La fábrica oculta
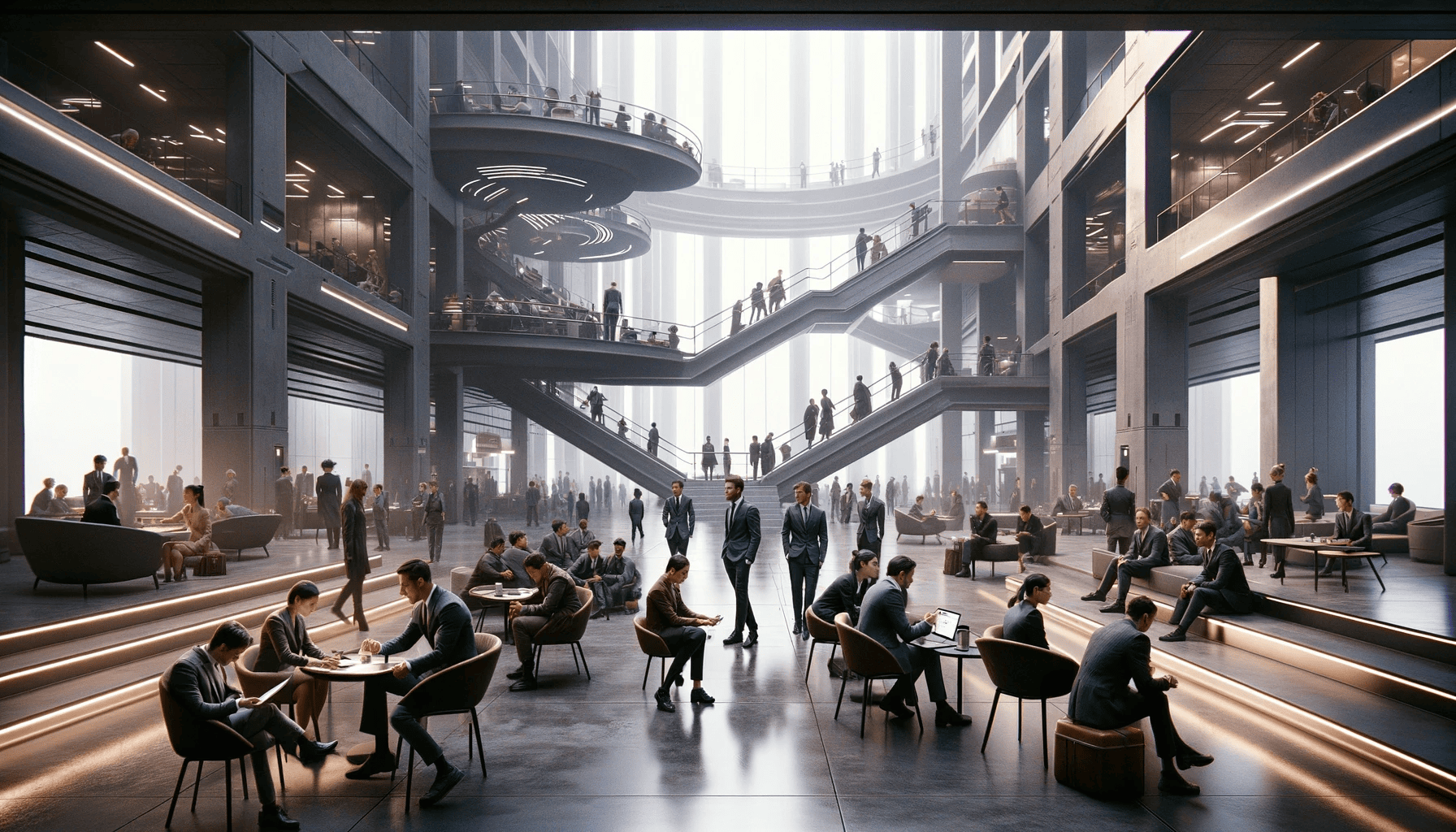
Si bien la atención mundial se centra en la lucha por aumentar la productividad y desarrollar nuevas tecnologías, los gerentes de fabricación, especialmente los de la industria electrónica y de equipos mecánicos (maquinaria), libran discretamente una batalla diferente: la batalla para superar los gastos generales. De hecho, nuestra investigación muestra que los gastos generales solo están por detrás de la calidad y que la comercialización de nuevos productos según lo programado es una de las principales preocupaciones de los ejecutivos de fabricación.
La razón de esta preocupación es obvia: los elevados gastos generales de fabricación tienen un efecto dramático en los beneficios y la competitividad, y los gerentes de fabricación creen que están mal equipados para gestionar bien estos costes. Como nos dijo un alto ejecutivo: «Hemos sido educados para administrar en un mundo en el que las tasas de carga [las proporciones de los costos generales con respecto a los costos laborales directos] son 100% hasta 200% o así. Pero ahora algunas de nuestras plantas funcionan con tasas de carga de más de 1.000%. ¡Ni siquiera sabemos qué significa eso!»
Estamos convencidos de que esta atención renovada a los gastos generales no es un fenómeno cíclico. Sin duda, la baja utilización de la capacidad representó cierto aumento de la conciencia durante la última recesión; aun así, la conciencia se ha mantenido alta durante toda la recuperación. Los gastos generales como porcentaje del valor añadido en la industria estadounidense y como porcentaje de los costos totales de fabricación han aumentado de manera constante durante más de 100 años, ya que la relación entre los costos laborales directos y el valor añadido ha disminuido (véase el Gráfico I). Además, en el entorno actual, los gerentes de producción tienen un apalancamiento más directo para mejorar la productividad mediante la reducción de los gastos generales que mediante la poda de mano de obra directa.
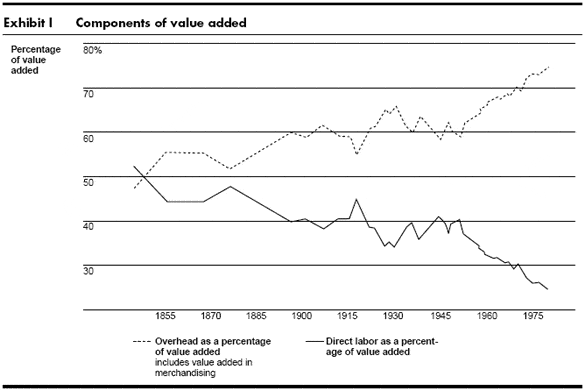
Anexo I Componentes de valor añadido
A medida que las fábricas estadounidenses aumentan el ritmo de la automatización, se dan cuenta de que están siendo afectadas dos veces: en primer lugar, los costos generales aumentan en términos porcentuales a medida que disminuyen los costos laborales directos (todo tiene que sumar un 100%).%); y en segundo lugar, los costes generales aumentan en términos reales debido al aumento de los costos de soporte asociados con el mantenimiento y la ejecución de los equipos automatizados.
El Anexo II muestra cómo los gastos generales como porcentaje del valor añadido aumentan a medida que una industria representativa (la electrónica) disminuye su ciclo de vida producto-proceso.1 Las empresas especializadas altamente personalizadas y de bajo volumen, como las del segmento de sistemas gubernamentales de la industria, llevan a cabo operaciones tipo taller con una proporción relativamente baja de gastos generales en relación con la mano de obra directa. Por el contrario, en las empresas que producen productos estandarizados de gran volumen en entornos automatizados, como en el segmento de microcomputadoras de la industria, la relación entre gastos generales y costos laborales directos es notablemente mayor.
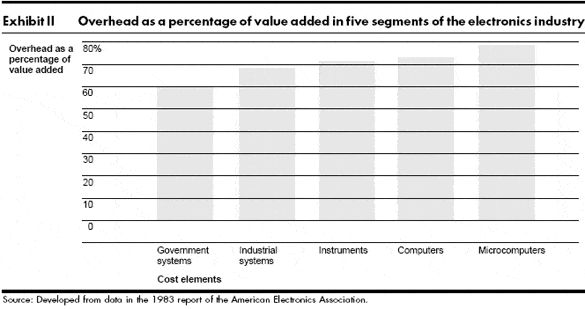
Anexo II Gastos generales como porcentaje del valor añadido en cinco segmentos de la industria electrónica Fuente: Elaborado a partir de los datos del informe de 1983 de la Asociación Americana de Electrónica.
Nuestros datos sugieren que, en todo el espectro de la industria estadounidense, los gastos generales de fabricación promedios son de 35% de los costes de producción; la cifra comparable para los productos japoneses es 26%, a pesar de que los japoneses se han automatizado rápidamente. El diferencial es particularmente grande en las industrias electrónica y de maquinaria, donde los gastos generales estadounidenses representan el 70%% hasta 75% de valor añadido, y el de Japón por 50% a 60%. (Consulte el inserto titulado «Nota de los autores sobre métodos de investigación» para obtener una descripción de los métodos y datos que utilizamos).
Nota de los autores sobre métodos de investigación
La investigación sobre la que se apoyan los datos y las conclusiones de este artículo procede de dos fuentes distintas. La mayoría de los datos cuantitativos provienen de la «Encuesta de Futuros Manufactureros de América del Norte» de 1984, que administramos. Los conocimientos sobre las estructuras de gastos generales de la industria electrónica, así como los problemas de gestión y los problemas que las rodean, provienen de entrevistas estructuradas y análisis de datos de cuatro fábricas de productos electrónicos en los Estados Unidos y de posteriores visitas de seguimiento a muchas otras plantas de electrónica y otros industrias en los Estados Unidos y el Lejano Oriente. La Mesa Redonda de Fabricación de la Universidad de Boston patrocinó ambos esfuerzos de recopilación de datos.
Manufacturing Futures Project es un estudio anual de las estrategias competitivas, preocupaciones, actividades recientes y planes que los fabricantes norteamericanos están elaborando para mejorar su eficacia operativa. En la encuesta de 1984, los encuestados incluyeron a más de 200 ejecutivos sénior de fabricación en tantas unidades de negocio diferentes (el título típico de los encuestados era vicepresidente de fabricación). Las unidades de negocio participantes provenían de una amplia gama de industrias, que clasificamos en cinco clases: electrónica, productos envasados de consumo, maquinaria, industrias básicas (productos químicos, metales, papel) y otros productos industriales. En 1984, tercer año consecutivo en que realizamos la encuesta en Norteamérica, nuestros colaboradores de la Universidad de Waseda de Tokio y del INSEAD en Francia la administraron también a más de 200 unidades de negocio tanto en Japón como en Europa.
La «Encuesta sobre futuros manufactureros» contiene más de 50 preguntas de varias partes. Un pequeño número (los relacionados con la gestión de los gastos generales) constituyeron la base del análisis de este artículo. Por ejemplo, una pregunta de la encuesta requería que los encuestados indicaran en una escala de cinco puntos el grado de preocupación sobre 32 posibles áreas problemáticas. Las cinco principales preocupaciones fueron las siguientes (el número entre paréntesis indica la puntuación escalada media dada cada posible preocupación de todos los encuestados de la encuesta):
1. Producir con altos estándares de calidad (3,98).
2. Presentación de nuevos productos según lo previsto (3.56).
3. Gastos generales elevados o crecientes (3,55).
4. Baja productividad laboral indirecta, incluido el trabajo de cuello blanco (3,44).
5. Problemas de rendimiento y rechazos (3,28).
Las personas de las industrias electrónica y de maquinaria fueron las más preocupadas por los gastos generales y la productividad laboral indirecta, aunque la preocupación por estas áreas fue elevada en los cinco grupos industriales analizados. Para reducir el foco de nuestras investigaciones posteriores, decidimos concentrarnos en los problemas de la gestión de los gastos generales en la industria electrónica. Nuestro razonamiento era que este grupo industrial había demostrado ser un referente para otras industrias durante la historia del Proyecto de Futuros de Fabricación.
Además, numerosas visitas a las plantas nos convencieron de que muchos de los problemas de gestión de los gastos generales en esta industria en rápida evolución se reflejaban en otras industrias, especialmente en el grupo de maquinaria. Los niveles muy elevados de inversión de capital y consumo de energía requeridos en los grupos de la industria básica y de bienes de consumo cambian sustancialmente la estructura de costes (y, por lo tanto, la naturaleza de los problemas de gestión de los gastos generales), aunque creemos que gran parte de lo que tenemos que decir es relevante para esos grupos.
Nuestras investigaciones de campo incluyeron extensos recorridos y entrevistas en cuatro plantas de la industria electrónica: dos centradas en la fabricación de componentes y dos en el montaje de equipos de gran volumen. Huelga decir que también dedicamos un tiempo considerable a discutir los gastos generales con los contadores y los gerentes de las plantas.
Para desarrollar datos comparables sobre los gastos generales, seguimos varias convenciones. En primer lugar, agrupamos todos los gastos generales en un solo grupo. En segundo lugar, hemos desagregado todos los costes para que se incluyan en categorías que se excluyen mutuamente. Por ejemplo, colocamos todos los costes de depreciación y espacio en la categoría de «instalaciones», aunque una empresa concreta podría seguir la práctica de asignar los costes de depreciación a subunidades organizativas, como las compras, y acumularlos en un coste total de compra (que pondríamos en «gastos generales de materiales»). categoría).
Enfoque en las transacciones
Para los gerentes, el paso crítico para controlar los gastos generales consiste en desarrollar un modelo que relacione estos costos con las fuerzas que los respaldan. La mayoría de los gerentes de producción entienden qué es lo que impulsa los costos directos de mano de obra y materiales, pero son mucho menos conscientes de lo que impulsa los costos generales. Es cierto que tenemos modelos que los contadores utilizan, al igual que los estándares de ingeniería y las listas de materiales, para relacionar los costes generales con los productos producidos. Pero estos modelos no hacen tanto explicar gastos generales como asignar ellos.
La mayoría de estos esfuerzos utilizan los estándares de ingeniería y los modelos de listas de materiales que entendemos como base para asignar gastos generales que no entendemos. Estos esfuerzos basan las tasas de sobrecarga en mano de obra directa, materiales u horas de máquina. El problema de este enfoque es que la fuerza impulsora de la mayoría de los gastos generales no es la producción unitaria ni la mano de obra directa. Los costos generales suelen correlacionarse con los productos unitarios, pero eso no significa que los productos unitarios «causen» costos generales. De hecho, actuar como si estuvieran relacionados causalmente lleva a los gerentes a concentrarse en las medidas de producción o en la mano de obra directa en lugar de en las actividades estructurales que determinan los costos generales. (Consulte el inserto titulado «Costos generales definidos»).
Costes generales definidos
En principio, los gastos generales de fabricación son fáciles de definir: incluyen todos los costos directos y asignados de fabricación distintos de la mano de obra directa y los materiales adquiridos. Entre estos costes se encuentran los siguientes:
- Mano de obra indirecta, incluidos los salarios de los trabajadores por hora que no contribuyen directamente a la fabricación de un producto, sino que consisten principalmente en mano de obra dedicada a la manipulación, el mantenimiento, el control de calidad y la inspección de materiales.
- Gastos generales y administrativos como administración de personal, contabilidad de costes, seguridad, salarios para la gestión de la planta y supervisión laboral directa, así como asignaciones corporativas para servicios compartidos y personal corporativo.
- Costos de instalaciones y equipos tales como seguros, depreciación de equipos de planta y herramientas. Estos costos también incluyen los alquileres y otros gastos relacionados con las instalaciones, como los costos de energía y servicios públicos. (Tenga en cuenta que en las industrias basadas en procesos, los costos de energía pueden constituir el componente más importante de los gastos generales y los costos totales. Nuestros datos sugieren que la energía representa alrededor de 4% de los costes totales de fabricación de una planta típica de la industria electrónica o de maquinaria.)
- Costes de ingeniería como los salarios de los ingenieros industriales, industriales y de otro tipo que se ocupan del diseño y el mantenimiento del proceso de producción en sí.
- Costos generales de materiales, incluidos los relacionados con la aprovisionamiento, el movimiento (con la excepción de los costes de manipulación de materiales de la planta de producción relegados a la categoría de mano de obra indirecta) y la coordinación de materias primas, componentes, subconjuntos y productos terminados. Estos costos también incluyen los salarios del personal de compras, planificación de producción, recepción, almacén, tráfico y sistemas de fabricación.
Esta figura muestra la distribución media de estas categorías de costes en las cuatro plantas de electrónica que examinamos. Ninguna de estas plantas mantuvo sus cuentas generales exactamente de la manera que hemos descrito. Aunque sus categorías básicas eran las mismas, cada una había inventado una nomenclatura y una taxonomía algo diferentes para hacer un seguimiento de estos costos. Para llegar a un conjunto de números relativamente consistente (y comparable), tuvimos que refundar los costos de cada una de estas plantas.
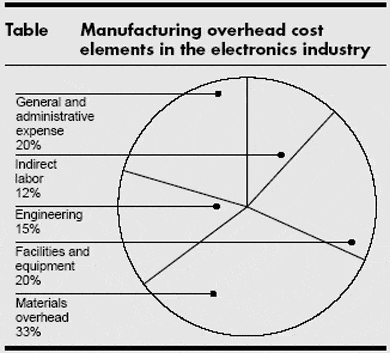
Tabla Elementos de costes generales de fabricación en la industria electrónica
La producción unitaria impulsa la entrada directa de mano de obra y materiales en el taller real que todos pensamos cuando imaginamos una fábrica. Pero en la «fábrica oculta», donde se acumula la mayor parte de los gastos generales de fabricación, la verdadera fuerza motriz proviene de las transacciones, no de los productos físicos. Estas transacciones implican intercambios de los materiales y/o la información necesarios para hacer avanzar la producción, pero no dan lugar directamente a productos físicos. Por el contrario, estas transacciones son responsables de aspectos del «producto ampliado» o «paquete de productos» que los clientes compran, como la entrega puntual, la calidad, la variedad y el diseño mejorado.
Para ver claramente cómo la fábrica oculta genera gastos generales, debemos identificar los tipos básicos de transacción que realizan las personas cuyos salarios y salarios representan los siguientes costes.
Transacciones logísticas, que ordenan, ejecutan y confirman el movimiento de materiales de un lugar a otro. Estas transacciones son procesadas, rastreadas y analizadas por muchos de los trabajadores indirectos del taller, así como por las personas de recepción, expedición, envío, entrada de datos, procesamiento de datos y contabilidad. Para la industria electrónica, calculamos que el procesamiento de tales transacciones representa el 10%% al 20% de los gastos generales totales de fabricación.
Balance de transacciones, que garantizan que los suministros de materiales, mano de obra y capacidad sean iguales a la demanda. Esto da lugar a las órdenes de movimiento y autorizaciones que generan transacciones logísticas.
Las personas involucradas en el procesamiento de estas transacciones incluyen personal de compras, planificación de materiales y control (que convierte los programas maestros y los pedidos de los clientes en requisitos de materiales y pedidos de compra y de tienda), así como personal de recursos humanos (que convierten estas demandas en requisitos de mano de obra). También se incluyen los gerentes que procesan y autorizan las previsiones y que convierten los pedidos en planes de producción y programas maestros. Estimamos que estas transacciones también representan el 10%% al 20% de gastos generales de fabricación en la fabricación de productos electrónicos.
Transacciones de calidad, que van mucho más allá de lo que solemos considerar como control de calidad, ingeniería indirecta y aprovisionamiento, e incluyen la identificación y comunicación de especificaciones, la certificación de que otras transacciones se han realizado como se suponía que debían realizarse y el desarrollo y registro de datos relevantes. En la industria electrónica, las transacciones de calidad suman un 25%% hasta 40% de gastos generales de fabricación.
Transacciones de cambio, que actualizan los sistemas básicos de información de fabricación para adaptarse a los cambios en los diseños de ingeniería, programas, rutas, normas, especificaciones de materiales y listas de materiales. Estas transacciones implican el trabajo de ingenieros de fabricación, industriales y de calidad, junto con una parte del esfuerzo invertido en compras, control de materiales, entrada de datos y procesamiento de datos.
Las transacciones de cambio pueden ocurrir una y otra vez. La primera vez que diseñas un producto, por ejemplo, realizas transacciones con una lista de materiales; cada vez que procesas una orden de cambio de diseño (ECO) para ese producto, tienes que volver a tramitar la factura. La realización y deshacer las transacciones logísticas, de equilibrio y de calidad que resultan de las transacciones de cambio llevan a las empresas a incurrir en gastos generales dos, tres veces o más, según la estabilidad de sus entornos de fabricación. En general, las transacciones de cambio representan 20% hasta 40% de gastos generales en la fabricación de productos electrónicos.
Gestión de transacciones de gastos generales
Si, como creemos, las transacciones son responsables de la mayoría de los gastos generales en la fábrica oculta, entonces la clave para gestionar los gastos generales es controlar las transacciones que las impulsan. Por gestión de transacciones, nos referimos a pensar consciente y cuidadosamente qué transacciones son apropiadas y cuáles no y cómo hacer las transacciones importantes de la manera más eficaz. Los fabricantes han aplicado rigurosamente este tipo de análisis a la mano de obra directa desde los días de Frederick Taylor. Sin embargo, ahora que los costos generales superan con creces los costos laborales directos, los gerentes deben redirigir sus esfuerzos analíticos.
Análisis de transacciones
Los criterios de diseño utilizados en el desarrollo de la mayoría de los productos y procesos de producción rara vez tienen en cuenta los costes generales, y mucho menos los costes de transacción que implican los diseños alternativos. Es posible, por ejemplo, eliminar numerosas transacciones mediante el diseño de procesos de producción de ciclo corto sin ningún inventario de trabajo en proceso (WIP) que requiera transacciones logísticas, de balanceo o de calidad. Esto es lo que han hecho los japoneses con su filosofía de diseño de procesos «justo a tiempo», que «arrastra» el trabajo a través de la fábrica solo cuando lo necesitan las operaciones posteriores. Este enfoque elimina gran parte de la necesidad de sistemas de control de planta o seguimiento de WIP elaborados y que consumen mucho tiempo.
Un producto electrónico que se rediseñó para satisfacer las presiones de la competencia ofrece un claro ejemplo de lo que puede hacer un sistema de producción de bajas transacciones. Antes del rediseño, el producto contenía más de 700 piezas, la mayoría de las cuales debían pedirse a un proveedor semanalmente y luego colocarse en un inventario de materiales antes de retirarse por lotes y llevarse al área de montaje final. La planta enviaba la producción semanal a un inventario de productos terminados en el sistema de distribución de la empresa. El recuento del número de transacciones mensuales requeridas por este sistema es el siguiente:
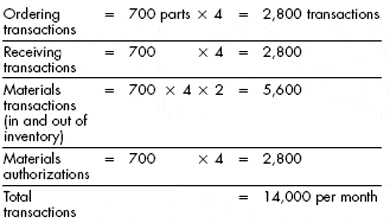
Tras un estudio cuidadoso, la dirección decidió que:
1. Los cambios en el diseño del producto y las especificaciones del proveedor podrían reducir el número de piezas de 700 a 200.
2. La fábrica podría emitir pedidos generales en lugar de órdenes de compra separadas de materiales y podría proporcionar a los proveedores tarifas de envío mensuales. La necesidad de piezas adicionales quedaría indicada por la devolución de un contenedor vacío de tamaño estándar.
3. Un procedimiento sencillo de recepción e inspección que requiere que el albarán se envíe directamente a la contabilidad al recibir el contenedor podría reemplazar el complicado proceso actual. Como resultado, la empresa tendría que enviar solo un cheque por mes a cada proveedor por los productos realmente recibidos.
4. Entregar las piezas directamente en el suelo podría eliminar el inventario de materiales, la necesidad de guardar los materiales, la emisión de autorizaciones para retirarlos y el trabajo de retirarlos de nuevo.
5. Un flujo de producción fluido haría evidentes inmediatamente los problemas de calidad y cambiaría el enfoque de la administración, desde el mantenimiento de registros exhaustivos hasta la prevención y la corrección inmediata.
Esta fábrica está ahora bien encaminada a implementar un sistema de producción con muchas menos transacciones mensuales:

Huelga decir que los gastos generales de esta fábrica se han desplomado, al igual que los costos de inventario. En algunas áreas, por ejemplo, la recepción, el número de transacciones ha aumentado, pero un examen minucioso de los pasos necesarios para llevar a cabo las transacciones en la fábrica oculta ha simplificado enormemente el flujo de trabajo y ha reducido los costes totales de transacción. Los gerentes solo tenían que estudiar el proceso de transacción de la fábrica oculta de la misma manera que han examinado durante mucho tiempo el proceso de producción de la fábrica visible.
Otra forma de mejorar la sobrecarga basada en transacciones es reducir la «granularidad» de los datos que se informan. Cada sistema de fabricación incorpora decisiones sobre la precisión y la frecuencia con la que se deben informar los datos de las transacciones. No tiene sentido procesar más datos de los necesarios o con más frecuencia de la necesaria.
Una empresa, por ejemplo, descubrió que su sistema de transacciones de calidad recopilaba y conservaba datos de calidad sobre todas las actividades posibles, a pesar de la muy mala calidad de sus productos. El departamento de calidad a menudo se quejaba de que nunca había tenido tiempo de analizar los datos, que se encontraban en archivadores y archivos informáticos, porque dedicaba todo su tiempo a recopilar. Al centrarse en las pocas áreas clave en las que existían la mayoría de los problemas de calidad, el departamento pudo mejorar drásticamente la calidad a la vez que redujo los costos. Procesaba transacciones de calidad de forma más intensiva en las áreas clave y mucho menos intensamente donde las cosas funcionaban sin problemas.
Estabilidad
Quizás la forma más sencilla de reducir el número de transacciones es estabilizar el entorno de fabricación. Muchas empresas estadounidenses están ahora tratando agresivamente de implementar enfoques japoneses justo a tiempo, pero los visitantes de Japón a menudo se sorprenden de lo que ven aquí. En Japón, el primer principio es la estabilidad, y se hace un gran esfuerzo para diseñar el proceso hasta el más mínimo detalle y formar a los trabajadores para que sigan las instrucciones al pie de la letra. Las cargas niveladas, los flujos de trabajo equilibrados y el buen mantenimiento ayudan a garantizar que lo inesperado no desestabilice las operaciones.
Cada vez que se emite un pedido de cambio de diseño, un cronograma se rompe o surge un problema de calidad, una ola de nuevas transacciones fluye a través de una planta. La política de «hacer lo correcto a la primera» se aplica al procesamiento de transacciones al igual que a la fabricación de productos. Estos cambios no solo aumentan el número de transacciones, sino que también tienen un efecto secundario importante. La inestabilidad en los cronogramas y el rendimiento de la planta hace que muchos gerentes de planta sobrecarguen sus fuerzas de trabajo para que las plantas puedan reaccionar ante picos de carga inesperados en el volumen de transacciones. Como dijo un veterano gerente de planta: «Tienes que mantener a las tropas de choque en reserva para manejar los problemas que surjan».
Una de las razones del bajo porcentaje de valor añadido atribuido a los gastos generales en las fábricas japonesas es que sus plantas son más estables que las nuestras. Su forma de manejar los pedidos de cambio de diseño es un buen ejemplo. El Anexo III muestra la frecuencia con la que las plantas electrónicas japonesas y estadounidenses autorizan cambios de diseño. Los japoneses procesan menos pedidos de cambio de diseño que sus homólogos estadounidenses (aproximadamente dos tercios menos) y autorizan estos cambios con mucha más antelación y, por lo tanto, permiten cargas de transacciones más estables y niveladas. Con más planificación, hay menos errores.
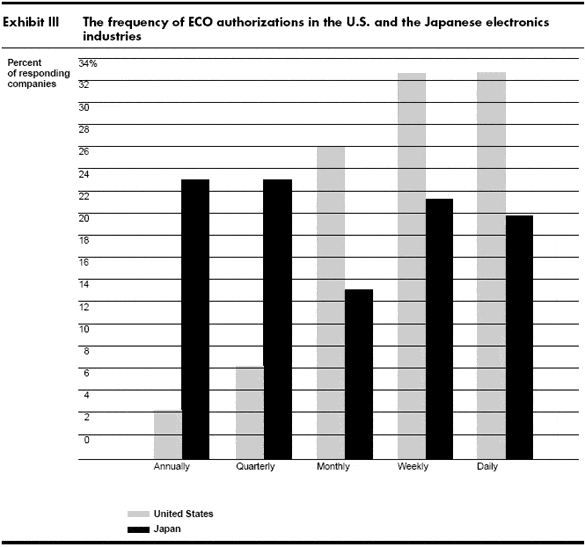
Anexo III Frecuencia de las autorizaciones ECO en las industrias electrónica de EE. UU. y Japón
Automatización
Una de las formas más comentadas de reducir los gastos generales asociados a la fábrica oculta es la automatización. Los robots pueden desempeñar un papel en los sofisticados sistemas de control de materiales que automatizan las transacciones logísticas; los láseres pueden leer códigos de barras y eliminar la necesidad de que los operadores de entrada de datos registren manualmente las transacciones de movimiento; la inspección asistida por computadora puede ayudar a reducir los costos de procesamiento de transacciones de calidad; El sistema de planificación de requisitos de materiales que funciona sin problemas puede abaratar el procesamiento de transacciones de balance.
El costo de procesar las transacciones manualmente puede ser diez veces mayor que el de procesarlas automáticamente. Sin embargo, el problema no es solo el costo de la transacción, sino también la efectividad del proceso de transacción. Además de los costos de lectura, distribución, archivo y recuperación, las transacciones manuales suelen tener un problema mucho más grave: tardan demasiado. El tiempo de respuesta es claramente un problema importante en la fabricación estadounidense en la actualidad, pero sabemos de empresas que tardan entre 5 y 15 días hábiles en convertir un pedido de un cliente en la forma adecuada para su fabricación. Una transacción manual basada en la recuperación de información de un archivador, la lectura del documento para comprender las condiciones, realizar la transacción, enviar los resultados y volver a archivar puede tardar 100 veces más que una transacción comparable realizada en un entorno con soporte informático.
Quizás el medio más importante de automatizar las transacciones sea utilizar sistemas informáticos tan bien integrados que los datos solo necesitan introducirse una vez. En prácticamente todas las grandes empresas, sin embargo, sigue habiendo una redundancia masiva de transacciones debido a la existencia de subsistemas que no pueden «comunicarse» entre sí. Estos problemas existen tanto en la fabricación como entre la fabricación y otras funciones.
Los sistemas integrados ofrecen más que eficiencia; también pueden mejorar la precisión y la comprensión. Cuando los mismos datos se guardan en varios lugares y las unidades organizativas independientes calculan de forma independiente hechos tales como envíos mensuales, el resultado son registros redundantes, procesamiento redundante de transacciones y confusión general. No es raro que los gerentes pidan a producción, marketing y finanzas que proporcionen los datos de envío de unidades de un producto y que obtienen tres respuestas diferentes.
Los sistemas informáticos debidamente diseñados e integrados deberían llevar a que las transacciones se realicen una sola vez y a menos confusión. Los buenos sistemas se adhieren a la regla de codificar solo datos nuevos: nunca diseñe una transacción de modo que requiera que los datos que ya están en un ordenador se vuelvan a introducir manualmente. En demasiadas fábricas, vemos a personas escribiendo datos como números de pieza mientras miran los números en los documentos generados por computadora.
Otro tipo de integración de datos une las bases de datos de fabricación con las de otras áreas funcionales. Lo más familiar es el vínculo entre ingeniería y fabricación que establecen los sistemas CAD/CAM, pero hay otros con igual o mayor impacto potencial. Una empresa, por ejemplo, está integrando su compleja red multiplanta con una red de entrada de pedidos y atención al cliente igualmente compleja para reducir los gastos generales, aumentar la velocidad y la eficacia de la entrega y mejorar la precisión de sus procesos de configuración y entrada de pedidos (una fuente importante de calidad). problemas). Otra empresa busca mejorar la eficiencia de su gran personal financiero vinculando su base de datos financieros con su base de datos de fabricación y así eliminar las entradas dobles y aumentar su capacidad de relacionar los planes de fabricación con el rendimiento financiero.
Un enfoque equilibrado
Por lo tanto, existen tres enfoques generales para gestionar los gastos generales de manera más eficaz: (1) analizar qué transacciones son necesarias y mejorar los métodos utilizados para llevarlas a cabo, (2) aumentar la estabilidad de las operaciones y (3) confiar en la automatización y la integración de sistemas. De los tres, los fabricantes estadounidenses parecen estar más enamorados del último.
Aplicada de forma selectiva, la automatización e integración de transacciones puede ser una herramienta importante para reducir los costes generales y aumentar la competitividad también en otras dimensiones. Sin embargo, en demasiados casos, esta herramienta tiene el efecto inverso. Los directivos suelen justificar este enfoque basándose en la sustitución del capital por mano de obra, pero a menudo olvidan que también están sustituyendo la mano de obra directa por gastos generales. Como se ha quejado un director de operaciones: «Todo lo que logramos hacer con nuestro nuevo y monstruoso sistema informático fue reemplazar$ Trabajadores de 10 por hora con$ 30-a-$ Técnicos de 50 horas a los que no podemos contratar de todos modos por su escasez». Según otro gerente de operaciones, «cuando automatizamos, los gastos de mano de obra directa se redujeron, pero los costos totales aumentaron debido al aumento de los gastos generales».
En muchos de estos casos, nadie se molestó en hacer un análisis completo del impacto en los volúmenes y costos de las transacciones a medida que las actividades pasaban a niveles de gestión intermedios. Algunas empresas incluso aplicaron sus viejas tasas de carga a los costes laborales directos proyectados después de la automatización.
Un segundo problema, y quizás más grave, se produce cuando los fabricantes automatizan transacciones que no son realmente necesarias en primer lugar. Una empresa que había construido recientemente una «fábrica del futuro» avanzada retiró posteriormente el sistema de vehículos guiados automatizados y una parte importante de los sistemas automáticos de almacenamiento y recuperación que había instalado para reducir el costo de sus transacciones logísticas internas. Después de la instalación, la empresa descubrió que había simplificado tanto el flujo de transacciones que, después de todo, no era necesaria ninguna automatización.
Otra empresa, mientras evaluaba un sistema de códigos de barras, descubrió recientemente que su justificación para el sistema desaparecía al eliminar el papeleo innecesario que había fluido entre la recepción, la inspección, la contabilidad y la producción. La proyección original había sido para una amortización de dos años en el sistema de códigos de barras (basada en la eliminación de los empleados administrativos necesarios para producir el papeleo), pero un examen más detenido mostró que la mayor parte de esa reducción administrativa vendría simplemente de eliminar las transacciones innecesarias.
La lección, entonces, es buscar un enfoque equilibrado para gestionar los gastos generales. La automatización no resuelve todos los problemas; de hecho, puede crear algunos a menos que se maneje con cuidado.
A medida que los gerentes estadounidenses se enfrentan a la tarea de controlar los gastos generales de fabricación, tendrán que ir más allá del análisis de procesos en su sentido habitual y aprender a analizar los procesos transaccionales. Los gerentes también tendrán que aprender cuándo y dónde automatizar el proceso de transacción, cómo integrarlo en la fabricación y en todas las funciones, y cómo y dónde estabilizar ese proceso para lograr su mayor efecto estratégico.
Por último, los gerentes de fabricación tendrán que ir más allá de las convenciones contables para analizar y categorizar los costos de forma que tengan un significado funcional. Creemos que la respuesta no radica únicamente en inventar nuevos sistemas contables. Este es un problema que deben resolver los contadores si pueden; sin duda ayudará si lo hacen. Pero ninguna magia contable permitirá a los gerentes de fabricación evitar una de las necesidades estratégicas del futuro: entender cómo gestionar la fábrica oculta.
1. Véase Steven C. Wheelwright y Robert H. Hayes, «Vincular el proceso de fabricación y los ciclos de vida de los productos», HBR enero-febrero de 1979, pág. 133, y «The Dynamics of Process-Product Life Cycles», HBR marzo-abril de 1979, pág. 127.
— Escrito por Jeffrey G. Miller Jeffrey G. Miller Thomas E. Vollmann