Defectos del producto y productividad
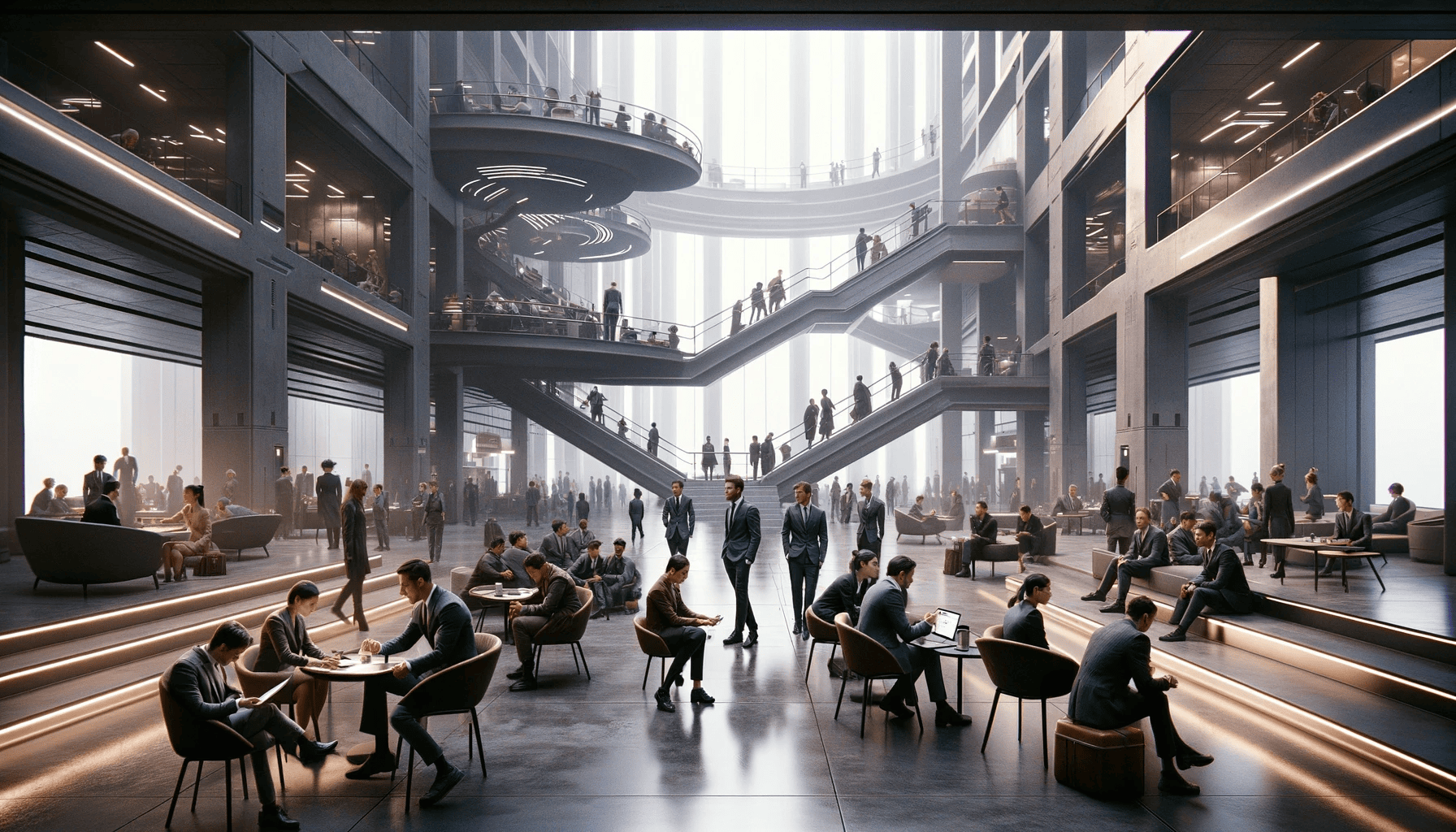
Muchas personas de este lado del océano han saludado con un bostezo el alboroto sobre los milagrosos logros de Japón en la industria manufacturera durante la última década. «Entonces, ¿qué más hay de nuevo?» dicen. «Deming dijo esto hace años». W. Edwards Deming es el padrino, si no el verdadero padre, de la productividad de las plantas. Fue el principal responsable de instituir en las plantas los procedimientos de control estadístico que los japoneses han adoptado con tanta deduza. En este artículo se describe el enfoque de Deming respecto a la productividad y la calidad: dado que solo la gerencia tiene autoridad para cambiar el sistema de producción para eliminarlos, los defectos de los productos son responsabilidad de la gerencia.
Para cambiar el sistema, la administración primero debe distinguir la variación anormal de la normal. También necesita especificar operativamente lo que se supone que debe producir el sistema. Con estos controles en mano, la organización puede predecir el rendimiento, los costos y los niveles de calidad, y los gerentes pueden comunicarse eficazmente con los clientes y las personas del taller. Y esto es muy importante, porque cuando la dirección ve al sistema y no a los trabajadores como la causa de los problemas, muchos de los resultados que menostran la moral de las malas decisiones, objetivos en los que nadie cree y desaparecen consignas motivadoras que culpan implícitamente a los trabajadores.
John Henry, presidente de Global Manufacturing Company, se recostó en su silla, suspiró y miró al techo. En el escritorio frente a él había un informe de dos estadísticos sobre los problemas de productividad y calidad en la fábrica Nightingale de Global.
Henry y sus vicepresidentes sabían que las cosas iban mal. Los clientes se quejaban, los precios eran demasiado altos, las cuentas por cobrar aumentaban, las llamadas de reparación aumentaban, los costos subían, la moral de los trabajadores bajaba y el sindicato amenazaba con hacer huelga debido a las incesantes demandas de la dirección de mejorar la productividad. Además, la mayoría de las máquinas no estaban a la altura del trabajo. Pero no habían negociado, pensó Henry con desgracia, sobre lo que encontrarían los estadísticos. Recogió el informe, suspiró en otra ocasión y lo volvió a mirar.
«Su fábrica en Nightingale», dice el informe, «funciona día tras día enviando artículos, 15% de los cuales (en promedio) tienen uno o más defectos importantes... Esta proporción de defectos importantes en tu producto puede explicar algunos de tus problemas con las ventas y los beneficios. La cantidad de retrabajo que tienen que hacer sus operadores a lo largo de la línea de producción también está sofocando sus ganancias.
«Tus problemas empiezan así. Un operador en la línea resulta un artículo. Ella lo mira por encima. Si encuentra un defecto importante, puede volver a trabajarlo ella misma porque sabe que de lo contrario podría volver a ella más tarde para solucionarlo. Pero, ella piensa, el inspector de la línea podría no detectar ese defecto. Si lo hace, puede volver a trabajarlo o enviarlo de vuelta al operador. Pero incluso si el inspector lo ve, el supervisor puede interceptar el artículo en su camino de regreso al operador y enviarlo a través de la producción para evitar que se quede corto en una etapa posterior de la línea.
«Desde el punto de vista del operador, ¿por qué no arriesgarse con defectos menores y mayores? Mándalos por la línea; lo más probable es que no vuelvan. Desde el punto de vista del inspector, el supervisor puede intervenir, por lo que corregir los defectos puede ser una pérdida de tiempo. Desde el punto de vista de la supervisora, puede arriesgarse al defecto. No puede perder, y podría ganar si mantiene su récord de producción alto.
«En otras palabras, Sr. Henry, el trabajo de su operador es producir defectos. Le pagan por ellos. Este es el sistema y el operador no es responsable de ello. La administración lo es».
El punto detrás del memorando de los estadísticos al pobre John Henry es que los defectos no son gratuitos: alguien hace defectos y se le paga por hacerlos. Si una proporción sustancial de la fuerza de trabajo corrige los defectos, entonces la empresa está pagando para corregir los defectos así como para hacerlos. Si la fábrica de Nightingale está produciendo 15% productos defectuosos, luego 15% del coste total se gasta en fabricar unidades defectuosos. Obviamente, la baja calidad significa un alto costo.
Todos los problemas de Henry y sus vicepresidentes surgieron de la mala gestión de la calidad. En otras palabras, y este podría ser el segundo punto de los estadísticos, la dirección consigue un producto de alta calidad mejorando el proceso. Si los gerentes pueden mejorar el proceso de fabricación, pueden transferir recursos de la producción de defectuosos a la fabricación de productos buenos adicionales.
Supongamos que la gerencia de Nightingale es capaz de mejorar el proceso realizando algunos cambios sin costo adicional, de modo que solo 9% de la salida es defectuosa. ¿Qué ha logrado la dirección?
1. La productividad ha aumentado. La fábrica ahora produce 6% más unidades al mismo coste. (Si la fábrica retrabaja los defectos, los operadores pueden aprovechar el tiempo que hubieran tardado en volver a trabajar los 6% defectuosos para hacer más buen producto. Esto crea un aumento adicional (gratuito) de la productividad).
2. La calidad de los agregados ha mejorado. Ahora solo 9% de la salida es defectuosa en lugar de 15%.
3. La capacidad ha aumentado. La fábrica produce 6% más unidades buenas con el mismo sistema: mano de obra, máquinas, materiales,.
4. El coste por unidad es menor. La fábrica fabrica más unidades al mismo costo.
5. El precio se puede reducir.
Se puede ver que el control de procesos (es decir, la gestión adecuada de la calidad) puede aliviar los problemas de John Henry. Con una mejor calidad, los clientes dejarán de quejarse y las devoluciones disminuirán, el personal de ventas podrá competir eficazmente debido a un producto de mayor calidad y un precio más bajo, las llamadas de servicio y reparación disminuirán, las cuentas por cobrar bajarán (porque es probable que los clientes satisfechos paguen sus facturas), los costos disminuirán, la productividad aumentará, el sindicato dejará de amenazar con hacer huelga y la dirección tendrá capital para mantener el equipo adecuadamente.
Mejorar el proceso es clave para aumentar la productividad y la calidad y reducir los costes unitarios. Los gerentes pueden alcanzar estos objetivos mediante la comprensión de las fuentes de variación de un proceso y utilizando las definiciones operativas adecuadas.
Las fuentes de variación
Veamos un proceso de fabricación que produce varillas de acero. Aunque el diámetro promedio de las varillas es de 2 pulgadas, no podemos esperar que el diámetro de cada caña sea exactamente eso. Esperaríamos algunas variaciones dependiendo de cómo se redondeó la medición.
La variación en un proceso es natural. De hecho, todos deberíamos esperarlo y no sorprendernos cuando ocurra. Pero los procesos están sujetos a dos fuentes de variación: normal y anormal. La variación anormal se debe a una causa especial o específica y puede estar presente o no en un proceso. En nuestro ejemplo, digamos que producimos una varilla con un diámetro de 1,96 pulgadas. ¿La discrepancia de 0,04 pulgadas es una variación anormal en el proceso? ¿O es una variación normal que deberíamos esperar? Si se trata de una variación anormal, nos gustaría intervenir y, digamos, ajustar una máquina. Si no lo es, no debemos intervenir. De hecho, al ajustar la máquina sin causa, corremos el riesgo de perder el proceso.
Algunos investigadores estiman que las variaciones anormales causan 15% de los problemas de un proceso, mientras que las variaciones normales provocan el 85 restante%.1 Las variaciones normales son comunes a todos los elementos de un proceso (un grupo completo de trabajadores, un departamento completo e incluso toda una empresa) y generan la mayoría de los altos costos de producción y servicio y los problemas de bajo rendimiento. La confusión entre las causas comunes y las causas especiales de variación genera frustración en todos los niveles, más variación y costos más elevados. Al no poder distinguir entre las dos fuentes de variación, la dirección puede reaccionar culpando a los trabajadores.
Un trabajador es impotente para actuar sobre una causa normal de variación. Los trabajadores no tienen autoridad para afinar las definiciones y las pruebas que determinan la calidad aceptable. No pueden hacer mucho con las máquinas o los equipos de prueba que están fuera de servicio. Pueden informar de tales eventos, pero la dirección debe hacer el seguimiento y hacer los cambios necesarios. Los trabajadores tampoco pueden cambiar las especificaciones ni la política de adquieren los materiales entrantes y no son responsables del diseño del producto. Todos ellos forman parte del sistema y solo los administradores pueden cambiar el sistema.
Es difícil sobrestimar cuán alta sería la moral en la mayoría de las fábricas si la dirección responsabilizara a los trabajadores solo de lo que podían controlar y no de las desventajas del sistema.
¿Qué tipo de variación es?
Debido a que los trabajadores no pueden ser responsables del sistema, los gerentes deben poder distinguir entre variaciones anormales y normales para que sepan cuándo y cómo cambiar el proceso. La única forma segura de diferenciar las dos fuentes de variación en un proceso es a través de las señales estadísticas que generan los gráficos de control.
Cartas de control
Un gráfico de control del sistema tiene una línea central que representa el promedio del proceso y dos límites de control, superior e inferior. Supongamos que desea examinar la operación de pulsación de teclas en un departamento de procesamiento de datos. Primero, de acuerdo con la teoría estadística, se determina el tamaño de la muestra, digamos 200 tarjetas por día.2 Luego, tomas muestras aleatorias de 200 tarjetas de la salida de cada día y las inspeccionas en busca de errores. El Anexo I muestra cómo construir un gráfico de control para una operación de pulsación de teclas.
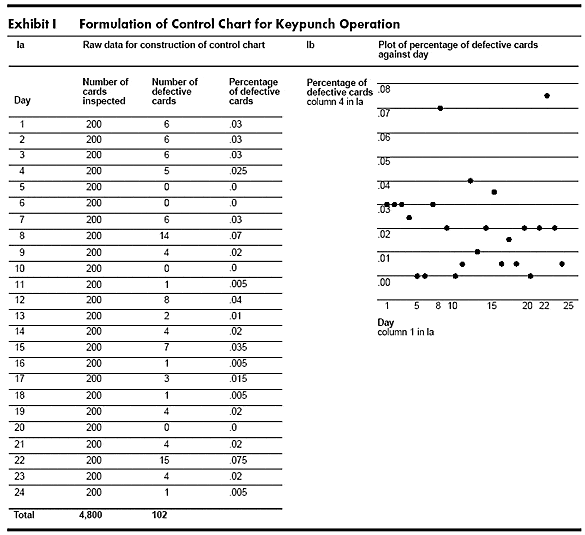
Anexo I Formulación de la tabla de control para la operación de punzonado Nota: Los dos puntos (día 8 y día 22) que se encuentran por encima del UCL envían una señal estadística a la gerencia para buscar posibles fuentes de variación anormal el día 8 y el día 22.

Prueba Ia muestra el porcentaje de tarjetas perforadas que están defectuosas. Exposición Ib es un gráfico de «porcentaje defectuoso» (columna 4 de Ia) frente a «día» (columna 1 de Ia). Exposición Ic muestra los cálculos que necesitará para construir la línea central (en este ejemplo, el porcentaje medio defectuoso del proceso) y los límites de control superior e inferior.
Construyes el gráfico de control(ID de prueba) conectando los puntos trazados en Ib y dibujando la línea central y los límites de control superior e inferior a través de los puntos. Por último, se analiza el gráfico de control. Si el valor de una muestra se encuentra dentro de los límites de control superior e inferior, y si no existe una tendencia u otro patrón sistemático, es probable que la variación sea normal. Sin embargo, si el valor de una muestra queda fuera de los límites de control, es probable que la variación sea anormal.
El gráfico que se muestra en el Anexo I es solo uno de los muchos tipos de gráficos de control, cada uno de los cuales tiene un propósito especial. (Puede encontrar ejemplos de otros gráficos en las fuentes enumeradas al final del artículo).
Si la variación es anormal
Al comparar Ib e Id, el lector verá lo difícil que es diferenciar a simple vista entre las dos causas de variación. La prueba Ib no permite a los gerentes distinguir entre las dos fuentes de variación, mientras que la prueba Id muestra claramente que en los días 8 y 22 ocurrió algo anormal, no atribuible al sistema, que provocó que las tarjetas defectuosas se perforaran.
Cuando un gerente determina que la causa de la variación es anormal, debe buscar y eliminar las causas atribuibles a un trabajador o grupo de trabajadores específicos, a una máquina, a un nuevo lote de materias primas,. Una vez que la administración elimina todas las causas asignables de variación, queda con un proceso estable que está bajo control estadístico.
Reexaminemos la operación de pulsación de teclas mostrada en el Anexo I con más detalle. Observe el gráfico de control para ver el porcentaje de tarjetas con errores (ID).
Es habitual basar los límites de control en un múltiplo del error estándar. Por lo general, este múltiplo es 3 y los límites se denominan límites de 3 sigmas. Esto significa que hay aproximadamente 3 posibilidades en 1.000 de que la ubicación de un punto fuera de los límites se deba a la variación aleatoria natural del sistema. Si observamos los gráficos de las pruebas I y II podemos ver que dos puntos están fuera del límite superior de control, lo que indica que el proceso no está bajo control estadístico.
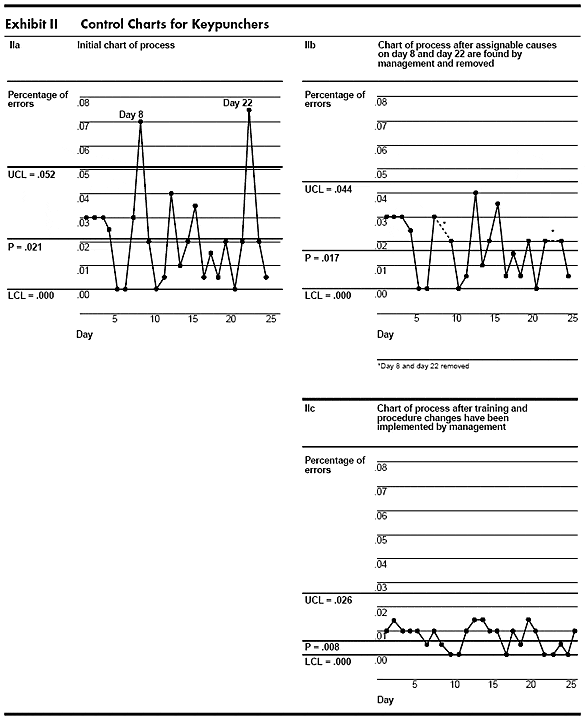
Gráficas de control del Anexo II para teclados
¿Cuál debería ser el próximo paso de la dirección? Para controlar el proceso, la gerencia debe investigar los puntos que estaban fuera de control para eliminar las causas asignables de variación del proceso. Supongamos que la dirección descubrió que el día 8 se había añadido un nuevo operador de punzonado a la fuerza de trabajo, y que el día que tardó el trabajador en aclimatarse al nuevo entorno probablemente causó el número inusualmente alto de errores de pulsación de teclas. Para garantizar que esta causa asignable no se repita, la empresa instituyó un programa de formación de un día.
La investigación del día 22 mostró que la noche anterior, el departamento se había quedado sin tarjetas del vendedor habitual y no esperaba un nuevo envío hasta la mañana del día 23. En consecuencia, el departamento compró tarjetas para un día de un nuevo proveedor. La gerencia descubrió que estas tarjetas eran de calidad inferior, lo que provocó el gran número de errores de pulsación de teclas. Para corregir esta variación asignable, la dirección instituyó una política de inventario revisada y definió operativamente la calidad aceptable para las tarjetas perforadas.
Tras eliminar los días para los que se encontraron las causas asignables de variación, los gerentes volvieron a calcular las estadísticas de la gráfica de control:
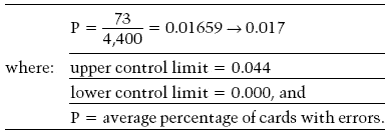
Prueba IIb muestra el gráfico de control revisado (IIa muestra el gráfico original). El proceso ahora es estable, en control estadístico.
Un proceso estable que solo presenta variaciones debido a limitaciones inherentes al sistema permite al gerente determinar su capacidad, es decir, qué es normal. Estas son algunas de las ventajas de lograr un proceso estable:
1. La administración conoce la capacidad del proceso y puede predecir su rendimiento, costos y niveles de calidad.
2. Con el sistema actual, la productividad es máxima y los costes mínimos.
3. La administración puede medir los efectos de los cambios en el sistema con mayor rapidez y fiabilidad.
4. Si la administración desea modificar los límites de especificación, tiene datos para respaldar su argumento.
La capacidad del proceso se convierte en un hecho. Un proceso estable que produce un número inaceptable de defectos seguirá haciéndolo mientras el sistema, tal como se define actualmente, siga siendo el mismo. Y solo la gerencia se encarga de cambiar el sistema.
Variación normal
Una vez que un proceso alcanza la estabilidad, que no es un estado natural sino un logro, la dirección está lista para actuar sobre el sistema para mejorar la productividad y la calidad. Los gerentes pueden mejorar el sistema mediante:
1. Cambiando el promedio del proceso. Por ejemplo, es posible que la dirección desee reducir el porcentaje de defectos o aumentar la producción media.
2. Cambiar la cantidad de variación. Dadas las demandas económicas del mercado, la dirección puede querer reducir la cantidad de variación para obtener un producto más uniforme o aumentarlo para obtener un producto menos uniforme.
Ciertos insumos y procedimientos, tales como mano de obra, capacitación, supervisión, materias primas, máquinas y definiciones operativas, definen el sistema. Para mejorar el sistema, la administración debe modificar estos factores. Una vez más, recalcamos que solo la gerencia tiene la responsabilidad y la autoridad para realizar estos cambios. Los trabajadores por sí solos no pueden afectar al sistema.
¿Cómo puede la gerencia cambiar el proceso de perforación de teclas para mejorar la productividad y la calidad? Al establecer procedimientos de formación que reducen el porcentaje medio de tarjetas defectuosas y la cantidad de variaciones comunes (lo que se traduce en límites de control más estrechos), la dirección puede ayudar a los empleados a producir tarjetas más libres de errores de forma coherente.
Prueba IIc muestra el nuevo cuadro de control después de la formación instituida por la dirección y los cambios de procedimiento. El porcentaje medio de tarjetas perforadas con errores ha disminuido de 0,017 a 0,008 y la variación del proceso también ha disminuido.
Es importante destacar que los conceptos que hemos discutido abarcan algo más que gráficos de control. Las empresas pueden utilizar gráficos de control sin comprender el enfoque que nos preocupa, es decir, la responsabilidad de la dirección de mejorar el sistema, no depender habitualmente de la inspección final, eliminar eslóganes, eliminar normas de trabajo arbitrarias,.
Hemos cerrado el círculo. Sabemos que mejorar el proceso aumenta la productividad y la calidad. Al distinguir entre variación anormal y normal, y al eliminar la variación anormal, los gerentes pueden obtener un control estadístico. Pero esto por sí solo no es suficiente para mejorar la productividad y la calidad.
Si la gerencia comprendiera plenamente las fuentes de variación y viera que su responsabilidad es mejorar el proceso, pero no entendiera las definiciones operativas, sus esfuerzos seguirían siendo en vano.
¿Qué se está produciendo?
Si la dirección no puede definir con precisión sus productos, ¿cómo puede venderlos, describir lo que quiere a la gente en el taller o mejorar el proceso de producción? No puede. Sin una definición operativa, la gente no puede hacer negocios. He aquí un ejemplo de la confusión que puede causar la ausencia de una idea precisa de lo que se está produciendo:
«La etiqueta de una manta dice '50% lana.» ¿Qué significa esto? ¿Media lana, en promedio, sobre esta manta, o mitad lana durante un mes de producción? ¿Qué es la mitad lana? ¿Mitad de peso? Si es así, ¿a qué humedad? ¿Por qué método de análisis químico? ¿Cuántos análisis? ¿La mitad inferior de la manta de lana y la mitad superior son otra cosa? ¿Es 50?% lana? ¿Significa el 50% de lana que debe haber lana en cualquier sección transversal aleatoria del tamaño de medio dólar? Si es así, ¿cuántos cortes se deben analizar? ¿Cómo los seleccionas? ¿Qué criterio debe cumplir la media? ¿Y cuánta variación entre cortes es permisible? Obviamente, el significado de 50% lana solo se puede declarar en términos estadísticos».3
¿Qué es una definición exacta o verdadera de un término? Por ejemplo, ¿qué es «exactamente redondo»? No existe una definición que nos ayude a saber si algo es redondo. El diccionario tampoco sirve de nada. Webster's dice que una figura es redonda si tiene «todas las partes de la superficie o circunferencia equidistantes del centro». Esta definición es muy útil para la lógica formal, pero si tratamos de usarla para determinar si nuestro disco es redondo, tendremos dificultades insuperables. El diccionario proporciona un concepto, no una definición para su uso en la industria.
¿Cómo podemos definir un término comprensible a nivel de tienda? Las definiciones operativas son de dos tipos: una para atributos, por ejemplo, éxito frente a fracaso, y otra para variables, por ejemplo, volumen de ventas. La definición operativa de un atributo consiste en:
1. Criterio que se aplica a un objeto o grupo.
2. Procedimiento para seleccionar el objeto objeto de estudio.
3. Operación, como medir u observar el objeto.
4. Un registro del resultado.
5. Prueba del objeto para decidir si se ajusta al criterio.
6. Una decisión afirmativa o no sobre si el objeto cumple el criterio.
Para derivar una definición operativa de una variable, los gerentes tomarían los mismos cuatro primeros pasos que dieron para obtener una definición de atributo. (Los pasos 5 y 6 de los atributos no se aplican a las variables).
Ahora bien, la pregunta es: ¿Cuál es la importancia de las definiciones operativas para la productividad de una empresa? Sabemos lo importante que es que los productores y los usuarios se entiendan entre sí. Sin definiciones operativas, una especificación carece de sentido. El conflicto y la confusión entre las empresas y entre los departamentos de una empresa surgen de la incapacidad de los gerentes de indicar de antemano, en términos significativos, las especificaciones de un artículo o su desempeño. Piense en los problemas de productividad y calidad que pueden surgir cuando un inspector responsable de encontrar defectos es inconsistente con el tiempo en sus juicios o cuando los inspectores son incoherentes entre sí. Los trabajadores no saben qué es aceptable o qué es defectuoso. Necesitan una definición operativa de un producto defectuoso.
Supongamos que fabricamos discos redondos. ¿Son redondos los discos? ¿Por qué nos importa? Si un disco está demasiado lejos de ser redondo, atascará la máquina del cliente, causará daños en el equipo y provocará tiempo de inactividad. Si queremos seguir en el negocio, es mejor que nos cuiden.
Vamos a escribir una definición operativa de round para el disco. Dado que estamos midiendo un atributo (redondo frente a no redondo), trabajaremos en el primer tipo de definición operativa.
Paso 1: En primer lugar queremos derivar un criterio para el objeto.
a. «Utilice pinzas que estén razonablemente en buen estado». (Percibes de inmediato la necesidad de cuestionar cada palabra).
«¿Qué es un 'orden razonablemente correcto'?» (Nosotros resolvemos la pregunta dejándote usar tus pinzas).
«Pero, ¿cómo debo usarlas?»
«Estaremos satisfechos si los usas de la forma habitual».
«¿A qué temperatura?»
«La temperatura de esta habitación».
b. «Tome 6 medidas del diámetro a unos 30 grados de distancia. Registra los resultados».
«Pero, ¿qué es 'a unos 30 grados de separación'? ¿No quieres decir exactamente 30 grados?»
«No, no existen exactamente 30 grados en el mundo físico. Así que prueba 30 grados; estaremos satisfechos».
c. Si el rango entre los 6 diámetros no supera los 0,007 centímetros, declararemos que el disco es redondo. Hemos determinado el criterio.
Paso 2: Vamos a seleccionar un disco en particular. (En este momento podríamos especificar algún esquema de muestreo).
Pasos 3 y 4: Toma las medidas y registra los resultados en centímetros: 3,365, 3,363, 3,368, 3,366, 3,366 y 3,369.
Paso 5: El rango es de 3,369 a 3,363, o una diferencia de 0,006. Comprobamos la conformidad comparando el rango de 0,006 con el rango de criterios inferior o igual a 0,007 (del paso 1).
Paso 6: Debido a que el disco pasó la prueba de redondez prescrita, declaramos que es redondo.
Si una empresa tiene trabajadores que entienden lo que significa la ronda y un cliente que está de acuerdo, los problemas que la empresa pudo haber tenido para satisfacer al cliente desaparecerán.
Veamos otro ejemplo en el que las definiciones operativas mejoran la comprensión dentro de la empresa. En este ejemplo medimos una variable (ventas), por lo que usamos el segundo tipo de definición operativa.
A una vendedora se le dice que su desempeño será juzgado con respecto al porcentaje de cambio en las ventas de este año con respecto a las ventas del año pasado. ¿Qué significa esto? ¿Cambio porcentual medio cada mes? ¿Cada semana? ¿Cada día? ¿Para cada producto? ¿Variación porcentual entre las ventas del 31 de diciembre de 1980 y el 31 de diciembre de 1981?
¿Cómo medimos las ventas: bruto, neto, beneficio bruto, beneficio neto, etc.? ¿El cambio porcentual es en dólares constantes o inflados? Si está en dólares constantes, ¿cuál es el año base? Si está en dólares inflados, ¿está a precios del año pasado o de este año? ¿En qué condiciones económicas?
Una definición poco precisa de cambio porcentual solo puede generar confusión, frustración y mala voluntad entre la dirección y la fuerza de ventas; no es la forma de mejorar la productividad. ¿Cómo debe definir operativamente la gerencia un cambio porcentual en las ventas?
Paso 1: Un cambio porcentual en las ventas es la diferencia entre las ventas de 1981 (del 1 de enero de 1981 al 31 de diciembre de 1981) y las ventas de 1980 (del 1 de enero de 1980 al 31 de diciembre de 1980) divididas por las ventas de 1980:
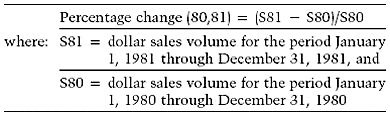
El S80 se mide en dólares constantes, con 1979 como año base, utilizando los precios del 15 de junio de 1979 y el 15 de junio de 1980 para obtener los precios constantes en dólares, y las ventas unitarias totales menos los rendimientos (por cualquier causa) al 31 de diciembre de 1980 para cada producto.
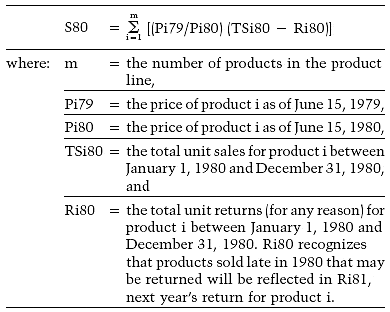
El S81 se mide en dólares constantes, con 1979 como año base, utilizando los precios del 15 de junio de 1979 y el 15 de junio de 1981 para obtener los precios constantes en dólares, y las ventas unitarias totales menos los rendimientos (por cualquier motivo) al 31 de diciembre de 1981 para cada producto. (Pi79 sigue siendo el mismo para todos los productos).
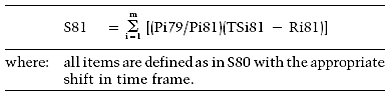
Este procedimiento para calcular el cambio porcentual de las ventas entre 1980 y 1981 entrará en vigor independientemente de las condiciones económicas. Además, la dirección puede revisar la definición de un cambio porcentual en las ventas después de la evaluación de ventas de 1985, pero no antes, a menos que la fuerza de ventas y la dirección de ventas estén de acuerdo.
Paso 2: La vendedora y sus registros de ventas son el objeto de estudio.
Pasos 3 y 4: El gerente de ventas utilizará todas las facturas y recibos de devolución de ventas de 1980 y 1981 para calcular el número neto de unidades vendidas de cada producto en 1980 y 1981. El gerente de ventas registrará los cálculos y los resultados.
La definición anterior de ventas puede no ser adecuada para otro gerente y fuerza de ventas; sin embargo, si el gerente de ventas la adopta y la fuerza de ventas la entiende, es una definición operativa.
Las definiciones operativas no son triviales. Si la dirección no define operativamente muchas variables y atributos críticos para que tanto los trabajadores como los clientes estén de acuerdo, surgirán problemas graves. El gráfico de control se convierte en una herramienta de gestión inútil debido a una fuente de variación totalmente nueva: la variación de las mediciones. Es responsabilidad de la dirección definir operacionalmente las características que se trazan. Si los inspectores no están de acuerdo entre sí o consigo mismos día a día, se desarrollará el caos. Los trabajadores no saben qué se espera de ellos. Su salida es correcta para el Inspector 1 y no para el Inspector 2; es posible que el trabajo de un empleado haya sido aprobado ayer por el Inspector 1, pero puede que no sea hoy.
Trabajo de la alta dirección
Numerosas personas han escrito recientemente directrices que indican a la gerencia lo que debe hacer para mejorar la productividad:
Cree una institución que tenga un propósito constante y un compromiso a largo plazo con la alta dirección.
Derriba las barreras entre departamentos.
Crear un entorno en el que la gente no tenga miedo de denunciar los problemas.
Desactivar los niveles incorporados de defectos, errores, materiales deficientes,.
No culpe a los trabajadores por los problemas de productividad y calidad.
Sin duda, el lector está familiarizado con ellos. Sin embargo, se siguen pautas de gestión adicionales que pueden no ser tan obvias del enfoque que hemos descrito aquí.
1. No esperes que la inspección resuelva el problema de calidad. En el momento en que se realiza la inspección, el producto ya es aceptable o defectuoso. No puedes inspeccionar la calidad de un producto.
La inspección masiva no separa limpiamente los artículos buenos de los malos. Una mejor manera es monitorear pequeñas muestras de producto para obtener gráficos de control para lograr o mantener el control estadístico. De esta manera, los gerentes podrían eliminar la necesidad de inspecciones y poner el talento de los inspectores a otros usos. Los vendedores y los clientes también pueden comparar sus instrumentos y pruebas; los vendedores y los clientes podrían empezar a hablar el mismo idioma. La inspección bajo presión suele ser una farsa: ya sea que entre o salga, todo pasa. Y porque la responsabilidad dividida significa que nadie es responsable, 200% la inspección es menos fiable que 100% inspección.
2. Como cuestión de política, deja de adjudicar el negocio al mejor postor. Sin una medida de la calidad que se compra, el precio no tiene sentido.
Para juzgar la calidad, los gerentes de compras necesitan educación y experiencia en la evaluación de la evidencia estadística de calidad. Si los compradores se convierten en expertos en evaluar la calidad, la mayoría de ellos reducirá drásticamente el número de proveedores con los que tratan. Un proveedor que no conoce sus costes, ni si puede repetir mañana la distribución de calidad de hoy, no es un buen socio comercial.
3. Elimine las metas, los objetivos numéricos, los eslóganes («cero defectos»), las imágenes y los carteles que los supervisores suelen colocar en las plantas para instar a las personas a aumentar la productividad. Desafortunadamente, estos programas de «mejora de la productividad» dejan los defectos justo donde están. No descubren ni corrigen fallos del sistema, ni proporcionan las medidas correctivas necesarias para que los gestores de señales estadísticas tomen medidas correctivas. No responden a la pregunta crítica: «¿Cómo podemos mejorar la productividad?»
4. Elimina las cuotas de trabajo. Las cuotas de trabajo no tienen en cuenta las variaciones normales del sistema. No incluyen una forma de detectar la necesidad de medidas correctivas ni una forma de asignar responsabilidades a la dirección o al delegado de la dirección en línea. Por ejemplo, un gerente de banco puede determinar el número de clientes que cree que un cajero debe manejar en una hora, el número de cálculos de intereses y multas que alguien debe calcular en una hora, y una cifra similar para cualquier otra actividad. Sin embargo, los estándares no dicen nada sobre la calidad del trabajo ni dan al gerente ninguna forma de entender la variación del proceso. Las normas no indican qué acciones deben tomar los gerentes ni cómo mejorar el proceso.
5. Instituir programas de formación en estadística para que los gerentes y supervisores entiendan cómo gestionar la calidad. La supervisión forma parte del sistema y, por supuesto, es responsabilidad de la dirección. Los métodos estadísticos son ayudas vitales para los capataces y los gerentes de producción para indicar las causas del desperdicio, la baja productividad y la mala calidad. Los gerentes también pueden utilizarlos para determinar cuándo los empleados están completamente capacitados y cuándo podría ayudar una formación adicional.
Fuentes
Comisión E-11 Manual de la Sociedad Americana de Pruebas y Materiales sobre Control de Calidad de Materiales (Publicación técnica especial No. 15C, 1951) y Manual de la Sociedad Americana de Pruebas y Materiales sobre Presentaciones de Datos y Análisis de Gráficas de Control (Publicación técnica especial No. 15D, 1976).
Irving W. Burr Estadísticas de ingeniería y control de calidad (Nueva York: McGraw-Hill, 1953).
Acheson J. Duncan Control de calidad y estadísticas industriales 4ª ed. (Homewood, Ill.: Richard D. Irwin, 1974).
David Durand Caos estable (Nueva York: General Learning Corporation, 1971).
A.V. Feigenbaum Control de calidad (Nueva York: McGraw-Hill, 1951) y Control de calidad total: ingeniería y gestión (Nueva York: McGraw-Hill, 1961).
Beca Eugene L. Control estadístico de calidad (Nueva York: McGraw-Hill, 1946, 1952, 1964, 1972). Las ediciones posteriores son de Eugene L. Grant y Richard S. Leavenworth.
Kaoru Ishikawa Guía para el control de calidad (Tokio: Organización Asiática de Productividad, 1976).
Joseph M. Juran Manual de control de calidad 3ª ed. (Nueva York: McGraw-Hill, 1974).
Harry H. Ku y col. El proceso de medición Publicación especial No. 300 de la Oficina Nacional de Normas (Washington, D.C.: Imprenta del Gobierno de los Estados Unidos, 1969).
E. H. Mac sobrina Especificaciones industriales 3ª ed. (Nueva York: John Wiley, 1953).
Ellis R. Ott Control de calidad de procesos (Nueva York: McGraw-Hill, 1975).
Walter A. Shewhart El control económico de los productos manufacturados (Nueva York: Van Nostrand, 1931; Sociedad Americana de Control de Calidad, 1980).
Leslie E. Simon Manual del ingeniero de métodos estadísticos (Nueva York: John Wiley, 1941).
• • •
Estas directrices indican lo que la alta dirección debe hacer para mejorar la productividad y la calidad. Aunque seguir cada una de las directrices no producirá resultados tangibles, al mismo tiempo, una empresa que comienza hoy plenamente comprometida obtendrá ganancias impresionantes en breve.
Un segundo lugar para obtener resultados rápidos sería eliminar el miedo, ayudar a las personas a sentirse seguras y ayudar a las personas a superar el miedo a denunciar problemas con el equipo o con los materiales entrantes. Los gerentes pueden alcanzar este objetivo en dos o tres años y obtener resultados económicos poderosos.
1. Véase, por ejemplo, Joseph M. Juran, Manual de control de calidad, 3ª ed. (Nueva York: McGraw-Hill, 1974).
2. Se puede encontrar una discusión sobre cómo calcular el tamaño de una muestra en numerosos textos, algunos de los cuales hemos enumerado al final del artículo.
3. W. Edwards Deming, Calidad, productividad y posición económica (Cambridge: Centro MIT de Ingeniería Avanzada, 1982).
— Escrito por Howard S. Gitlow Howard S. Gitlow Paul T. Hertz