El globo: Cómo BMW está desactivando la bomba de tiempo demográfica
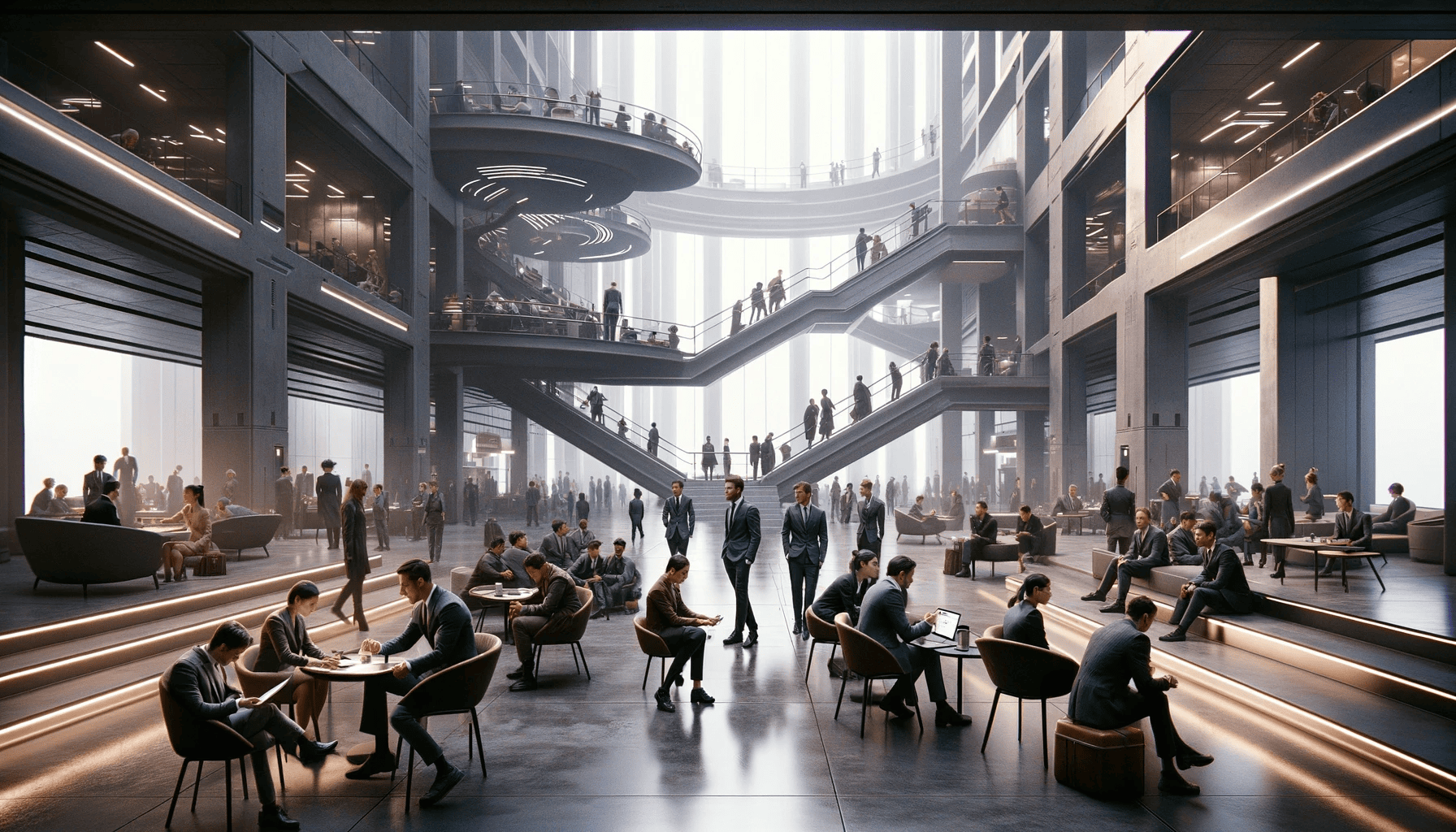
En junio de 2007, Nikolaus Bauer, jefe de la planta de tren de potencia de BMW de 2.500 empleados en Dingolfing, Baja Baviera, se preocupaba por lo que parecía una inevitable disminución de la productividad de una fuerza de trabajo envejecida en los años venideros. Con dos de sus directores de producción, Peter Jürschick y Helmut Mauermann (coautor, con Bauer), desarrolló un enfoque innovador y ascendente para mejorar la productividad que la compañía está probando y refinando en plantas de Estados Unidos, Alemania y Austria. El objetivo es incorporarlo a través de la organización mundial de fabricación de BMW.
El problema de BMW era que se esperaba que la edad promedio de los trabajadores de la planta aumentara de 39 a 47 en 2017. Debido a que los trabajadores de más edad tienden a llamar enfermos durante períodos más largos y, en general, deben esforzarse más para mantener su producción, soportar todo el peso del cambio demográfico amenazaría la capacidad de la planta para ejecutar la estrategia de BMW de mejorar la competitividad a través del liderazgo tecnológico y la productividad mejoras.
BMW no ha sido la única compañía con esta preocupación. Los líderes corporativos, políticos y economistas laborales de la mayoría de los países desarrollados están preocupados por las consecuencias del cambio demográfico en sus mercados laborales, que cada vez más consisten en trabajadores de más edad. En los Estados Unidos, por ejemplo, la población mayor de 65 años crecerá del 12,5% en 2000 al 16,6% en 2020 (las cifras correspondientes para Alemania son 16,4% y 21,6%, y para Japón 17,1% y 26,2%). Esta tendencia resultará costosa: en todo el mundo desarrollado, los costos de atención médica para una persona mayor de 65 años son aproximadamente tres veces más que los costos para alguien de entre 30 y 50 años.
Los enfoques tradicionales del problema incluyen despedir a los trabajadores de más edad o obligarlos a jubilarse anticipadamente. Pero esta no es una opción para empresas como BMW, que se ganan el compromiso de su fuerza laboral al ser empleadores confiables, y ciertamente no es una opción para toda una nación: Ola tras ola de jubilaciones anticipadas en los años 80 y 1990 aumentó la proporción de jubilados y ciudadanos trabajadores, haciendo que la financiación de jubilación más difícil. Otro enfoque consiste en trasladar a los trabajadores de más edad a empleos que son menos exigentes físicamente, pero esta no es una opción si no hay suficientes trabajadores jóvenes para ocupar su lugar. Tampoco es una solución a nivel nacional, en la que tal medida pueda interpretarse como discriminatoria. Para complicar el problema de BMW, la compañía era el mayor empleador en Baja Baviera, por lo que la decisión de despedir o reasignar a los trabajadores mayores tendría consecuencias políticas.
Veamos cómo Bauer y sus colegas resolvieron este aparente dilema.
La Línea
Para llegar a su solución, Jürschick y Mauermann eligieron una de las líneas de producción de la planta para un proyecto piloto. Los capataces de la línea, Günther Stadler y Kurt Dickert, le dieron personal con una mezcla de trabajadores del año 2017, es decir, trabajadores con una edad promedio de 47 años. (Ver la exposición «Una Línea de Producción Piloto».) A continuación, Stadler y Dickert trabajaron con las personas en línea, con el apoyo de altos directivos y expertos técnicos, para desarrollar cambios que mejoren la productividad, como la gestión de la atención sanitaria, la mejora de las capacidades de los trabajadores y el entorno laboral, e instituir políticas a tiempo parcial y procesos de gestión del cambio. La inversión directa en el proyecto de línea 2017 fue casi insignificante, aproximadamente 20.000 euros. Pero los 70 cambios aumentaron la productividad en un 7% en un año, situando la línea a la par de líneas en las que los trabajadores eran, en promedio, más jóvenes.
Una línea de producción piloto
En previsión de un aumento en la edad media de los trabajadores en una planta de BMW, una línea de producción piloto contaba con trabajadores con una edad media de 47 años, lo que representa una combinación de empleados del año 2017.
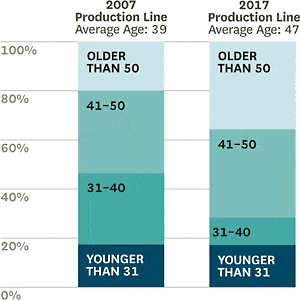
La línea, situada en el centro de la planta, producía cajas de cambio de eje trasero para automóviles de tamaño mediano y fue operada por 42 empleados. Esta línea relativamente pequeña fue una de las más intensivas en mano de obra en la fábrica. Empezó en 2003 con un volumen por turno de 440 cajas de cambios, que estaba previsto que subiría a 500 en 2008.
Hubo una fuerte resistencia inicial al proyecto, que rápidamente fue apodado la «línea de los pensionistas». Los trabajadores más jóvenes que ya estaban en la línea sentían que sufrirían una afluencia de personas menos productivas, mientras que los trabajadores mayores en otros lugares de la planta temían que serían mucho menos productivos si fueran sacados de sus zonas de confort y asignados a la línea piloto. Para muchos trabajadores, el proyecto parecía otra iniciativa de arriba hacia abajo que no les dejaba más remedio que adaptarse. Stadler y Dickert tenían preocupaciones propias, a saber, que BMW reduciría las tasas de velocidad de trabajo y los objetivos de rendimiento y degradaría los sistemas de IT en un esfuerzo por acomodar las deficiencias percibidas por los trabajadores de más edad.
Para encabezar la oposición, Jürschick y Mauermann consultaron al Consejo de Trabajadores de la planta. Esto resultó ser no sólo una política inteligente, sino también un movimiento práctico para el éxito del proyecto. El consejo remitió al equipo del proyecto a un estudio anterior sobre la productividad de los trabajadores en BMW que había identificado un marco básico para el cambio en cinco dimensiones: gestión de la salud, habilidades, entorno laboral, políticas de jubilación y procesos de cambio. El marco era teórico, pero dio al equipo ideas sobre los problemas que necesitarían abordar para mejorar la productividad de los trabajadores de más edad. También les permitió controlar el problema de productividad. El estudio había utilizado un cuestionario estándar, elÍndice de capacidad de trabajo (WAI), que evalúa y califica la adecuación entre la capacidad de un trabajador y las demandas de empleos específicos. El análisis de 100 combinaciones trabajador-trabajo en el departamento del eje trasero reveló que el promedio puntuación de productividad disminuyó con la edad, como se esperaba, pero el variación aumentó: algunos trabajadores siguieron siendo plenamente productivos, mientras que otros experimentaron un fuerte descenso. Gracias a estos hallazgos, Jürschick y Mauermann entraron en el proyecto entendiendo que la disminución de la productividad no es tan inevitable como el envejecimiento.
Stadler y Dickert, por su parte, mantuvieron muchas conversaciones individuales con los trabajadores, explicando que la línea piloto no sería una asignación flexible para los préritimes a tiempo parcial; estaría sujeta a los mismos estándares ambiciosos de productividad y calidad que otras líneas. También apelaron al orgullo de los trabajadores: «Necesitamos su experiencia y habilidades para lograr esto, y es importante para el futuro de esta planta. ¡Nuestros trabajos están en juego!»
Al final, el equipo del proyecto persuadió a 20 trabajadores que ya estaban en línea para que se quedaran y reclutó a 22 más, con la promesa de que podrían volver a sus antiguos puestos después de un año. En octubre de 2007, ambos turnos de la línea fueron atendidos con una mezcla de trabajadores que reflejaban la composición demográfica proyectada de la planta para 2017.
El proceso
El proyecto apoyó una iniciativa de concienciación sanitaria de toda la empresa. En noviembre de 2007, la empresa organizó una jornada informativa sobre nutrición personal y gestión sanitaria en la que participaron más de 10.000 trabajadores, de los 19.000 aproximadamente en todas las plantas de Dingolfing. Como parte de ello, el equipo del proyecto organizó un autodiagnóstico que otorgó puntos positivos para hábitos como ejercicio regular y puntos negativos para fumar o tener sobrepeso.
Stadler y Dickert organizaron talleres de lanzamiento para el proyecto, durante los cuales pidieron a los trabajadores que describieran sus dolores y dolores y lo que cambiarían en la línea. Estos talleres impulsaron a los trabajadores a hacerse cargo de su bienestar y del proyecto. Cada idea planteada fue tomada en serio, por lo que los empleados se sentían lo suficientemente seguros como para lluvia de ideas libremente. El equipo animó a los trabajadores a escribir sus ideas en tarjetas y a ponerlas en un tablero. La gente apreciaba esta forma de comunicarse. Un empleado comentó: «Las viejas formas del programa de mejora continua requerían mucha escritura. Completar estos formularios me mató. Solía ser granjero. Escribir las cosas es difícil para mí».
Cada trabajador recibió un «presupuesto» de cinco puntos para asignar entre las ideas, un proceso simple que dio lugar a una lista de acciones prioritarias para el equipo del proyecto. «Ninguna de las ideas vino de arriba», dice Mauermann. «Los gerentes y capataces deliberadamente abandonaron el control: Nos abstuvimos de evaluar, criticar o rechazar ideas individuales. A los empleados se les ocurrió su propia clasificación».
La voluntad de la dirección de implementar rápidamente ideas aumentó aún más la aceptación entre los trabajadores. Un capataz comentó: «La generación de ideas realmente despegó cuando una estación de trabajo tiene un piso de madera. Las personas de las líneas vecinas se rieron al principio, pero después de solo un día se hizo evidente que ayudaba. Al final del día, tus rodillas no estaban doloridas. Esto mostró que el proyecto de 2017 podría tener sentido».
Después de esto, los trabajadores se hicieron cargo, y el equipo del proyecto se centró en la ejecución de sus ideas. El equipo pidió apoyo a un ergonomista, un oficial de seguridad e ingenieros de procesos, pero los trabajadores hicieron la mayor parte del trabajo ellos mismos, algunos de ellos en su propio tiempo. Se enorgullecían cada vez más de su participación en el proceso.
Los cambios
Muchas de las ideas implementadas en la línea 2017 fueron cambios físicos en el lugar de trabajo que reducirían el desgaste en el cuerpo de los trabajadores y, por lo tanto, la probabilidad de que los trabajadores llamaran enfermos. El nuevo suelo de madera junto con el calzado adaptado al peso, por ejemplo, reducen la tensión de las articulaciones y la exposición a sacudidas eléctricas estáticas. Los trabajadores de la línea también instalaron sillas especiales en varias estaciones de trabajo, lo que les permitió trabajar sentados o relajarse durante períodos cortos durante los descansos. El primer modelo que trajeron fue una silla de peluquería. Después de probarlo, los trabajadores, con la ayuda de un ingeniero, mejoraron la forma y composición de la silla, reemplazando su cubierta de plástico, que causaba sudoración y rozaduras, por una de cuero. A continuación, se desarrollaron nuevos asientos con un fabricante de sillas por un coste total de menos de 1.000€.
Algunas de las medidas se referían tanto a cuestiones de ergonomía como a la calidad. La instalación de mesas verticalmente ajustables permitió adaptar las estaciones de trabajo a la altura de cada trabajador, lo que redujo la tensión de espalda. También facilitó la rotación de puestos de trabajo durante un turno, ya que las tablas podían ajustarse rápidamente para adaptarse a los trabajadores entrantes. Del mismo modo, la instalación de lentes de aumento flexibles ayudó a los trabajadores a distinguir entre piezas pequeñas, reduciendo la fatiga visual y los errores. En total, la línea implementó 70 pequeños cambios en el diseño y el equipamiento que mejoraron la ergonomía en varias estaciones de trabajo. (Para ejemplos de algunos de los cambios y su costo, ver la exposición «2017 Ergonomía»).
2017 Ergonomía
Los trabajadores de la línea de producción 2017 hicieron 70 cambios en los equipos de trabajo que redujeron la tensión física y las posibilidades de error. El coste total fue de 40.000 euros y algunas horas de tiempo de mantenimiento. Entre los ejemplos se incluyen:
Suelo de madera
Coste <5.000 €
Reduce la tensión de la rodilla y la exposición a la sacudida de electricidad estática
Sillas de barbería
Coste <1.000 €
Permitir descansos cortos y tensión física alterna (los trabajadores pueden pararse o sentarse)
Calzado ortopédico
Costo <2.000 €
Reduce la tensión en los pies
Monitores en ángulo
Sin costo
Reducir la fatiga visual
Hecho en dos horas de tiempo de mantenimiento
Lentes de aumento
Coste <1.000 €
Reduzca la fatiga visual y minimice los errores de clasificación
Mesas de trabajo ajustables
Sin costo
Alivia la tensión física y facilita la rotación del personal durante los turnos
Se realiza por mantenimiento dentro de las horas normales
Herramientas de agarre de mango grande
Sin costo
Reduce la tensión en los brazos
Proyecto con estudiantes universitarios
Contenedores de transporte apilables
Sin costo
Alivia la tensión física y facilita la rotación del personal durante los turnos
Modificación de contenedores ya desarrollados para la introducción de un nuevo producto
Tipo de letra más grande en pantallas de ordenador
Sin costo
Reduzca la fatiga visual y minimice los errores de clasificación
Hecho por personal de mantenimiento durante horas normales
Grúas de elevación manual
Coste <1.000 €
Reduce la tensión en la espalda
Coste total de grúas compartidas con la universidad para apoyar una tesis de maestría
Los cambios en el diseño y el equipo se complementaron con cambios en las prácticas de trabajo. La línea introdujo la rotación de puestos de trabajo en las estaciones de trabajo durante un turno para equilibrar la carga sobre el cuerpo de los trabajadores. (Ver la exposición «Rotación ergonómica óptima del trabajo»). Hubo cierta resistencia inicial. Un trabajador comentó: «Estaba en contra. Siempre piensas que la persona que te precede en la máquina no hace un trabajo tan bueno como puedas. Pero rápidamente vimos que el tiempo pasa más rápido, vemos mejor cómo trabajan las personas que nos rodean, y podemos ayudarnos mutuamente».
Rotación ergonómica óptima del trabajo
Como parte de un esfuerzo por mantener la productividad de los trabajadores mayores en una línea de producción de BMW, la dirección analizó el grado de tensión física experimentada en varias estaciones de trabajo. A involucró cepa leve o moderada, B fue la más exigente físicamente y C fue la menor. Se decidió que los trabajadores podían permanecer en el puesto de trabajo A durante todo un turno, pero que debían girar entre B y C para reducir la posibilidad de lesiones.
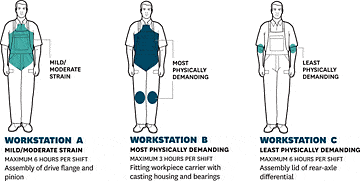
Estación de trabajo/tensión moderadaMáximo 6 horas por turnoMontaje de brida de accionamiento y piñonEstación de trabajo BMás exigenciaMáximo 3 horas por turnoSoporte para piezas de trabajo Montaje con carcasa de fundición y rodamientos de la estación de trabajo Limpieza físicaMáximo 6 horas por turnoTapa de montaje del eje trasero diferencial
Haga clic aquí para obtener una imagen más grande del gráfico.
Además, un fisioterapeuta desarrolló ejercicios de fuerza y estiramiento, que hizo con los trabajadores todos los días durante las primeras semanas. Esto provocó algunas burlas de las otras líneas, por lo que muchos en la línea de 2017 se mostraron reacios a realizar los ejercicios. El avance llegó cuando Stadler reclutó a un voluntario del grupo, que recogió a sus colegas al comienzo de los descansos y realizó los ejercicios con ellos.
Los resultados
Como se ha señalado anteriormente, la inversión de capital para el proyecto de línea 2017 ascendió a unos 20.000 euros, lo que incluía el tiempo empleado por el ergonomista y fisioterapeuta, así como Bauer, Jürschick y Mauermann. Los salarios que cubren la asistencia a los talleres ascendieron a casi 20.000 euros, lo que eleva los costos globales a unos 40.000 euros.
¿Qué consiguió BMW a cambio? La línea logró una mejora de productividad del 7% en un año, igualando la productividad de las líneas atendidas por trabajadores más jóvenes. La producción objetivo de la línea se incrementó a 500 unidades por turno a mediados de 2008 y a 530 unidades por turno en febrero de 2009, de acuerdo con los ambiciosos objetivos de la planta. Después del aumento de la productividad, cuatro trabajadores fueron reasignados a otras líneas, pero nadie, incluidos los escépticos iniciales, quiso irse. El objetivo de 10 defectos por millón de calidad se alcanzó después de tres meses. El rendimiento actual se encuentra en cero defectos. El ausentismo relacionado con la licencia por enfermedad, la licencia de maternidad, la atención preventiva de la salud y la rehabilitación se situó en un 7% durante el año 2008, más alto que en otros lugares de la planta, pero típico de esta mezcla de trabajadores mayores. En junio de 2009, el ausentismo había descendido al 2%, por debajo de la media de la planta.
BMW ahora promociona la línea 2017 como un modelo de productividad y alta calidad en sus comunicaciones internas. Se establecieron proyectos de seguimiento en Leipzig (Alemania) y Steyr (Austria), en la planta final de montaje de automóviles al otro lado de Dingolfing, y en la planta estadounidense. A medida que BMW ha implementado este enfoque, se ha asegurado de abordar las condiciones específicas de los lugares de trabajo implicados, mientras que transfiere el enfoque dirigido por los trabajadores para identificar y aplicar cambios. Los números precisos son confidenciales, pero estas pruebas extendidas muestran resultados similares a los de Dingolfing.
El proyecto de línea 2017 es un caso notable de resolución de problemas organizacionales distribuidos. La alta dirección de la planta planteó el problema, los gerentes de producción realizaron un experimento y los trabajadores de línea crearon las soluciones. Es un enfoque que se convertirá en una capacidad crítica para las empresas globales. La introducción y ampliación de las tecnologías medioambientales y la penetración de nuevos mercados en Asia son desafíos similares a los que Nikolaus Bauer enfrentó: los gerentes pueden articular el problema y elegir entre soluciones, pero no son necesariamente una buena fuente de soluciones. Para que surjan, los empleados de primera línea necesitan la libertad de experimentar. A medida que las empresas se enfrentan a los desafíos estratégicos futuros, la capacidad intelectual de su fuerza laboral puede ser el factor diferenciador más importante.
— Escrito por Christoph Loch, Nikolaus Bauer, Helmut Mauermann Nikolaus Bauer,