La teoría emergente de la fabricación
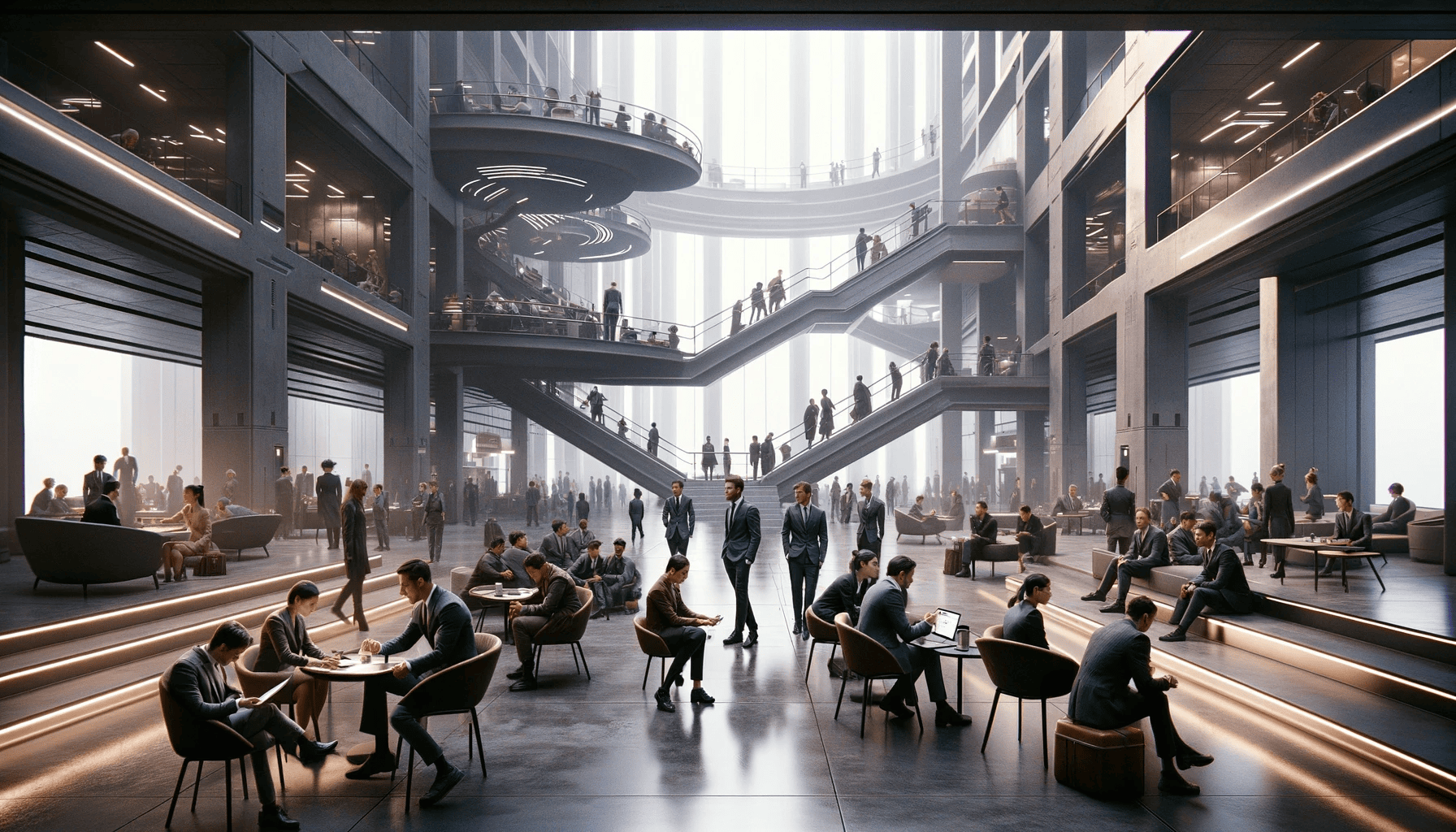
No podemos construirlo todavía. Pero ya podemos especificar la fábrica «posmoderna» de 1999. Su esencia no será mecánica, aunque habrá muchas máquinas. Su esencia será conceptual: el producto de cuatro principios y prácticas que, en conjunto, constituyen un nuevo enfoque de la fabricación.
Cada uno de estos conceptos se está desarrollando por separado, por diferentes personas con diferentes puntos de partida y agendas diferentes. Cada concepto tiene sus propios objetivos y sus propios tipos de impacto. El control estadístico de calidad está cambiando la organización social de la fábrica. La nueva contabilidad de fabricación nos permite tomar decisiones de producción como decisiones empresariales. La organización de la «flotilla», o módulo, del proceso de fabricación promete combinar las ventajas de la estandarización y la flexibilidad. Por último, el enfoque de sistemas incorpora el proceso físico de hacer cosas, es decir, la fabricación, en el proceso económico de los negocios, es decir, en el negocio de crear valor.
A medida que estos cuatro conceptos se desarrollan, están transformando la forma en que pensamos sobre la fabricación y cómo la gestionamos. La mayoría de los fabricantes de los Estados Unidos saben ahora que necesitamos una nueva teoría de fabricación. Sabemos que poner remiendos a viejas teorías no ha funcionado y que un nuevo parche solo nos empujará más atrás. Juntos, estos conceptos nos dan la base de la nueva teoría que tanto necesitamos.
El concepto más publicitado, el Control Estadístico de Calidad (SQC), en realidad no es nuevo en absoluto. Se basa en la teoría estadística formulada hace 70 años por Sir Ronald Fisher. Walter Shewhart, físico de Bell Laboratories, diseñó la versión original de SQC en la década de 1930 para la producción masiva sin defectos de centrales telefónicas y aparatos telefónicos complejos. Durante la Segunda Guerra Mundial, W. Edwards Deming y Joseph Juran, ambos antiguos miembros del círculo de Shewhart, desarrollaron por separado las versiones utilizadas hoy en día.
Los japoneses deben su liderazgo en la calidad de fabricación en gran medida a que adoptaron los preceptos de Deming en los años cincuenta y sesenta. Juran también tuvo un gran impacto en Japón. Pero la industria estadounidense ignoró sus contribuciones durante 40 años y solo ahora se está convirtiendo a SQC, con compañías como Ford, General Motors y Xerox entre los nuevos discípulos. Europa occidental también ha ignorado en gran medida el concepto. Lo que es más importante, incluso los profesionales más exitosos de SQC no entienden a fondo lo que realmente hace. En general, se considera una herramienta de producción. En realidad, su mayor impacto está en la organización social de la fábrica.
A estas alturas, todos los interesados en la fabricación saben que SQC es un método científico riguroso para identificar la calidad y la productividad que se puede esperar de un proceso de producción determinado en su forma actual, de modo que el control de ambos atributos pueda integrarse en el propio proceso. Además, SQC puede detectar al instante fallos de funcionamiento y mostrar dónde se producen: una herramienta desgastada, una pistola pulverizadora sucia, un horno de sobrecalentamiento. Y debido a que puede hacerlo con una muestra pequeña, los fallos de funcionamiento se informan casi de inmediato, lo que permite a los operadores de máquinas corregir los problemas en tiempo real. Además, SQC identifica rápidamente el impacto de cualquier cambio en el rendimiento de todo el proceso. (De hecho, en algunas aplicaciones desarrolladas por los discípulos japoneses de Deming, las computadoras pueden simular de antemano los efectos de un cambio propuesto). Por último, SQC identifica dónde y, a menudo, cómo se puede mejorar continuamente la calidad y la productividad de todo el proceso. Esto solía llamarse «Ciclo Shewhart» y luego «Ciclo Deming»; ahora es kaizen, el término japonés para la mejora continua.
Pero estas características de ingeniería explican solo una fracción de los resultados de SQC. Sobre todo, no explican la brecha de productividad entre las fábricas japonesas y estadounidenses. Incluso después de ajustarse por su dependencia mucho mayor de proveedores externos, Toyota, Honda y Nissan producen dos o tres veces más automóviles por trabajador que las plantas estadounidenses o europeas comparables. La creación de calidad en el proceso no representa más de un tercio de esta diferencia. Las principales ganancias de productividad de Japón son el resultado de los cambios sociales provocados por SQC.
Los japoneses emplean proporcionalmente más operadores de máquinas en el trabajo de producción directa que Ford o GM. De hecho, la introducción de SQC casi siempre aumenta el número de operadores de máquinas. Pero este aumento se compensa muchas veces con la brusca caída del número de personas que no operan: inspectores, sobre todo, pero también personas que no lo hacen hacer pero arreglar, como equipos de reparación y «bomberos» de todo tipo.
En las fábricas estadounidenses, especialmente en las plantas de producción en masa, estos empleados obreros que no operan superan considerablemente en número a los operadores. En algunas plantas, la proporción es de dos a uno. Pocos de estos trabajadores son necesarios bajo SQC. Además, los supervisores de primera línea también se eliminan gradualmente, y solo un puñado de formadores toman su lugar. En otras palabras, SQC no solo hace posible que los operadores de máquinas tengan el control de su trabajo, sino que hace que dicho control sea casi obligatorio. Nadie más tiene el conocimiento práctico necesario para actuar eficazmente sobre la información que SQC le devuelve constantemente.
Al alinear la información con la responsabilidad, SQC resuelve un conflicto hasta ahora irresoluble. Durante más de un siglo, han prevalecido dos enfoques básicos de la fabricación, especialmente en los Estados Unidos. Uno de ellos es el enfoque de ingeniería impulsado por la «gestión científica» de Frederick Winslow Taylor. El otro es el enfoque de «relaciones humanas» (o «recursos humanos») desarrollado antes de la Primera Guerra Mundial por Andrew Carnegie, Julius Rosenwald de Sears Roe buck y Hugo Münsterberg, psicólogo de Harvard. Los dos enfoques siempre han sido considerados antítesis, de hecho, mutuamente excluyentes. En SQC, se unen.
Taylor y sus discípulos estaban tan decididos como Deming a incorporar calidad y productividad en el proceso de fabricación. Taylor afirmó que su «única forma correcta» garantizaba la calidad de cero defectos; se oponía con tanta vehemencia a los inspectores como Deming lo es hoy en día. También lo fue Henry Ford, quien afirmó que su línea de montaje incorporaba calidad y productividad al proceso (aunque de otra manera no le tocó la dirección científica de Taylor y probablemente ni siquiera lo sabía). Sin embargo, sin la rigurosa metodología de SQC, ni la gestión científica ni la línea de montaje podrían ofrecer un control de procesos integrado. Con todos sus éxitos, tanto la dirección científica como la línea de montaje tuvieron que recurrir a una inspección masiva para solucionar los problemas en lugar de eliminarlos.
El enfoque de relaciones humanas considera el conocimiento y el orgullo de los trabajadores de línea como el mayor recurso para controlar y mejorar la calidad y la productividad. También ha tenido importantes éxitos. Pero sin el tipo de información que proporciona SQC, no se puede distinguir fácilmente la actividad productiva de la ajetreada. También es difícil saber si una modificación propuesta mejorará realmente el proceso o simplemente hará que las cosas se vean mejor en un rincón, solo para empeorarlas en general.
Los círculos de calidad, que en realidad se inventaron y utilizaron ampliamente en la industria estadounidense durante la Segunda Guerra Mundial, han tenido éxito en Japón porque llegaron después de que se estableciera SQC. Como resultado, tanto el círculo de calidad como la dirección tienen información objetiva sobre los efectos de las sugerencias de los trabajadores. Por el contrario, la mayoría de los círculos de calidad estadounidenses de los últimos 20 años han fracasado a pesar del gran entusiasmo, especialmente por parte de los trabajadores. ¿El motivo? Se establecieron sin SQC, es decir, sin comentarios rigurosos y fiables.
Muchos fabricantes estadounidenses han incorporado calidad y productividad en sus procesos de fabricación sin SQC y, sin embargo, con un mínimo de inspección y fijación. Johnson & Johnson es un ejemplo de ello. Otras empresas han conseguido que los operadores de maquinas tengan el control del proceso de fabricación sin instituir SQC. Hace mucho tiempo, IBM sustituyó a todos los supervisores de primera línea por un puñado de «gerentes» cuya tarea principal es la formación, mientras que Herman Miller logra una calidad sin defectos y una alta productividad mediante la formación continua y los incentivos para compartir la productividad.
Pero éstas son excepciones. En general, Estados Unidos ha carecido de la metodología para incorporar calidad y productividad al proceso de fabricación. Del mismo modo, nos ha faltado la metodología para trasladar la responsabilidad del proceso y el control del mismo al operador de la máquina, para poner en práctica lo que el matemático Norbert Wiener denominó el «uso humano de los seres humanos».
SQC permite alcanzar ambas aspiraciones tradicionales: alta calidad y productividad, por un lado, trabajo digno de los seres humanos, por el otro. Al cumplir los objetivos de la fábrica tradicional, constituye la piedra angular del edificio de fabricación del siglo XX que diseñaron Frederick Taylor y Henry Ford.
Los mostradores de frijoles no disfrutan de una buena prensa en estos días. Se les culpa de todos los males que afligen a la manufactura estadounidense. Pero los mostradores de frijoles tendrán la última risa. En la fábrica de 1999, la contabilidad de fabricación desempeñará un papel tan importante como siempre y probablemente incluso más importante. Pero los frijoles se contarán de forma diferente. La nueva contabilidad de fabricación, que podría denominarse con mayor precisión «economía de fabricación», difiere radicalmente de la contabilidad de costes tradicional en sus conceptos básicos. Su objetivo es integrar la fabricación con la estrategia empresarial.
La contabilidad de costes de fabricación (el nombre completo de la contabilidad de costes que rara vez se usa) es la tercera pata del taburete (las otras patas son la gestión científica y la línea de montaje) en la que descansa la industria manufacturera moderna. Sin la contabilidad de costes, estos dos nunca habrían sido plenamente eficaces. También es de origen estadounidense. Desarrollada en la década de 1920 por General Motors, General Electric y Western Electric (la división de fabricación de AT&T), la nueva contabilidad de costos, no la tecnología, le dio a GM y GE la ventaja competitiva que los convirtió en líderes mundiales de la industria. Tras la Segunda Guerra Mundial, la contabilidad de costos se convirtió en una importante exportación estadounidense.
Pero para entonces, las limitaciones de la contabilidad de costos también se estaban haciendo evidentes. Cuatro son especialmente importantes. En primer lugar, la contabilidad de costos se basa en las realidades de la década de 1920, cuando la mano de obra directa y de cuello azul representaba 80% de todos los costes de fabricación distintos de las materias primas. En consecuencia, la contabilidad de costes equipara el «costo» con los costes laborales directos. Todo lo demás es «diverso», agrupado como gastos generales.
En estos días, sin embargo, una planta en la que los costos laborales directos son tan altos como el 25%% es una rara excepción. Incluso en los automóviles, la mayor cantidad de mano de obra de las principales industrias, los costos de mano de obra directa en plantas actualizadas (como las que los japoneses están construyendo en Estados Unidos y algunas de las nuevas plantas Ford) han bajado a 18%. Y 8% a 12% se está convirtiendo rápidamente en la norma industrial. Una gran empresa de fabricación con un proceso intensivo en mano de obra, Beckman Instruments, considera ahora que los costos laborales son «varios». Pero, por lo general, los sistemas de contabilidad de costos se siguen basando en costos laborales directos que se tienen en cuenta cuidadosamente, incluso minuciosamente. Los costes restantes, y eso puede significar 80% hasta 90%—se asignan por razones que todo el mundo sabe que son puramente arbitrarias y totalmente engañosas: en proporción directa a los costos laborales de un producto, por ejemplo, o a su volumen en dólares.
En segundo lugar, los beneficios de un cambio en el proceso o en el método se definen principalmente en términos de ahorro de costes laborales. Si se tienen en cuenta otros ahorros, suele ser sobre la base de la misma asignación arbitraria por la que se contabilizan los costos distintos de la mano de obra directa.
Aún más grave es la tercera limitación, incorporada en el sistema tradicional de contabilidad de costes. Al igual que un reloj de sol, que muestra las horas en que brilla el sol pero no da información en un día o una noche nublados, la contabilidad de costes tradicional solo mide los costes de producción. Ignora los costes de no producción, ya sean el resultado del tiempo de inactividad de la máquina o de defectos de calidad que requieren el desguace o la reelaboración de un producto o pieza.
La contabilidad de costes estándar supone que el proceso de fabricación resulta ser buenos productos 80% de la época. Pero ahora sabemos que incluso con el mejor SQC, el tiempo de no producción consume mucho más del 20%% del tiempo total de producción. En algunas plantas, representa 50%. Y el tiempo de no producción cuesta tanto como el tiempo de producción: salarios, calefacción, iluminación, intereses, salarios e incluso materias primas. Sin embargo, el sistema tradicional no mide nada de esto.
Por último, la contabilidad de costes de fabricación supone que la fábrica es una entidad aislada. El ahorro de costes en la fábrica es «real». El resto es «especulación», por ejemplo, el impacto de un cambio en el proceso de fabricación en la aceptación de un producto en el mercado o en la calidad del servicio. La difícil situación de GM desde la década de 1970 ilustra el problema con esta suposición. La gente de marketing no estaba contenta con la decisión de la alta dirección de construir todos los modelos de automóviles, desde Chevrolet hasta Cadillac, con el mismo número reducido de carrocerías, cuadros y motores. Sin embargo, el modelo de contabilidad de costos demostró que tal similitud produciría ahorros sustanciales en los costos laborales Por lo tanto, el argumento de marketing de que los automóviles GM perderían el atractivo de los clientes a medida que se parecían cada vez más se dejó de lado como especulación. En efecto, la contabilidad de costes tradicional difícilmente puede justificar un producto mejora, por no hablar de un producto o proceso innovación. La automatización, por ejemplo, aparece como un coste pero casi nunca como un beneficio.
Todo esto lo conocemos desde hace casi 40 años. Y durante 30 años, académicos de contabilidad, contables gubernamentales, contables de la industria y firmas de contabilidad han trabajado arduamente para reformar el sistema. Han realizado mejoras sustanciales. Sin embargo, dado que los intentos de reforma intentaron basarse en el sistema tradicional, las limitaciones originales permanecen.
Lo que provocó el cambio en la nueva contabilidad de fabricación fue la frustración de los fabricantes de equipos de automatización de fábricas. Los usuarios potenciales, la gente de las plantas, deseaban desesperadamente el nuevo equipo. Pero no se podía convencer a la alta dirección de gastar el dinero en máquinas herramienta o robots controlados numéricamente que podían cambiar rápidamente herramientas, accesorios y moldes. Los beneficios de los equipos automatizados, ahora sabemos, radican principalmente en la reducción del tiempo de no producción al mejorar la calidad (es decir, hacerlo bien la primera vez) y reducir drásticamente el tiempo de inactividad de la máquina al cambiar de un modelo o producto a otro. Sin embargo, la contabilidad de costos de estas ganancias no documenta.
De esta frustración surgió Computer-Aided Manufacturing-International, o CAM-I, un esfuerzo cooperativo de productores de automatización, fabricantes multinacionales y contadores para desarrollar un nuevo sistema de contabilidad de costos. Iniciado en 1986, CAM-I está empezando a influir en las prácticas de fabricación. Pero ya ha desencadenado una revolución intelectual. El trabajo más emocionante e innovador de la gestión actual se encuentra en la teoría de la contabilidad, con nuevos conceptos, nuevos enfoques, nueva metodología, incluso lo que podría llamarse nueva filosofía económica, tomando forma rápidamente. Y si bien existe una enorme controversia sobre los detalles específicos, los lineamentos de la nueva contabilidad de fabricación son cada vez más claros.
Tan pronto como CAM-I comenzó a funcionar, se hizo evidente que el sistema contable tradicional no podía reformarse. Tuvo que ser reemplazado. Los costes laborales son claramente la unidad de medida errónea en la fabricación. Pero, y esta es una nueva visión, también lo son todos los demás elementos de la producción. La nueva unidad de medida tiene que ser hora. Se debe suponer que los costes de un período determinado son fijos; no hay costes «variables». Incluso los costos de los materiales son más fijos que variables, ya que la producción defectuosa utiliza tanto material como una buena producción. Lo único que es variable y controlable es cuánto tiempo lleva un proceso determinado. Y «beneficio» es lo que reduce ese tiempo. De un solo golpe, esta información elimina las tres primeras de las cuatro limitaciones tradicionales de la contabilidad de costos.
Pero los nuevos conceptos de costes van aún más allá al redefinir qué son realmente los costes y los beneficios. Por ejemplo, en el sistema tradicional de contabilidad de costes, el inventario de productos terminados no cuesta nada porque no absorbe mano de obra directa. Se trata como un «activo». Sin embargo, en la nueva contabilidad manufacturera, el inventario de productos terminados es un «costo hundido» (término de economista, no contable). Las cosas que se encuentran en el inventario no ganan nada. De hecho, retiene dinero caro y absorbe tiempo. Como resultado, sus costes de tiempo son elevados. La nueva contabilidad mide estos costes de tiempo frente a los beneficios del inventario de productos terminados (por ejemplo, un servicio al cliente más rápido).
Sin embargo, la contabilidad de fabricación sigue enfrentándose al desafío de eliminar la cuarta limitación de la contabilidad de costes tradicional: su incapacidad de incorporar en la medición del rendimiento de la fábrica el impacto de los cambios de fabricación en el negocio total: el retorno en el mercado de una inversión en automatización, para ejemplo, o el riesgo de no realizar una inversión que aceleraría los cambios de producción. Los costes y beneficios de estas decisiones en la planta pueden resolverse ahora con una precisión considerable. Sin embargo, las consecuencias empresariales son especulativas. Solo se puede decir: «Sin duda, esto debería ayudarnos a conseguir más ventas» o «Si no lo hacemos, corremos el riesgo de quedarnos atrás en el servicio al cliente». Pero, ¿cómo cuantificas esas opiniones?
La fortaleza de la contabilidad de costes siempre ha sido que se limita a lo medible y, por lo tanto, da respuestas objetivas. Pero si los intangibles se incorporan a sus ecuaciones, la contabilidad de costos solo generará más interrogantes. Por lo tanto, se debate acalorado cómo proceder y con razón. Sin embargo, todo el mundo está de acuerdo en que estos impactos empresariales deben integrarse en la medición del rendimiento de la fábrica, es decir, en la contabilidad de fabricación. De una forma u otra, la nueva contabilidad obligará a los gerentes, tanto dentro como fuera de la planta, a tomar decisiones de fabricación como negocio decisiones.
El epigrama de Henry Ford, «El cliente puede tener cualquier color siempre que sea negro», ha entrado en el folclore estadounidense. Pero pocas personas se dan cuenta de lo que quiere decir Ford: la flexibilidad cuesta tiempo y dinero, y el cliente no paga por ello. Aún menos personas se dan cuenta de que a mediados de la década de 1920, la «nueva» contabilidad de costos hizo posible que GM ganara a Ford al ofrecer a los clientes colores y cambios anuales de modelo sin costo adicional.
A estas alturas, la mayoría de los fabricantes pueden hacer lo que GM aprendió a hacer hace unos 70 años. De hecho, muchos van un poco más allá al combinar la estandarización con la flexibilidad. Pueden, por ejemplo, construir una variedad de productos finales a partir de un número bastante reducido de piezas estandarizadas. Sin embargo, los fabricantes tienden a pensar como Henry Ford: se puede tener estandarización a bajo costo o flexibilidad a alto costo, pero no ambas cosas.
La fábrica de 1999, sin embargo, se basará en la premisa de que no solo lata tener ambos pero también mosto tienen ambos, y a bajo costo. Pero para lograrlo, la fábrica tendrá que estructurarse de manera muy diferente.
La fábrica de hoy es un buque de guerra. La planta de 1999 será una «flotilla», formada por módulos centrados en una etapa del proceso de producción o en torno a una serie de operaciones estrechamente relacionadas. Aunque el mando y el control generales seguirán existiendo, cada módulo tendrá su propio mando y control. Y cada uno, al igual que los barcos de una flotilla, será maniobrable, tanto en cuanto a su posición en todo el proceso como en su relación con otros módulos. Esta organización dará a cada módulo los beneficios de la estandarización y, al mismo tiempo, dará mayor flexibilidad a todo el proceso. De este modo, permitirá cambios rápidos en el diseño y el producto, una respuesta rápida a las demandas del mercado y una producción a bajo costo de «opciones» o «especiales» en lotes bastante pequeños.
Hoy en día no existe semejante planta. Nadie puede construirlo todavía. Pero muchos fabricantes, grandes y pequeños, se están moviendo hacia la estructura de la flotilla: entre ellos se encuentran algunas de las plantas estadounidenses de Westinghouse, la planta robótica de Asea Brown Boveri en Suecia y varias grandes plantas de impresión, especialmente en Japón.
El mayor impulso para este desarrollo probablemente se debió al fracaso de GM en obtener un retorno de su enorme (al menos$ 30 mil millones y tal vez$ 40 mil millones) de inversión en automatización. Parece que GM utilizó las nuevas máquinas para mejorar su proceso existente, es decir, para hacer que la línea de montaje sea más eficiente. Sin embargo, el proceso se volvió menos flexible y menos capaz de lograr cambios rápidos.
Mientras tanto, los fabricantes de automóviles japoneses y Ford gastaban menos y alcanzaban más flexibilidad. En estas plantas, la línea sigue existiendo, pero es discontinua en lugar de estar estrechamente unida. El nuevo equipo se utiliza para acelerar los cambios, por ejemplo, para automatizar los cambios de plantillas, herramientas y accesorios. Por lo tanto, la línea ha adquirido una buena parte de la flexibilidad de la producción tradicional por lotes sin perder su estandarización. Por lo tanto, la estandarización y la flexibilidad ya no son una propuesta de lo uno o lo otro. Están, como de hecho deben estar, fusionados.
Sin embargo, esto significa un equilibrio diferente entre estandarización y flexibilidad para diferentes partes del proceso de fabricación. Un equilibrio «promedio» en toda la planta no hará nada muy bien. Si se impone a lo largo de la línea, simplemente se traducirá en una alta rigidez y grandes costos para todo el proceso, que aparentemente es lo que ocurrió en GM. Lo que se requiere es una reorganización del proceso en módulos, cada uno con su propio equilibrio óptimo.
Además, las relaciones entre estos módulos pueden tener que cambiar cada vez que cambia el producto, el proceso o la distribución. Pasar de vender equipo pesado a arrendarlo, por ejemplo, puede cambiar drásticamente la relación entre la producción de productos terminados y la producción de piezas de repuesto. O bien, un cambio de modelo bastante pequeño puede alterar la secuencia en la que las piezas principales se ensamblan en el producto terminado. No hay nada nuevo en esto, por supuesto. Pero bajo la estructura de línea tradicional, tales cambios se ignoran o tardan una eternidad en lograrse. Con la intensificación de la competencia y la reducción de los ciclos de vida de los productos, estos cambios no pueden ignorarse y deben hacerse rápidamente. De ahí la organización modular de la flotilla.
Pero esta organización requiere algo más que un cambio drástico en la estructura física de la fábrica. Requiere, sobre todo, comunicación e información diferentes. En la planta tradicional, cada sector y departamento informa por separado arriba. Y informa de lo que ha pedido arriba. En la fábrica de 1999, los sectores y departamentos tendrán que pensar qué información deben a quién y qué información necesitan de quién. Gran parte de esta información fluirá hacia los lados y a través de las líneas de departamento, no arriba. La fábrica de 1999 será una red de información.
En consecuencia, todos los gerentes de una planta tendrán que conocer y entender todo el proceso, del mismo modo que el comandante destructor debe conocer y entender el plan táctico de toda la flotilla. En la fábrica de 1999, los gerentes tendrán que pensar y actuar como miembros del equipo, teniendo en cuenta el desempeño del conjunto. Sobre todo, tendrán que preguntarse: ¿Qué necesitan saber las personas que ejecutan los demás módulos sobre las características, la capacidad, los planes y el rendimiento de mi unidad? Y, a su vez, ¿qué necesitamos saber en mi módulo sobre el suyo?
El último de los nuevos conceptos que transforman la fabricación es el diseño de sistemas, en el que toda la fabricación se considera un proceso integrado que convierte los materiales en bienes, es decir, en satisfacciones económicas.
Marks & Spencer, la cadena minorista británica, diseñó el primer sistema de este tipo en la década de 1930. Marks & Spencer diseña y prueba los productos (ya sean textiles o alimentos) que ha decidido vender. Designa a un fabricante para fabricar cada producto bajo contrato. Trabaja con el fabricante para producir la mercancía adecuada con la calidad adecuada al precio justo. Por último, organiza la entrega puntual de los productos terminados a sus tiendas. Todo el proceso se rige por una previsión meticulosa de cuándo los productos saldrán de los estantes de las tiendas y se introducirán en las bolsas de compra de los clientes. En los últimos diez años más o menos, esta gestión de sistemas se ha vuelto común en el comercio minorista.
Aunque la organización de sistemas sigue siendo poco frecuente en la fabricación, en realidad se intentó por primera vez allí. A principios de la década de 1920, cuando el Model T estaba en todo su esplendor, Henry Ford decidió controlar todo el proceso de fabricación y traslado de todos los suministros y piezas que necesitaba su nueva planta, el gigantesco River Rouge. Construyó su propia fábrica de acero y vidrio. Fundó plantaciones en Brasil para cultivar caucho para neumáticos. Compró el ferrocarril que traía suministros al río Rouge y se llevó los vagones terminados. Incluso jugó con la idea de construir sus propios centros de servicio en todo el país y dotarlos de mecánicos capacitados en escuelas propiedad de Ford. Pero Ford concibió todo esto como un edificio financiero unido por la propiedad. En lugar de construir un sistema, construyó un conglomerado, un monstruo difícil de manejar que era caro, inmanejable y horriblemente poco rentable.
En cambio, el nuevo sistema de fabricación no está «controlado» en absoluto. La mayoría de sus piezas son independientes: proveedores independientes en un extremo y clientes en el otro. Tampoco se centra en la planta, como lo estaba la organización de Ford. El nuevo sistema considera que la planta es poco más que un lugar amplio en el flujo de fabricación. La planificación y la programación comienzan con el envío al cliente final, al igual que en Marks & Spencer. Hay que diseñar retrasos, paradas y redundancias en el sistema: un almacén aquí, un suministro adicional de piezas y herramientas allí, un stock de productos antiguos que ya no se fabrican pero que el mercado sigue demandando ocasionalmente. Son imperfecciones necesarias en un flujo continuo que se rige y dirige por la información.
Lo que ha empujado a los fabricantes estadounidenses a diseñar sistemas de este tipo es el problema que encontraron al copiar los métodos just-in-time de Japón para suministrar materiales y piezas a las plantas. El problema podría haberse predicho, ya que el esquema japonés se basa en condiciones sociales y logísticas únicas de ese país y desconocidas en Estados Unidos. Sin embargo, el cambio parecía a los fabricantes estadounidenses una cuestión de procedimiento, de hecho, casi trivial. Sin embargo, empresa tras empresa descubrieron que la entrega puntual de suministros y piezas creaba turbulencias en todas sus plantas. Y aunque nadie podía entender cuál era el problema, lo único que quedó claro fue que con las entregas justo a tiempo, la planta ya no funciona como un proceso paso a paso que comienza en el muelle de recepción y termina cuando los productos terminados se trasladan a la sala de embarque. En cambio, la planta debe rediseñarse desde el extremo hacia atrás y gestionarse como un flujo integrado.
Expertos en fabricación, ejecutivos y profesores han instado a este enfoque desde hace dos o tres décadas. Y algunas industrias, como la refinación de petróleo y la construcción a gran escala, lo practican. Pero, en general, las plantas de fabricación estadounidenses y europeas no están diseñadas ni gestionadas por sistemas. De hecho, pocas empresas tienen suficiente conocimiento sobre lo que sucede en sus plantas para ejecutarlas como sistemas. Sin embargo, la entrega justo a tiempo obliga a los gerentes a hacer preguntas sobre los sistemas: ¿En qué parte de la planta necesitamos redundancia? ¿Dónde debemos colocar la carga de los ajustes? ¿En qué costos deberíamos incurrir en un lugar para minimizar el retraso, el riesgo y la vulnerabilidad en otro?
Algunas empresas incluso están empezando a extender el concepto de sistemas de fabricación más allá de la planta y en el mercado. Caterpillar, por ejemplo, organiza su fabricación para suministrar cualquier pieza de repuesto en cualquier parte del mundo en un plazo de 48 horas. Pero las empresas como esta siguen siendo excepciones; deben convertirse en la regla. En cuanto definimos la fabricación como el proceso que convierte las cosas en satisfacciones económicas, queda claro que la producción no se detiene cuando el producto sale de fábrica. La distribución física y el servicio de productos siguen formando parte del proceso de producción y deben integrarse con él, coordinarse con él y gestionarse junto con él. Ya se reconoce ampliamente que el mantenimiento del producto debe ser una consideración importante durante su diseño y producción. En 1999, la fabricación de sistemas tendrá una influencia cada vez mayor en la forma en que diseñamos y remodelamos las plantas y en cómo gestionamos las empresas de fabricación.
Tradicionalmente, las empresas manufactureras se han organizado «en serie», con funciones como ingeniería, fabricación y marketing como pasos sucesivos. En la actualidad, ese sistema suele complementarse con una organización de equipo paralela (los equipos de gestión de productos de Procter & Gamble son un ejemplo bien conocido), que reúne varias funciones desde el inicio de un nuevo proyecto de producto o proceso. Sin embargo, si la fabricación es un sistema, cada decisión de una empresa manufacturera se convierte en una decisión de fabricación. Cada decisión debe cumplir con los requisitos y necesidades de fabricación y, a su vez, debe explotar los puntos fuertes y las capacidades del sistema de fabricación particular de una empresa.
Cuando Honda decidió hace seis o siete años fabricar un auto nuevo y exclusivo para el mercado estadounidense, el debate estratégico más acalorado no era sobre diseño, rendimiento o precio. Se trataba de distribuir el Acura a través de la consolidada red de concesionarios de Honda o crear un nuevo segmento de mercado mediante la construcción de concesionarios Acura independientes a un alto costo y riesgo. Se trataba de una cuestión de marketing, por supuesto. Pero la decisión fue tomada por un equipo de personal de diseño, ingeniería, fabricación y marketing. Y lo que inclinó la balanza hacia la red de concesionarios separados fue una consideración de fabricación: el diseño para el que la distribución y el servicio independientes tenían más sentido era el diseño que mejor aprovechaba las capacidades de fabricación de Honda.
La plena realización del concepto de sistemas en la fabricación está a años de distancia. Puede que no necesite un nuevo Henry Ford. Sin embargo, sin duda requerirá una gestión muy diferente y gerentes muy diferentes. Todos los gerentes del negocio de fabricación del mañana tendrán que conocer y comprender el sistema de fabricación. Es muy posible que adoptemos la costumbre japonesa de iniciar a todos los nuevos directivos en la planta y en trabajos de fabricación durante los primeros años de su carrera. De hecho, podríamos ir aún más lejos y exigir a los gerentes de toda la empresa que roten en puestos de fábrica a lo largo de sus carreras, del mismo modo que los oficiales del ejército regresan regularmente al servicio de las tropas.
En el nuevo negocio de fabricación, la fabricación es el integrador que une todo. Crea el valor económico que paga por todo y por todos. Por lo tanto, el mayor impacto del concepto de sistemas de fabricación no se producirá en el proceso de producción. Al igual que con SQC, su mayor impacto será en las preocupaciones sociales y humanas, por ejemplo, en las carreras profesionales, o lo que es más importante, en la transformación de funcional gerentes en negocio gerentes, cada uno con un papel específico, pero todos miembros de la misma producción y del mismo elenco. Y seguramente, las empresas manufactureras del mañana no estarán dirigidas por ejecutivos financieros, comercializadores o abogados sin experiencia en manufactura, como lo hacen hoy tantas empresas estadounidenses.
Existen diferencias importantes entre estos cuatro conceptos. Considera, por ejemplo, lo que cada uno quiere decir con «la fábrica». En SQC, la fábrica es un lugar donde trabaja la gente. En la contabilidad de gestión y en el concepto de fabricación flexible de la flotilla, es un lugar donde se trabaja; no importa si son personas, ratones blancos o robots. En el concepto de sistemas, la fábrica no es un lugar en absoluto; es una etapa de un proceso que añade valor económico a los materiales. En teoría, al menos, la fábrica no puede y ciertamente no debe diseñarse, y mucho menos construirse, hasta que se comprenda todo el proceso de «fabricación», hasta llegar al cliente final. Así pues, definir la fábrica es mucho más que un ejercicio teórico o semántico. Tiene consecuencias prácticas inmediatas en el diseño, la ubicación y el tamaño de la planta; en qué actividades se van a agrupar en un complejo de fabricación; incluso en cuánto y en qué invertir.
Del mismo modo, cada uno de estos conceptos refleja una mentalidad particular. Para aplicar SQC, no tienes que pensar, tienes que hacerlo. La contabilidad de gestión se centra en el análisis técnico, mientras que el concepto de flotilla se centra en el diseño de la organización y el flujo de trabajo. En el concepto de sistemas, hay una gran tentación de seguir pensando y nunca llegar a hacer nada. Cada concepto tiene sus propias herramientas, su propio lenguaje y se dirige a diferentes personas.
Sin embargo, lo que estos cuatro conceptos tienen en común es mucho más importante que sus diferencias. En ninguna parte es más evidente que en su suposición de que el proceso de fabricación es una configuración, un todo que es mayor que la suma de sus partes. Los enfoques tradicionales consideran la fábrica como un conjunto de máquinas individuales y operaciones individuales. La fábrica del siglo XIX era un conjunto de máquinas. La dirección científica de Taylor dividió cada trabajo en operaciones individuales y luego juntó esas operaciones en trabajos nuevos y diferentes. Los conceptos «modernos» del siglo XX (la línea de montaje y la contabilidad de costes) definen el rendimiento como la suma de las operaciones de menor costo. Pero ninguno de los nuevos conceptos tiene mucho que ver con el rendimiento de las piezas. De hecho, las partes como tales solo pueden tener un rendimiento inferior. El proceso produce resultados.
La dirección también reflejará esta nueva perspectiva. SQC es la más convencional en sus implicaciones para los directivos, ya que no cambia tanto su trabajo sino que traspasa gran parte de él a la fuerza laboral. Pero incluso los gerentes sin responsabilidad empresarial (y bajo SQC, los empleados de la planta no tienen ninguna) tendrán que gestionar con conciencia de las consideraciones empresariales mucho más allá de la planta. Y cada gerente de fabricación será responsable de integrar a las personas, los materiales, las máquinas y el tiempo. Por lo tanto, cada gerente de fabricación durante diez años tendrá que aprender y practicar una disciplina que integre la ingeniería, la gestión de personas y la economía empresarial en el proceso de fabricación. Por supuesto, bastantes fabricantes ya están haciendo esto, aunque por lo general no son conscientes de que están haciendo algo nuevo y diferente. Sin embargo, esta disciplina no se ha sistematizado y todavía no se enseña en las escuelas de ingeniería ni en las escuelas de negocios.
Estos cuatro conceptos son sinérgicos en el mejor sentido de este término tan abusado. Juntos, pero solo juntos, abordan los conflictos que más han preocupado a las plantas de producción masiva tradicionales del siglo XX: los conflictos entre las personas y las máquinas, el tiempo y el dinero, la estandarización y la flexibilidad, y las funciones y los sistemas. La clave es que cada uno de estos conceptos define el rendimiento como productividad y concibe la fabricación como el proceso físico que añade valor económico a los materiales. Cada uno trata de aportar valor económico de una manera diferente. Pero comparten la misma teoría de fabricación.
— Escrito por Peter F. Drucker