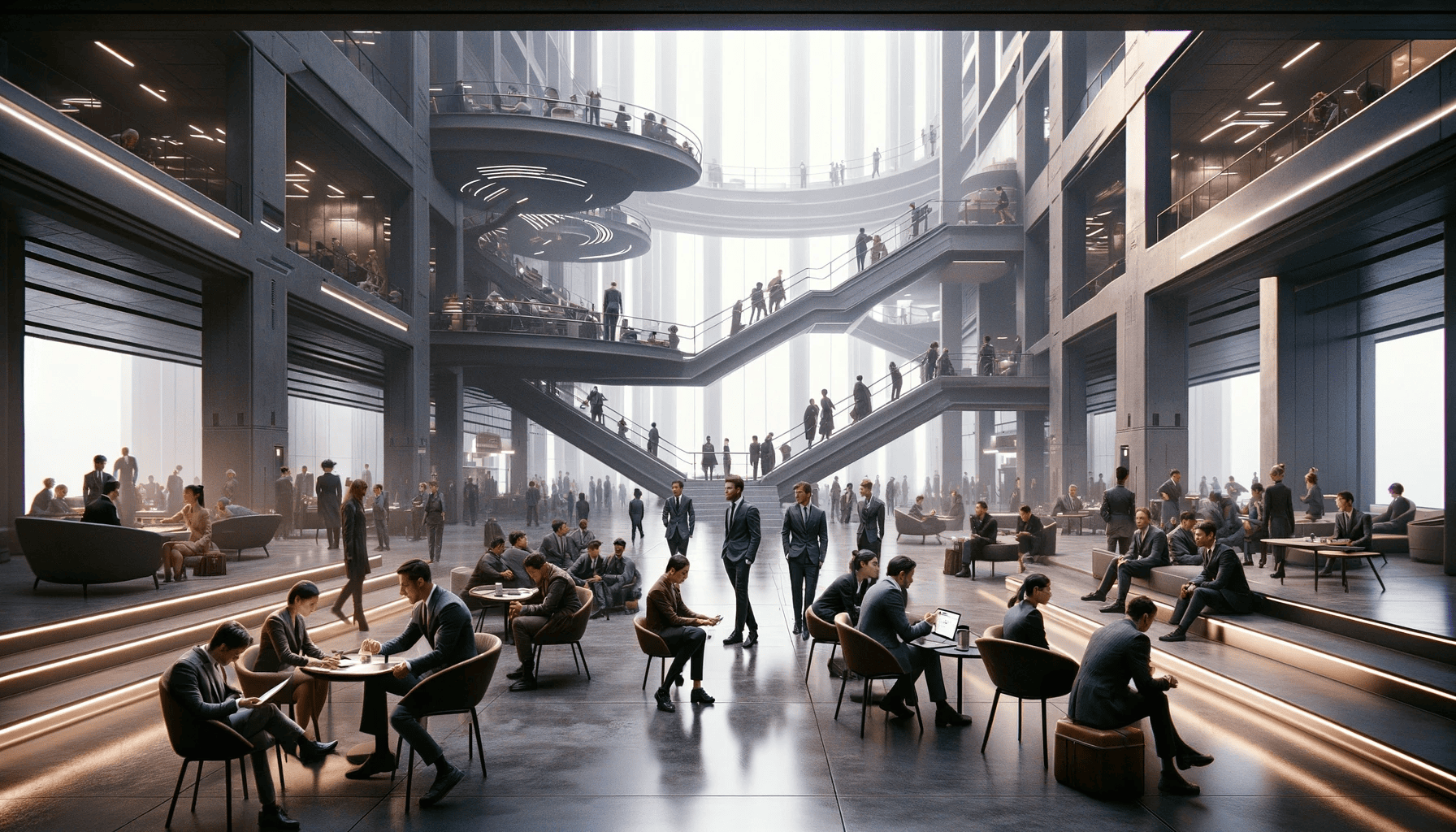
Durante la década de 1980, las empresas manufactureras estadounidenses redescubrieron el poder de una fabricación superior e iniciaron diversas actividades para mejorar su competitividad. Muchos anunciaron que su «estrategia de fabricación» era convertirse en «de clase mundial», tan buenas, según diversas medidas, como las mejores empresas de sus industrias. Para lograr este objetivo, por lo general adoptaron uno o más de un número creciente de programas de mejora, como TQM (gestión de calidad total), producción JIT (justo a tiempo) y DFM (diseño para la fabricación), sin mencionar la fabricación ajustada, la reingeniería, la evaluación comparativa y el enfoque de equipo omnipresente.
Si bien algunos de estos esfuerzos de mejora han tenido éxito, la mayoría, según encuestas recientes, no lo han hecho. Incluso algunas de las empresas japonesas que fueron pioneras en estos enfoques parecen tener dudas. Estos resultados contradictorios han generado frustración, confusión y un debate creciente sobre si las dificultades de estos esfuerzos son el resultado de una mala gestión o de fallas en los propios programas.
Este debate está mal dirigido. El problema no está en los programas ni en la forma en que se implementan. El problema es que simplemente mejorando fabricación (por ejemplo, mediante la adopción de JIT, TQM u otras siglas de tres letras) es no una estrategia para utilizar la fabricación para lograr una ventaja competitiva. Tampoco aspira a una fabricación ajustada, a la mejora continua o a un estatus de clase mundial.
En el turbulento entorno competitivo actual, una empresa necesita más que nunca una estrategia que especifique el tipo de ventaja competitiva que busca en su mercado y articule cómo se va a lograr esa ventaja. Si los directivos depositan sus esperanzas competitivas en la implementación de unos pocos enfoques de mejores prácticas, abandonan implícitamente el concepto central de una estrategia en favor de un enfoque genérico para el éxito competitivo. ¿Cómo puede una empresa esperar alcanzar algún tipo de ventaja competitiva si su único objetivo es ser «tan buena como» sus competidores más duros?
Proponemos una nueva explicación de los problemas que muchas empresas han experimentado con los programas de mejora. Nuestra opinión refleja el cambio actual en la reflexión no solo sobre la fabricación sino también en la esencia de la estrategia competitiva en sí misma. Además, integra la estrategia de fabricación con las nociones de competencias básicas y organizaciones de aprendizaje.
El quid de la cuestión es que la mayoría de las empresas se centran en el formulario de sus activos organizacionales (por ejemplo, la mecánica de JIT y TQM), en lugar de su sustancia, las aptitudes y capacidades que permiten a una fábrica sobresalir y posibilitar que varios programas de mejora logren los resultados deseados. La consecuencia de esta perspectiva es que los gerentes han tendido a ver esos programas como soluciones a problemas específicos y no como escalones en la dirección deseada.
Concienciar la estrategia de fabricación como dirección prevista tiene ramificaciones para casi todos los aspectos de la gestión de una corporación porque implica que la clave del éxito a largo plazo es poder hacer ciertas cosas mejor que tus competidores. Estas capacidades organizativas superiores proporcionan una ventaja competitiva mucho más sostenible que una basada en algo que se puede construir o comprar. Por ejemplo, es posible que pueda comprar acceso a cierta tecnología, pero no puede comprar la capacidad de producirla de manera eficiente, venderla eficazmente ni promocionarla. a lo largo del tiempo. El camino hacia el éxito competitivo no está pavimentado con equipos avanzados, la transferencia de la producción a un área de bajos salarios ni la mejora de la calidad mediante la adopción de un sistema TQM. Todos estos son programas que tus competidores pueden copiar con relativa facilidad.
En un entorno estable, la estrategia competitiva consiste en apostar una posición y la estrategia de fabricación se centra en mejorar las cosas necesarias para defender esa posición. Sin embargo, en entornos turbulentos, el objetivo de la estrategia se convierte en flexibilidad estratégica. Ser de clase mundial no es suficiente; una empresa también tiene que tener la capacidad de cambiar de marcha, por ejemplo, del desarrollo rápido de productos a bajo costo, de forma relativamente rápida y con recursos mínimos. La tarea de la fabricación consiste en proporcionar esa capacidad.
En un entorno turbulento, el objetivo de la estrategia debería ser flexibilidad estratégica.
Si los gerentes consideran las capacidades que desean desarrollar o preservar, pueden tomar decisiones muy diferentes sobre el cierre de una planta o la salida de una empresa, sobre decisiones de «hacer frente a comprar», sobre alianzas y adquisiciones, sobre si automatizar una operación o trasladarla a un área de bajos salarios, sobre capacitación y trayectorias profesionales de gestión. (Consulte el inserto «Un nuevo enfoque de la inversión»). Tener en cuenta las capacidades futuras deseadas también puede ayudar a los gerentes a pensar si JIT o cualquiera de las otras «mejores prácticas» nuevas es el mejor vehículo para desarrollar las capacidades que serán fundamentales para el éxito a largo plazo de su empresa.
Un nuevo enfoque de la inversión
Tradicionalmente, las empresas han considerado las inversiones en nuevas instalaciones, tecnología e I+D como el principal medio para mejorar sus capacidades de fabricación existentes. Sin embargo, de acuerdo con el nuevo enfoque de la estrategia de fabricación, los gerentes deberían pensar más en las inversiones en términos de su capacidad para crear nuevas capacidades. Rara vez, si es que alguna vez, es una capacidad que valga la pena estratégicamente creada a través de una inversión única. Las capacidades que proporcionan fuentes duraderas de ventaja competitiva suelen desarrollarse a lo largo del tiempo mediante una serie de inversiones en instalaciones, capital humano y conocimiento.
La idea de las inversiones como pasos cruciales en el proceso de creación de capacidades entra en conflicto con una suposición que a menudo subyace a las decisiones de presupuestación de capital: que las inversiones pueden revertirse o retrasarse. Según la presupuestación de capital tradicional, un activo que se vende a menudo se puede recomprar y una inversión a menudo se puede aplazar sin más penalización que la contenida en el valor temporal del dinero. Esto puede ser cierto para ciertos tipos de activos, como una nueva planta. Sin embargo, las capacidades de una empresa van más allá de sus activos físicos. De hecho, están plasmadas en gran medida en las habilidades y conocimientos colectivos de su gente y en los procedimientos organizativos que dan forma a la forma en que los empleados interactúan. Al igual que los músculos, las capacidades incorporadas en el capital humano se atrofian con el desuso y el deterioro pueden ser irreversibles.
Considere una empresa que está contemplando cerrar una planta. Las normas contables exigen que se reconozca la pérdida en el valor contable resultante de dicho cierre. Pero, ¿qué pasa con la pérdida de las capacidades especializadas integradas en la planta, como habilidades en mecanizado de precisión, personal altamente motivado y conocimiento detallado de las necesidades de los clientes? Si la demanda aumenta de nuevo, la empresa puede salir y comprar una planta y un equipo, pero reemplazar el capital humano que tardó años en construirse será mucho más difícil.
Los modelos financieros tradicionales utilizados para evaluar las inversiones de capital también ignoran el hecho de que las inversiones pueden crear oportunidades de aprendizaje. Estas oportunidades se parecen mucho a las opciones financieras: tienen valor y ese valor aumenta a medida que el futuro se vuelve más impredecible. Si una empresa no puede predecir si los futuros clientes harán hincapié en el alto rendimiento o en el bajo costo, una opción que le permitiría lograr cualquiera de los dos a medida que evoluciona la situación tiene un valor muy alto.
Considere una empresa que necesita ampliar su capacidad. Una forma podría ser añadir una línea de producción que sea idéntica a las líneas existentes. Un segundo podría ser invertir en un esfuerzo de I+D dirigido a mejorar la productividad. Ciertamente, este último es más arriesgado, pero también brinda la oportunidad de comprender mejor el proceso de producción. Este nuevo conocimiento, a su vez, podría crear oportunidades para inversiones futuras, como un nuevo diseño de equipos de producción o el desarrollo de materiales sustitutivos. También podría abrir nuevas opciones competitivas. Descubrir una forma de reducir los tiempos de configuración, por ejemplo, puede aumentar la capacidad sin inversión adicional. Alternativamente, podría permitir a la empresa producir lotes más pequeños sin pérdida de capacidad. Ninguna de estas opciones sería si la empresa se expandiera añadiendo otra línea como las existentes.
• • •
Se necesita algo de historia para explicar las fuerzas detrás de este nuevo marco estratégico para Smanufacturing.
Hasta principios de la década de 1980, la mayoría de los directivos de los Estados Unidos pensaban en la fabricación en términos de un paradigma cuyas raíces se remontan a más de 100 años. El sistema estadounidense de fabricación, con su énfasis en los mercados masivos, los diseños estándar y la producción de gran volumen con piezas intercambiables, revolucionó la fabricación a mediados del siglo XIX. Modificado y elaborado por los principios de gestión científica promulgados por Frederick Taylor y sus discípulos, así como por grandes industriales como Isaac Singer, Andrew Carnegie y Henry Ford, este nuevo paradigma ayudó a Estados Unidos a convertirse en una potencia industrial en la década de 1920.
Se aceptaron como dogma las siguientes ideas: que el trabajo se realizaba de la manera más eficiente cuando se dividía y se asignaba a especialistas; que los gerentes y los expertos del personal debían pensar para que los trabajadores pudieran concentrarse en «hacer»; que cada proceso se caracterizaba por una cierta cantidad de variación, por lo tanto, tasa irreductible de defectos; y que la comunicación en una organización debe controlarse estrictamente y proceder a través de una cadena de mando jerárquica. La fabricación debe hacer hincapié en las tiradas largas, utilizar equipos diseñados para cada etapa del proceso cuyas capacidades se ajusten lo más posible y utilizar inventarios para amortiguar las diferentes etapas entre sí y del comportamiento errático de proveedores y clientes. El trabajo debe organizarse y llevarse a cabo de forma sistemática, en una secuencia lógica y bajo estricta supervisión.
En 1969, Wickham Skinner desafió la afirmación de Taylor de que había una mejor manera de fabricar en su ahora clásico artículo de HBR, «Manufacturing—Missing Link in Corporate Strategy» (mayo-junio). El núcleo de su argumento fue que: (a) las empresas tienen diferentes puntos fuertes y débiles y pueden elegir diferenciarse de sus competidores de diferentes maneras; b) de manera similar, los diferentes sistemas de producción, la combinación de decisiones en una serie de áreas clave de decisión, tienen un funcionamiento diferente características; y por lo tanto, en lugar de adoptar un sistema de producción estándar de la industria, (c) la «tarea» de la organización de fabricación de una empresa es configurar un sistema de producción que, a través de una serie de opciones interrelacionadas y coherentes internamente, refleje las prioridades y compensaciones implícitas en su situación competitiva y su estrategia.
A pesar del surgimiento de un orden mundial totalmente diferente para la competencia industrial, este marco básico ha demostrado ser notablemente sólido. Una serie de prácticas comunes que se utilizan hoy en día tienen sus raíces en él. Por ejemplo, el concepto de «fábrica enfocada» se desprende naturalmente de la idea de que ninguna organización puede hacer todas las cosas igual de bien. Pensemos en una empresa que comercializa una línea de productos vendidos en un mercado en el que las decisiones de compra dependen en gran medida del precio y otra a personas que están dispuestas a pagar una prima por características personalizadas y de alta calidad. Dado que no cabe esperar que ninguna planta proporcione todas estas características igualmente bien, el concepto de fábrica enfocado aboga por dividir la producción de las dos líneas en fábricas o subunidades separadas dentro de la misma planta.
Otra rama es la idea de hacer coincidir la evolución del producto y del mercado con las características del proceso de fabricación. El ciclo de vida del proceso del producto sugiere que, a medida que un producto madura, la importancia relativa de las prioridades competitivas cambiará, y estos cambios tienen implicaciones importantes para la fabricación. Por ejemplo, en sus primeras etapas, un producto a menudo compite sobre la base de características especiales o diseños innovadores. Esto exige un proceso de producción muy flexible con respecto a los cambios del mercado y de diseño. Tal operación podría emplear trabajadores altamente cualificados, herramientas de uso general y poca automatización; además, debería ubicarse cerca de la I+D y, para reducir el riesgo de obsolescencia, producir lotes pequeños. A medida que el producto madura, el mercado suele evolucionar hacia un pequeño número de productos de gran volumen que compiten entre sí en gran medida en función del precio. Con este fin, las fábricas deben estar altamente automatizadas, ubicadas en áreas donde los costos de mano de obra o materiales sean bajos, emplear trabajadores menos calificados y, para minimizar los costos de cambio, programar la producción a largo plazo.
El marco de Skinner para la estrategia de fabricación se basa en la noción de ajuste estratégico: el sistema de fabricación de una empresa debe reflejar su posición competitiva y su estrategia. Focus proporciona tanto un medio para lograr este ajuste como una disciplina para mantenerlo frente a un aluvión de oportunidades. Además, el ciclo de vida del proceso del producto ayuda a guiar los ajustes en la estrategia y los sistemas que probablemente serán necesarios en un mundo cambiante.
Sin embargo, pronto quedó claro que este marco está incompleto. No explica, por ejemplo, por qué dos fabricantes de electrodomésticos pueden adoptar estrategias competitivas similares y elegir procesos de producción similares, pero uno puede terminar teniendo mucho más éxito que el otro.
Dos empresas pueden adoptar estrategias y procesos de producción similares, pero una puede terminar teniendo mucho más éxito.
• • •
Las empresas japonesas comenzaron a atacar con creciente ferocidad los mercados mundiales de varias industrias a finales de la década de 1970. Su arma secreta resultó ser puro virtuosismo manufacturero. La mayoría producía productos similares a los ofrecidos por las empresas occidentales y los comercializaba de manera similar. Lo que hace que estos productos sean atractivos no solo fue su costo sino también su baja incidencia de defectos, su fiabilidad y su durabilidad.
Durante un tiempo, parecía que la superioridad manufacturera de Japón podía atribuirse a los preceptos tradicionales de la estrategia de fabricación. En general, los japoneses adoptaron políticas coherentes en su búsqueda de una alta eficiencia y calidad. También operaban fábricas específicas; de hecho, su énfasis en la «fabricación repetitiva», la producción «justo a tiempo» y los flujos de trabajo fluidos los llevaron a ser casi obsesivos en su búsqueda de tiradas largas de productos estándar. Y su énfasis en la mejora continua pareció, al menos inicialmente a quienes buscaban puntos de referencia familiares, para reflejar la fascinación estadounidense por las curvas de aprendizaje.
Pero a medida que nuestros ojos se acostumbraban lentamente a los muchos matices de la cultura japonesa y comenzaban a descubrir los detalles de sus prácticas de gestión, se hicieron evidentes ciertas paradojas. Durante la década de 1980, comenzó a surgir un nuevo paradigma de fabricación que desafiaba tanto el sistema estadounidense de fabricación como algunos de los principios básicos de la estrategia de fabricación.
¿Son realmente necesarias las compensaciones? Los estrategas de fabricación habían argumentado durante mucho tiempo que los diferentes sistemas de producción exhibían características operativas diferentes: algunos eran buenos a bajo costo, otros de alta calidad y otros con tiempos de respuesta rápidos. En el diseño de un sistema de producción, por lo tanto, los gerentes tenían que decidir cuál era el más importante. Y si había conflictos entre los distintos objetivos, tenían que tomar decisiones difíciles basándose en un análisis cuidadoso de las compensaciones. Sin embargo, muchas fábricas japonesas que practicaban la fabricación ajustada parecían superar a sus contrapartes estadounidenses en varias dimensiones; lograron un menor costo, una mayor calidad, una introducción de productos más rápida y una mayor flexibilidad, todo al mismo tiempo.
En La máquina que cambió el mundo, el libro ampliamente leído sobre la industria automotriz, los autores James Womack, Daniel Jones y Daniel Roos describen cómo, a diferencia de la producción en masa, la producción ajustada «es «esbelta» porque consume menos de todo... la mitad del esfuerzo humano en la fábrica, la mitad del espacio de la fábrica, la mitad de la inversión en herramientas, la mitad del horas de ingeniería para desarrollar un nuevo producto en la mitad del tiempo. Además, requiere mantener menos de la mitad del inventario necesario in situ, lo que resulta en menos defectos y produce una variedad de productos cada vez mayor y en constante crecimiento».1
Al parecer, la fabricación ajustada ha eliminado las compensaciones entre productividad, inversión y variedad. (Consulte el inserto «Allegheny Ludlum: minimización de las compensaciones de fabricación»).
Allegheny Ludlum: Minimizar las compensaciones de fabricación
Allegheny Ludlum Corporation es una empresa estadounidense que ha estado aplicando una estrategia para minimizar las compensaciones inherentes a la fabricación mediante la ampliación de sus capacidades a través de una variedad de programas personalizados. La siderúrgica especializada, que en los últimos 13 años ha tenido un alto rendimiento sobre el capital social (período durante el cual muchas siderúrgicas perdieron dinero), ha logrado alcanzar un grado sustancial de flexibilidad (en términos de personalización de pedidos individuales) y bajos costes.
El éxito de Allegheny no puede explicarse por su adhesión al concepto tradicional de estrategia de fabricación o por la fabricación ajustada, sino por la forma en que ha integrado con éxito ambos. Al igual que otras empresas que han adoptado la fabricación ajustada, Allegheny hace hincapié en la variedad de productos, los esfuerzos continuos para reducir los costos de fabricación, el trabajo en equipo y la toma de decisiones delegada.
Sin embargo, algunos de los enfoques de Allegheny contradicen las prácticas convencionales de fabricación escasa. Aunque la empresa emplea a los equipos multifuncionales favorecidos en la fabricación ajustada, mantiene una estructura principalmente funcional. Y si bien la fabricación ajustada hace hincapié en la resolución de problemas «horizontal» (lidiar con problemas en niveles inferiores de la organización), la alta dirección de Allegheny está muy involucrada con todos los aspectos del negocio. Los informes diarios sobre productividad, utilización, rendimiento, rechazos y variaciones se dirigen verticalmente a su CEO, que utiliza la información para instituir acciones correctivas inmediatas.
La acerera se ha comprometido a invertir, mejorar y capturar (a través de modelos) sus conocimientos sobre tecnología de procesos. Para alentar a las plantas a llevar a cabo experimentos técnicamente arriesgados, la empresa cobra su coste a una cuenta corporativa separada en lugar de a las propias plantas.
Uno de esos esfuerzos desarrolló capacidades que permitieron a Allegheny duplicar la capacidad de su taller de fundición sin ninguna expansión física. Esto implicó varios proyectos. Una se centró en encontrar materias primas de menor costo, mientras que otras se centraron en aumentar el tamaño de los lotes, reducir el tiempo necesario entre lotes y reducir el tiempo entre la finalización de la fusión y el procesamiento posterior. Estos proyectos incluían experimentación en el taller, con la participación activa de supervisores de primera línea y contribuciones de otros departamentos. Por ejemplo, I+D desarrolló programas informáticos para aumentar el control sobre el proceso de fusión. Este aumento de la capacidad le dio a Allegheny la opción de ampliar su producción total de aceros básicos (a un costo inferior al de la competencia), realizar pedidos más personalizados o alguna combinación de ambos. Cuando hay incertidumbre sobre la demanda de cada tipo de producto, tener esta opción es obviamente valioso.
Al igual que las empresas dedicadas a la fabricación ajustada, Allegheny se dedica a la mejora vigorosa y continua de la fabricación. A diferencia de las mejoras de muchas de estas empresas, estas mejoras se llevan a cabo dentro de un marco estratégico que reconoce que la clave para lograr una ventaja competitiva es decidir qué capacidades construir.
¿Las fábricas tienen que estar centradas? Aunque en un principio las fábricas japonesas parecían restringir la variedad de productos y fomentar flujos de trabajo ininterrumpidos, muchas empresas japonesas de élite se embarcaron en una orgía de proliferación de productos durante la década de 1980. Sony, por ejemplo, introdujo más de 300 versiones de su Walkman básico (renunciando a la necesidad de realizar estudios de mercado, simplemente introdujo un nuevo modelo y vio cómo se vendía), y Seiko era conocida por su capacidad de introducir un nuevo modelo de reloj cada día laborable. ¿No refutó esta proliferación de productos la idea del enfoque? La aparición de nuevos sistemas de fabricación flexible, que aparentemente permitían a las fábricas producir una amplia gama de productos con poca pérdida de eficiencia, también parecía socavar la necesidad de fábricas centradas.
¿Es suficiente el ajuste estratégico? Aunque el marco de estrategia de fabricación tradicional proporcionaba una visión de la contribución que la organización de fabricación de una empresa podía hacer a su éxito competitivo, dejaba vagas algunas cuestiones clave. Por ejemplo, si bien estaba claro que una vez que una empresa se decidía por una estrategia competitiva, su organización manufacturera debía desarrollar las capacidades específicas necesarias para implementar esa estrategia, no estaba tan claro cuánta libertad debería tener la fabricación para desarrollar competencias que fueran más allá de la estrategia requisitos inmediatos. Y hubo poca discusión sobre los criterios que deberían utilizarse para guiar la selección de las capacidades que se adquirirían.
Además, si bien muchas empresas japonesas habían creado capacidades de fabricación excepcionales, no parecían tener un enfoque duradero de la competencia. En cambio, la forma de su ataque cambió, a veces con una velocidad desconcertante, de bajo costo a alta precisión, flexibilidad e innovación. Y a través de estos cambios, a veces podían transformar la naturaleza de la competencia dentro de una industria.• • •
Al parecer, las empresas japonesas habían encontrado un enfoque de fabricación uniformemente superior al «sistema Taylor», que se caracterizaba por un énfasis en la velocidad y la flexibilidad más que en el volumen y el costo. De acuerdo con este enfoque ajustado, las personas deben estar ampliamente capacitadas en lugar de especializarse. El personal está «sobrecargado» y los gastos generales son malos. Los rechazos son inaceptables. La comunicación debe tener lugar de manera informal y horizontal entre los trabajadores de línea en lugar de a través de rutas jerárquicas prescritas. Los equipos deben ser de uso general, posiblemente utilizar algún tipo de automatización programable, y estar organizados en celdas que produzcan un grupo de productos similares en lugar de estar especializados por etapa del proceso. El tiempo de producción es más importante que la mano de obra o la utilización del equipo. El inventario, al igual que los rechazos, es «desperdicio». Las relaciones con los proveedores deben ser a largo plazo y cooperativas. Las actividades asociadas con el desarrollo de productos deben realizarse de forma simultánea, no secuencial, y deben ser llevadas a cabo por equipos multifuncionales.
El enfoque japonés nos ha dado un giro completo desde los días de Frederick Taylor: la velocidad y la flexibilidad han reemplazado el coste y la jerarquía, pero una vez más, nos hemos decidido por «una mejor manera» de competir. La pregunta, entonces, es ¿qué papel le queda a la estrategia de fabricación? ¿De qué sirve preocuparse si debe hacer hincapié en el costo o en la flexibilidad cuando sus competidores han adoptado enfoques de fabricación que les permitan ganarle en ambos aspectos?
¿Qué papel le queda a la estrategia de fabricación cuando nos hemos decidido por «una mejor forma» de competir?
En el entorno relativamente estable de los años 60 y principios de los 70, el nombre del juego en estrategia era encontrar una posición atractiva en la industria (ofrecer el menor costo o la más alta calidad) y construir una fortaleza competitiva a su alrededor. Una buena estrategia de fabricación era aquella que defendía la posición de una empresa a través de un conjunto de capacidades estrechamente enfocadas.
Sin embargo, cuando los términos de la competencia cambiaron de bajo costo a alta calidad a flexibilidad e innovación, las empresas descubrieron que tanto su estrategia competitiva como su estrategia de fabricación quedaron obsoletas rápidamente. Centralizar la producción en una instalación altamente automatizada puede parecer una decisión brillante cuando los clientes dan prioridad a un precio bajo. Pero a medida que el mercado cambia y los competidores se adaptan para proporcionar mayor calidad y tiempos de respuesta más rápidos, manteniendo al mismo tiempo sus costos razonablemente baja, una instalación centralizada puede convertirse rápidamente en una piedra de molino corporativa.
Por otro lado, las empresas que eligen la innovación de productos en lugar del bajo coste como forma de competir podrían tener el problema contrario. Por ejemplo, Compaq prosperó en la década de 1980 al ser uno de los desarrolladores más rápidos de nuevos productos en la industria de los ordenadores personales. Pero se encontró con problemas en la década de 1990, cuando los clientes daban mayor importancia al bajo costo y a la respuesta rápida en la personalización de los productos, mejorando gradualmente las características y la entrega. Tras una gran agitación organizativa, Compaq pudo reajustar sus operaciones para reducir sus costos y, más recientemente, ha comenzado a realizar nuevos cambios con la esperanza de proporcionar una capacidad de respuesta al cliente que coincida con la de sus rivales Dell Computer.
Lamentablemente, ni el enfoque tradicional de la estrategia de fabricación ni el paradigma de fabricación lean-manufacturing prestan mucha atención a reforzar la flexibilidad estratégica de una organización. De hecho, ambos enfoques suelen obstaculizar la flexibilidad. El enfoque inicial de la estrategia de fabricación llevó a los altos directivos a centrar las operaciones de sus empresas en torno a prioridades competitivas específicas que tendían a hacerlas vulnerables a los cambios estratégicos. Y la fabricación ajustada impulsa a las empresas a ser similares entre sí.
El problema no está en la fabricación ajustada en sí ni en ninguna de sus prácticas de componentes como ingeniería simultánea, JIT o TQM. El problema es la forma en que las empresas aplican estas prácticas a sus propios problemas. Las empresas suelen embarcarse en este tipo de programas para corregir debilidades particulares de sus operaciones. Sin embargo, los directivos suelen definir sus problemas en términos de puntos de partida y puntos finales: «Necesitamos reducir nuestro coste variable$ 1 por unidad» o «Necesitamos reducir nuestro nivel de defectos a 200 partes por millón». Y buscan soluciones mediante la adopción de prácticas específicas: «Vamos a implementar un sistema JIT para ser más receptivos» o «Necesitamos un programa de gestión de calidad para mejorar nuestra calidad».
Es difícil imaginar que un proceso de mejora de la fabricación progrese muy lejos sin especificar ciertos cambios en las prácticas y objetivos mensurables. Pero pensar en términos de periodos de tiempo y enmarcar las soluciones como la adopción de prácticas específicas puede dar lugar a dos tipos de problemas. La primera es equiparar una mejora de las capacidades de fabricación con una estrategia de fabricación. La segunda es no reconocer que las nuevas prácticas crean nuevas capacidades que pueden formar la base de una nueva estrategia de fabricación: si son reconocidos y explotados.• • •
Tras emprender un importante esfuerzo de mejora de la fabricación, las empresas pueden descubrir que justo cuando parecen haber resuelto el problema (por ejemplo, reducir la brecha de calidad entre ellas y sus competidores), encuentran nuevos problemas que requieren nuevos enfoques, algunos de los cuales parecen contradecir los solo póngalo en su lugar. Una vez que la calidad ha mejorado, por ejemplo, es posible que las empresas necesiten reducir los tiempos de desarrollo de los productos o reducir los costes de entrega.
Las empresas suelen resolver un problema solo para enfrentar otros nuevos, cuyas soluciones contradicen los programas que se acaban de poner en marcha.
Algunos argumentarían que tales cambios en las prioridades reflejan simplemente la necesidad de una mejora continua. Después de todo, nunca se puede esperar dejar de hacer mejoras. Desafortunadamente para los involucrados (los gerentes, los supervisores de primera línea y los empleados del taller), estos esfuerzos se parecen más a una frustración continua. A pesar de la implementación aparentemente exitosa de un nuevo conjunto de prácticas tras otro, la empresa siempre parece estar tratando de ponerse al día con sus competidores.
Whistler, una empresa estadounidense de electrónica de consumo, se enfrentó a una opción a finales de la década de 1980 cuando estaba perdiendo rápidamente cuota de mercado frente a sus competidores asiáticos: mejorar las operaciones nacionales para lograr la paridad de costos o trasladarse al extranjero, como lo habían hecho sus competidores estadounidenses. Whistler eligió el primero y logró reducir sus costes de fabricación a niveles asiáticos durante dos años. Desafortunadamente, para cuando la empresa lo logró, los competidores asiáticos estaban tomando cuota de mercado al introducir un aluvión de nuevos productos.
El problema de Whistler no era que su programa de mejora fuera defectuoso o estuviera mal implementado; había logrado reducir drásticamente los costos. Pero al hacerlo, había distraído la atención de la dirección del desarrollo de nuevos productos, mientras que los competidores asiáticos habían podido ser más innovadores. y mantener costos relativamente bajos.
Sin darse cuenta, los esfuerzos de mejora de la fabricación de Whistler habían dado lugar a un cambio en su estrategia de fabricación de ser la primera en introducir productos innovadores a lograr la paridad de costos. Si la empresa hubiera visto su problema desde este punto de vista, podría haber elegido un camino diferente. En lugar de simplemente intentar cambiar sus operaciones para que sean más competitivas en cuanto a costos, pero menos innovadoras, podría haber buscado formas de cambiar la compensación entre coste e innovación.• • •
Al ver los diferentes programas de mejora dirigidos a soluciones específicas de la competencia como problemas, los gerentes pasan por alto el verdadero poder de estos programas: su capacidad para desarrollar nuevas capacidades. Por lo tanto, un papel clave de la estrategia de fabricación de una empresa es guiar la selección de programas de mejora.
Considere una planta que establezca el objetivo a largo plazo de reducir drásticamente sus plazos de entrega e inventarios. Puede avanzar hacia este objetivo en cualquiera de las dos direcciones. Una podría ser la adopción inmediata de un sistema de extracción JIT. Si la planta carece de las habilidades que hacen que JIT funcione (por ejemplo, tiempos de preparación bajos y tasas de defectos), este enfoque puede resultar muy costoso. Sin embargo, la adopción de este sistema creará fuertes incentivos para reducir los tiempos de preparación y las tasas de defectos, así como para desarrollar otras habilidades relacionadas con las TIC e inducir una ética de mejora continua. Con el tiempo, podría surgir un verdadero sistema JIT.
Un enfoque alternativo sería comenzar con un sistema de planificación de los recursos de fabricación (MRP), un sistema informatizado de programación de la producción basado en previsiones de demanda futura y plazos de producción, así como en datos en tiempo real del taller. Es posible que los resultados iniciales no sean parecidos a los de JIT. De hecho, los plazos de entrega pueden incluso aumentar temporalmente, ya que los sistemas MRP tienden a ser bastante torpes a la hora de gestionar los cambios de horario y los pedidos urgentes. Por otro lado, MRP ejerce presión para mejorar la disciplina del taller y desarrollar mejores datos, lo que facilita una mejor programación de la producción y la transición a la fabricación integrada por ordenador. Una vez establecido el control MRP, los plazos de entrega del sistema pueden ser reducidos constantemente hasta que se acerque a un sistema JIT puro.
Ambos enfoques pueden permitir a la empresa responder rápidamente a las demandas de los clientes con bajos inventarios. Sin embargo, cultivan capacidades diferentes a lo largo del tiempo. La adopción de un sistema tipo MRP fomenta las habilidades en el uso de computadoras y la gestión de bases de datos, ninguna de las cuales es fundamental para un enfoque JIT. Los sistemas de extracción, por otro lado, fomentan las habilidades en la resolución de problemas en la planta de fábrica, la mejora incremental de los procesos y la respuesta rápida. Cada enfoque, en resumen, deja a la organización con un conjunto diferente de habilidades y, por lo tanto, un conjunto diferente de opciones estratégicas en el futuro. No se debe tomar una decisión sobre qué enfoque seguir sin considerar qué conjunto de capacidades será más valioso para la empresa.• • •
Pensar en TQM, JIT y otros programas de mejora de la fabricación no como termina en sí mismos, pero en términos de las capacidades que ambos requieren y crean impulsos a pensar de manera diferente sobre las soluciones. Dentro de un marco estático, las soluciones a los problemas se consideran acuerdos únicos. Sin embargo, en un entorno dinámico, las soluciones se consideran parte de un plazo más largo ruta de mejora. Las prácticas individuales se adoptan no solo para resolver un problema inmediato, sino también para desarrollar nuevas habilidades que abran nuevas oportunidades. Desde esta perspectiva, la estrategia de fabricación no consiste solo en alinear las operaciones con las prioridades competitivas actuales, sino también en seleccionar y crear las capacidades operativas que necesitará una empresa en el futuro. (Consulte el inserto «Hitachi-Seiki: Creación de capacidades»).
La estrategia de fabricación consiste en crear las capacidades operativas que una empresa necesita para el futuro.
Hitachi-Seiki: Creación de capacidades
Muchas empresas japonesas se han dado cuenta de que, al ampliar el rango de sus capacidades de fabricación, aumentan sus opciones estratégicas. Aun así, pocos han creado estrategias que detallan exactamente qué capacidades deben desarrollar para mejorar su flexibilidad estratégica. Hitachi-Seiki parece ser una de las excepciones. A mediados de la década de 1980, la empresa, un fabricante relativamente oscuro de máquinas herramienta, se había convertido en uno de los principales proveedores mundiales de sistemas de fabricación flexibles, equipos controlados por ordenador que pueden realizar una secuencia variable de tareas de mecanizado.
Ya en 1952, cuando se desarrolló la primera máquina herramienta con control numérico en el MIT, Hitachi-Seiki se fijó el ambicioso objetivo de desarrollar las capacidades necesarias para convertirse en líder en automatización computarizada. Comenzó con la investigación básica en producción automatizada, algunas de las cuales se realizaron en colaboración con otros fabricantes japoneses a través de un consorcio organizado por el Ministerio de Comercio Internacional e Industria. Después de la disolución del consorcio y a pesar de que los numerosos problemas con la nueva tecnología llevaron a la mayoría de las empresas a seguir con los procesos de fabricación tradicionales, Hitachi-Seiki siguió construyendo su base de conocimientos.
Al reconocer desde el principio que una automatización exitosa requeriría la integración del diseño mecánico (la tecnología tradicional de máquinas herramienta) y la electrónica, la empresa comenzó a contratar ingenieros eléctricos. Y en 1967, creó una nueva disciplina de ingeniería, a la que llamó «mecatrónica».
Los primeros esfuerzos de la empresa en sistemas de fabricación flexible fracasaron. Su primer sistema, desarrollado en 1972, tenía una productividad ligeramente mejor que la maquinaria convencional y estaba plagado de problemas de fiabilidad y coordinación. Sin embargo, el desarrollo de ese sistema creó capacidades para proyectos futuros. Por ejemplo, reunió por primera vez a algunos de los mejores ingenieros de diferentes disciplinas de la empresa para escribir software. Encontraron dificultades para coordinar sus esfuerzos. Pero gracias a esta experiencia inicial, Hitachi-Seiki pudo cultivar ingenieros con amplias habilidades y perspectivas.
El primer sistema de fabricación flexible de Hitachi-Seiki estuvo plagado de problemas, pero el desarrollo del sistema proporcionó una rica experiencia de aprendizaje que creó capacidades para proyectos futuros.
El segundo proyecto de la compañía incorporó algunas de las lecciones aprendidas del primero. Si bien los resultados fueron ligeramente mejores, tampoco alcanzó sus objetivos y su productividad no era lo suficientemente alta como para generar un retorno de la inversión adecuado. Pero la empresa volvió a aprender lecciones críticas. Una era que considerar la fabricación flexible como un conjunto de problemas puramente técnicos que podían resolverse con conocimientos técnicos era un error. En cambio, la empresa necesitaba adoptar un enfoque sistémico para el desarrollo que combinara las perspectivas de fabricación e ingeniería.
Para su tercer proyecto, Hitachi-Seiki creó un equipo de desarrollo que agrupa diversas funciones, como fabricación, diseño de máquinas, ingeniería de software y diseño de herramienta. El líder del proyecto se formó como ingeniero mecánico pero tenía experiencia en diseño y fabricación de herramienta.
El equipo había aprendido de los proyectos anteriores que sería difícil desarrollar un sistema que pudiera alcanzar todos los objetivos de rendimiento deseados. Estos incluían el cambio automático de herramienta, accesorios flexibles que podían contener materiales de diferentes tamaños y la capacidad de operar sin atender. Así que los miembros del equipo decidieron desarrollar tres sistemas y crearon equipos separados para abordar cada uno. Los tres sistemas se terminaron en un tiempo récord y cumplieron sus objetivos financieros y de rendimiento.
La lección de la historia de Hitachi-Seiki no es simplemente «Si al principio no tienes éxito, inténtalo de nuevo». La empresa tenía un objetivo a largo plazo pero carecía de las capacidades para lograrlo. Los primeros proyectos eran vehículos para desarrollar estas capacidades. Con cada proyecto, la empresa amplió sus conocimientos sobre cuestiones técnicas (es decir, software informático) y cuestiones organizativas (es decir, cómo integrar disciplinas para resolver problemas). Y con cada proyecto sucesivo, los ingenieros que comenzaron como especialistas se convirtieron gradualmente en generalistas.
Tras desarrollar el primer sistema de fabricación flexible de éxito comercial de la empresa, muchos de los miembros del equipo del proyecto se trasladaron al Departamento de Servicio al Cliente, donde diseñaron y construyeron sistemas para los clientes. Esto aprovechó las habilidades que habían desarrollado y amplió su comprensión de las necesidades de los clientes. También garantizó que un nuevo grupo de ingenieros comenzara a aprender a desarrollar sistemas de fabricación flexibles.
Este cambio de perspectiva tiene enormes implicaciones para las decisiones corporativas básicas. Veamos dos ejemplos.
Fábricas enfocadas. Los defensores del enfoque tradicional de la estrategia de fabricación y la fabricación ajustada consideran la idea de enfocarse de manera diferente. La idea de que las fábricas deben centrarse en un conjunto limitado de tareas u objetivos sigue ganando aceptación en los Estados Unidos, aunque no siempre está claro si una instalación determinada debe centrarse en productos, procesos o regiones. Los defensores de la fabricación ajustada, en cambio, consideran que el enfoque es un concepto anticuado, que refleja la larga fijación de Estados Unidos con la producción en masa.
A pesar de sus aparentes diferencias, ambos no reconocen que la organización de un sistema de fabricación afecta no solo a su rendimiento actual sino también, con el tiempo, a las cosas que puede hacer fácilmente o con dificultad. Si debe centrarse una planta y cómo debe centrarse depende de las capacidades que quiera desarrollar.
Las habilidades de una planta pueden considerarse el conjunto de tareas que considera rutinarias. Que una tarea determinada sea o no rutinaria depende de la experiencia y las capacidades. Por ejemplo, el montaje de alta precisión puede, con el tiempo, convertirse en rutina para una planta, pero aún así puede considerarse muy difícil para una planta con menos experiencia. Esto explica por qué tantas plantas con un rendimiento deficiente se han transformado al adoptar el concepto de enfoque. Su bajo desempeño reflejaba la falta de habilidades operativas y la concentración proporcionaba un mecanismo para canalizar la atención y los recursos de la gerencia hacia el dominio de esas habilidades. A medida que una organización adquiere experiencia operativa, las tareas difíciles se convierten en rutinarias y pueden adquirir complejidad adicional con poca penalización en el rendimiento.
Integración vertical y abastecimiento. La fabricación ajustada favorece la externalización y las relaciones a largo plazo con los proveedores. Por otro lado, las empresas estadounidenses han considerado tradicionalmente las decisiones de abastecimiento en términos de compensaciones financieras y limitaciones de recursos. Una vez más, ambos puntos de vista restan importancia a la dinámica de tales decisiones.
Considere una empresa que está tratando de decidir si va a fabricar un componente o comprarlo a un proveedor externo. Por lo general, estas decisiones se toman analizando los costos de producción y organización relevantes de las dos alternativas. Sin embargo, ese tipo de análisis se vuelve sospechoso si uno piensa no en términos de partes que se incorporan a los productos, sino en términos de capacidades que están estrechamente vinculadas y se refuerzan mutuamente en contraposición a aquellas que pueden separarse. Si un proveedor potencial posee capacidades esenciales para el éxito competitivo de una empresa, la empresa debe trabajar para asimilar esas capacidades o desarrollar relaciones muy estrechas y similares a las de una asociación con ese proveedor.
La decisión de externalizar una actividad puede alterar por completo el cálculo de decisiones futuras. Al igual que las personas, las organizaciones pueden olvidar cómo hacer las cosas. A medida que las habilidades se atrofian por el desuso, volver a llevar las actividades a la empresa en algún momento futuro se vuelve menos factible. Por lo tanto, al igual que la decisión sobre las fábricas centradas, la externalización requiere una evaluación del potencial de aprendizaje. Llevar a cabo una actividad interna con la que la empresa tiene poca experiencia puede ser ineficiente y menos «esbelta» a corto plazo, pero absolutamente esencial a largo plazo porque desarrolla habilidades críticas de las que carece actualmente la empresa.• • •
La estrategia de fabricación ya no puede limitarse a guiar las elecciones a corto plazo entre prioridades conflictivas como el costo, la calidad y la flexibilidad. Los directivos tampoco pueden limitarse a elegir qué técnica de mejora de moda adoptar o qué empresa emular. El éxito a largo plazo requiere que una empresa busque continuamente nuevas formas de diferenciarse de sus competidores. Las empresas que pueden transformar sus organizaciones de fabricación en fuentes de ventaja competitiva son aquellas que pueden aprovechar varios programas de mejora para lograr el objetivo más amplio de seleccionar y desarrollar capacidades operativas únicas. ¿Cómo puede crear una empresa semejante estrategia?
En primer lugar, debe comenzar con la idea de que la principal forma en que la fabricación añade valor a una empresa es permitiéndole hacer ciertas cosas mejor que sus competidores. Qué cosas y cómo son mejores serán diferentes para las empresas individuales y para la misma empresa en puntos individuales de su evolución. En ocasiones, todas las empresas quedan rezagadas con respecto a sus competidores en algún ámbito, pero a largo plazo, deben identificar una o dos áreas (por ejemplo, flexibilidad e innovación) en las que intentará estar a la vanguardia la mayor parte del tiempo.
Obviamente, estas capacidades deberían ser las que los clientes valoran; mejor aún, deberían ser aquellas que a los competidores les resulte difícil duplicar. Los clientes pueden valorar el bajo costo, por ejemplo, pero como aprendieron muchas empresas de electrónica de consumo durante los años setenta y ochenta, lograr un bajo costo al ir al extranjero no proporciona una ventaja sostenible porque los competidores pueden hacer lo mismo. Los competidores también pueden licenciar una nueva tecnología o contratar a quienes participaron en su desarrollo. Las excelentes estrategias de fabricación se basan en habilidades y capacidades únicas, no en inversiones en edificios, equipos o individuos específicos.
En segundo lugar, una empresa debe desarrollar un plan para desarrollar las capacidades que desea adquirir. Aquí es donde entra en juego la cuestión de qué enfoques de mejora de la fabricación utilizar y en qué orden. Una empresa puede decidir utilizar equipos, pero solo después de haber cultivado las capacidades que permitirán que los equipos sean eficaces: credibilidad y confianza entre grupos funcionales y un cuadro de líderes de equipo eficaces.
Antes de adoptar cualquier programa, los gerentes deben preguntarse: «¿Qué capacidades específicas creará este programa para mi organización y son valiosas estas capacidades en términos competitivos?» Proporcionar respuestas claras a estas preguntas suele ser más fácil si los gerentes se centran solo en unas pocas actividades de mejora cuidadosamente seleccionadas. Y los elegidos probablemente tendrán que modificarse para satisfacer las necesidades de la empresa. Ni las capacidades ni los programas de mejora vienen en una talla única.
En el mundo actual, donde nada es predecible y los competidores desconocidos emergen de direcciones inesperadas en el peor momento posible, una empresa debe considerarse a sí misma como un conjunto de capacidades en evolución, no solo como una colección de productos y negocios, que proporcionan la flexibilidad necesaria para embarcarse en nuevas direcciones. La estrategia corporativa debe proporcionar un marco para guiar la selección, el desarrollo y la explotación de estas capacidades. Dado que muchas de las capacidades con mayor valor competitivo residen en la organización de fabricación de una empresa, la estrategia corporativa debe ser mucho más explícita y depender de las consideraciones de fabricación que en el pasado.
Referencias
1. La máquina que cambió el mundo (Nueva York: Macmillan, 1990), pág. 13.
— Escrito por Robert H. Hayes Robert H. Hayes Gary P. Pisano