Cummins Engine flexiona su fábrica
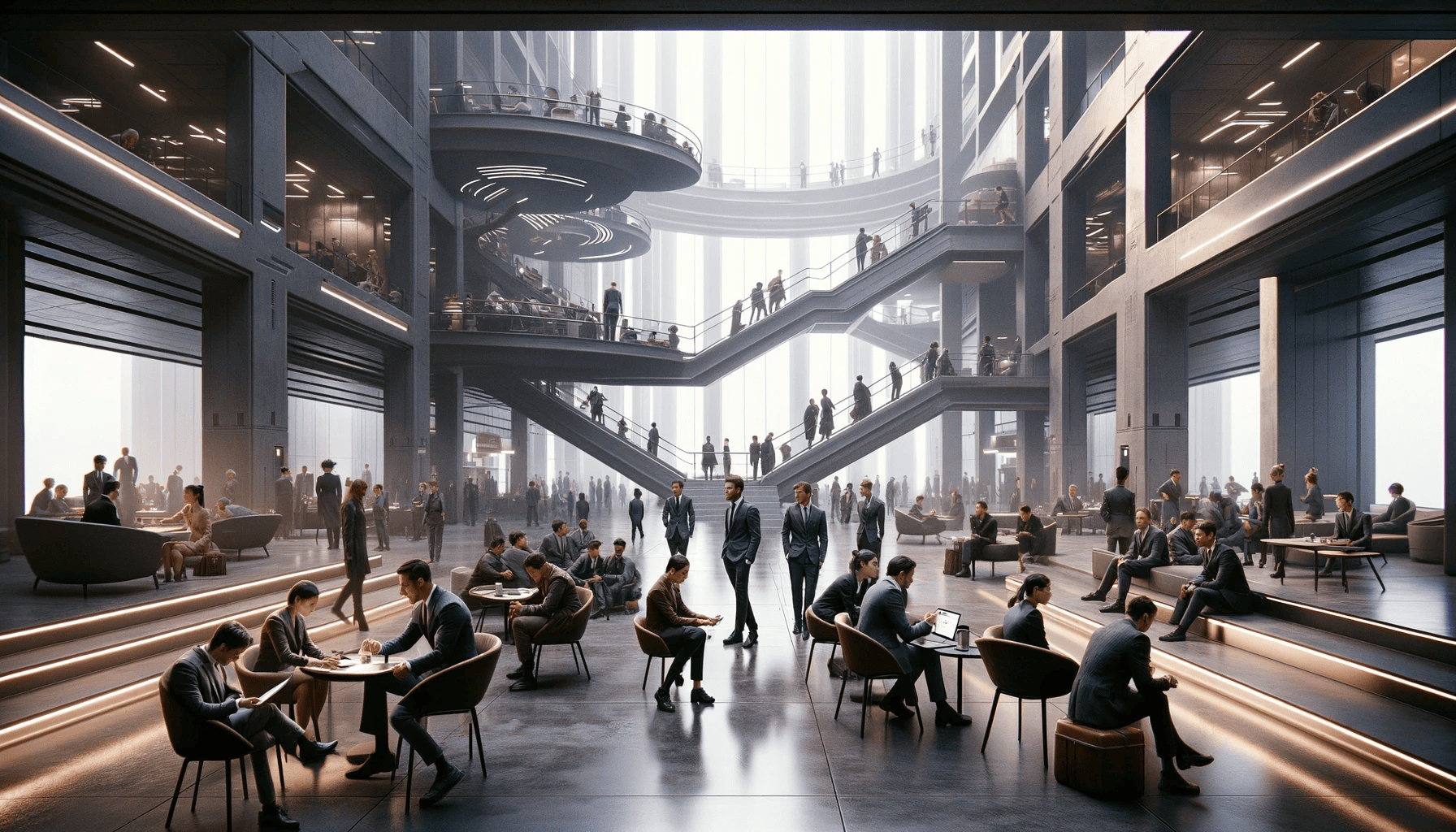
Las reglas están cambiando. ¿Lo estamos? En 1986, Cummins Engine Company, un fabricante de motores diésel con sede en Columbus, Indiana, se encontraba en una situación familiar para muchas empresas de Rust Belt. Hasta mediados de la década de 1970, Cummins había disfrutado de una línea de productos relativamente estable y sostenía constantemente más de 50% del mercado. Creamos lo que nuestros clientes creían que era un motor indestructible, la serie NT, y nuestras fábricas se organizaron para satisfacer la demanda constante del motor. Ejecutamos enormes volúmenes en líneas de mecanizado dedicadas con una eficiencia espléndida, hasta 500 motores al día; la fabricación por lotes se ha elevado a una ciencia. Nadie en la parte superior de la empresa se preocupó mucho por que llevemos enormes inventarios de trabajo en proceso, siempre y cuando entreguemos buena calidad a tiempo.
Luego llegaron las regulaciones federales de emisiones y, por supuesto, la intensa competencia de empresas como Komatsu y Caterpillar. Desde entonces, Cummins ha tenido que lanzar siete generaciones del motor NT y tres familias de motores completamente nuevas: las series B, C y L. Mientras tanto, los clientes esperan una atención cada vez mayor y una rapidez de respuesta sin precedentes a sus necesidades individuales. Por si esto fuera poco, Cummins ha tenido que recortar los precios de los nuevos productos de 20% hasta 40% solo para conservar la cuota de mercado. Inevitablemente, la alta dirección ordenó que la fábrica redujera los costos y el tiempo de entrega, lo que es otra forma de decir que reduzca el WPI, en el mismo momento en que la fábrica estaba tratando de lidiar con la proliferación de piezas.
En 1986, nuestro catálogo ofrecía más de 100.000 piezas. Y aunque nuestros diseñadores se estaban volviendo más sensibles a nuestras dificultades de fabricación, el número seguía aumentando. Para una de nuestras familias de motores más recientes, Cummins ofrece 86 volantes diferentes, 49 opciones de carcasa de volante y 17 tipos de motores de arranque con 12 posibles montajes, todos los cuales se pueden ensamblar en aproximadamente 1200 combinaciones para satisfacer las aplicaciones de los clientes. Así que, mientras luchábamos por fabricar piezas para todos los modelos nuevos, sin mencionar a ese tipo de Kansas al que le encanta su caballo de batalla de 1938 y rechaza obstinadamente un reemplazo gratuito, nos enfrentamos a tener que personalizar los productos, modificar piezas que no se demostraron en el campo y entregarlas en plazos de entrega más cortos. Los mercados se estaban fragmentando cada vez más y la demanda se volvía más cíclica. Todas estas presiones garantizaban un menor volumen de producción, lo que no era lo mejor para los costes unitarios. Lo peor de todo es que las piezas de bajo volumen eran líneas de obstrucción dedicadas anteriormente a piezas de gran volumen.
Frustrado por las limitaciones de la antigua fabricación por lotes, Cummins encargó a un pequeño grupo de trabajo que desarrollara conocimientos fundamentales sobre el problema de la reorganización de nuestras fábricas para crear una línea de productos proliferada. Nos pusimos a trabajar a principios de 1987, estudiando las fábricas de otras empresas y la nuestra, y lo que aprendimos ha funcionado bien para Cummins. Pero también ha dado una profundidad inesperada al término «fábrica flexible». Expusimos algo importante sobre cómo los avances en la industria de las máquinas herramienta, tan dinámicos hoy en día como los de la tecnología de la información, están dando forma a la nueva competencia en materia de bienes duraderos. Las reglas, de hecho, están cambiando.
Más allá de la fabricación celular
La mayoría de las fábricas empiezan como talleres de trabajo: la escala de producción crece, se añaden máquinas y también lo son los nuevos productos. En poco tiempo, se produce un «diseño del proceso», mediante el cual se agrupan máquinas similares: tornos con tornos, amoladoras con amoladoras. Los lotes de piezas se mezclan desde el departamento de fresado al departamento de taladrado. Hay muchas desventajas bien documentadas en este modo de operación, entre las que cabe destacar la evolución de rutas de flujo extremadamente complicadas. Se necesita un enorme tiempo acumulativo para que las piezas semiacabadas se muevan de un departamento a otro y luego esperen en la fila. El resultado son plazos de entrega excesivos, inventarios excesivos y ninguna responsabilidad clara por el WIP.
Es precisamente para evitar estos problemas que tantos fabricantes, incluido Cummins, han reorganizado sus fábricas en departamentos de productos, cada uno responsable de una familia de productos relacionados. Han agrupado sus máquinas en «celdas», grupos en forma de U que mueven una pieza del torno a la amoladora a la fresadora con poca interrupción. Dedicadas a una gama más o menos estrecha de piezas, estas células de mecanizado son atendidas por uno o dos operadores; su lógica no es más notable que la de las líneas de transferencia de la automatización dura. En las celdas, la WIP se transmite de máquina a máquina sin «descansar» y, por lo tanto, pasa por los procesos de conversión sin problemas, a menudo con un sistema de extracción simple como kanban para gestionar el flujo. Casi siempre se producen mejoras sorprendentes por el traslado a las celdas. Muchos consultores de fabricación deben su sustento a los ahorros reales en tiempo de entrega, inventario de WIP y mano de obra directa que se pueden lograr al adherirse al canon justo a tiempo.
Entre 1980 y 1985, la mayoría de las fábricas de Cummins ya habían hecho la transición a la fabricación celular. En la planta de Columbus, nos habíamos reorganizado en 15 celdas, cada una de las cuales mecanizaba un grupo relativamente pequeño de piezas relacionadas: una línea de bomba de agua, una línea de volante, una línea de colector,. Invertimos solo$ 60.000 para máquinas nuevas,$ 105.000 para accesorios y herramientas adicionales, y aproximadamente$ 40.000 para mover cosas. En el primer año, realizamos un 25% reducción de espacio, a 30% reducción de chatarra, y más de 90% reducción del inventario de WIP. Ahorramos más de un millón de dólares en costos laborales (en su mayoría indirectos).
Sin embargo, no se necesita la imaginación de Frederick Winslow Taylor para ver que las técnicas de fabricación celular por sí solas son inadecuadas para el desafío de una línea de productos muy proliferada, solo el problema que había asolado a Cummins. La clave de la fabricación celular —como escriben expertos en JIT como Richard J. Schonberger— es el cambio. Si una célula va a mecanizar, digamos, 7 piezas de manera eficiente, los operadores de celdas deben poder cambiar herramientas y accesorios en tornos, taladros y amoladoras consecutivos lo suficientemente rápido como para que el tiempo de inactividad no erosione seriamente las ganancias (en tiempo, mano de obra, etc.) de organizarse en celdas en primer lugar. Pero, ¿qué pasa cuando 7 partes se convierten en 14 y las tiradas de 10.000 se convierten en 500? Células de mecanizado estrangulador.
Peor aún, como ya he dicho, las partes tienden a proliferar en los extremos, al principio y al final, de sus ciclos de vida. Las piezas nuevas cambian a medida que la I+D perfecciona los diseños; las piezas maduras se personalizan más. Y Cummins se comprometió a sacar nuevos productos y a dar servicio a los productos antiguos con la misma determinación. La proporción de piezas de bajo volumen aumentó aún más. Nos encontramos sujetos a la «regla 20—80»: unos 20% de las piezas (los corredores más altos) representaban más de 80% de la producción, mientras que los 20 restantes% de producción causada 80% de la disrupción. No éramos la única empresa con cifras de producción tan desproporcionadas. En una gran empresa de equipos industriales estudiamos, alrededor de 80% de la variedad de productos representó un escaso 5%% de la producción total pero consumida 25% de la mano de obra total.
Un cambio rápido no es suficiente
Distorsiones de este tipo han obligado a las fábricas de piezas a hacer demasiados cambios. La WIP en las celdas de mecanizado no fluye sin problemas a menos que fluya de manera uniforme. Si, después de mecanizar un palé de piezas, todos los operadores de células tuvieran que detenerse durante varios minutos (en algunos casos, horas) para cambiar herramientas y accesorios, ¿no habría sido más racional seguir simplemente con el diseño del proceso del taller? Es cierto que el tiempo de ciclo será más rápido en las celdas de mecanizado dedicadas que en la fabricación por lotes. Sin embargo, el rendimiento total de la fábrica puede reducirse a tasas inaceptables. Para Cummins no tenía sentido seguir añadiendo piezas a las celdas de mecanizado (y a los departamentos de producción) para explotar al máximo nuestros equipos o conservar hipotéticas eficiencias de escala. Lo que teníamos era un gran número de piezas diferentes que compitían por los mismos recursos de producción y los ataban.
Como era de esperar, algunas personas de la empresa argumentaron que deberíamos trabajar más duro para reducir el tiempo de configuración. Sin embargo, un estudio minucioso de Cummins y otros fabricantes de equipos reveló que el éxito del cambio se limitaba a líneas de fabricación de mayor volumen, es decir, líneas que normalmente producen menos de diez piezas. Además, la rebaja en la configuración significaría desviar gran parte de la atención de la gerencia hacia una parte desproporcionadamente pequeña de la producción total, es decir, hacia los corredores bajos.
Determinamos que la reducción agresiva de la configuración por sí sola no era suficiente para resolver el problema de las piezas de bajo volumen que congestionaban las líneas dedicadas. Comenzamos a desarrollar una forma más sutil de clasificar las piezas de gran volumen y bajo volumen, siendo esta última la más disruptivo para las líneas de ciclo rápido. Inevitablemente, esto también significaba tener más en cuenta las máquinas herramienta flexibles, a pesar de sus tiempos de ciclo más lentos. Y a medida que nos enfocamos en el volumen, es decir, centrar la fábrica no solo por producto sino también por volumen—nos dimos cuenta de que teníamos una de las claves para hacer que la flexibilidad funcione. Después de todo, los sistemas de gran volumen y bajo volumen deben coexistir prácticamente en todas las fábricas. Sin embargo, la gestión de estos dos tipos de sistemas requiere actitudes, habilidades, equipos y principios de calidad muy diferentes.
Tomemos la dirección de la fuerza laboral. La gestión de procesos de gran volumen requiere nociones tayloristas de supervisión y control: estudios de tiempo y movimiento combinados con un seguimiento estricto del desempeño coordinado de los trabajadores. En entornos de bajo volumen, la administración hace hincapié en la planificación y el soporte, no en la supervisión per se, y en el mantenimiento y la programación de equipos complejos. Los entornos de bajo volumen también requieren personal de fabricación cualificado que esté familiarizado con una amplia variedad de productos y procesos asociados.
El procesamiento de pedidos, la logística y la programación de la producción también son diferentes. Por lo general, las líneas de gran volumen se pueden alimentar mediante sistemas de extracción. Las líneas de bajo volumen, por el contrario, requieren proyecciones de mayor alcance, a menudo generadas por ordenador. También requieren una mayor planificación con los proveedores, que necesitan entregar lotes pequeños de materias primas (piezas fundidas, piezas forjadas, elementos de fijación) no solo a tiempo sino con muy poca antelación. De hecho, más de 50% de envíos atrasados en productos de bajo volumen en otra importante planta de fabricación que estudiamos se debieron a dificultades en el procesamiento de pedidos, pedidos de materiales o planificación de la producción. Observamos que, como era de esperar, las piezas de gran volumen tenían prioridad sobre las piezas de bajo volumen cada vez que se mezclaban.
Y considere los diferentes enfoques de calidad. En la fabricación repetitiva, el control estadístico de procesos se utiliza para trazar el progreso de las características críticas del producto/proceso. En la fabricación de bajo volumen, el SPC se vuelve más difícil debido a las tiradas cortas de los lotes. En este caso, el énfasis debe estar en el control de variables tales como herramientas y fijaciones. También debe haber una documentación rigurosa del proceso para garantizar la replicabilidad de los procedimientos de fabricación.
Finalmente, aprendimos desde el principio que si la gestión exitosa de la fábrica flexible presuponía centrar la fábrica tanto en producto como en volumen, clasificar las piezas simplemente en términos de volumen alto y bajo volumen no iba a funcionar. La distinción era demasiado burda para ser práctica. ¿Es más disruptivo para una célula de mecanizado fabricar 5.000 piezas de una pieza que requiere una hora de configuración o fabricar 10.000 piezas de otra pieza que necesita cuatro horas para su cambio?
Clasificación de piezas tal y como son
A medida que probamos las características funcionales de las distintas piezas que fabrica Cummins, pudimos discernir cuatro categorías de componentes del motor (ver la ilustración del motor Cummins NT para ver ejemplos de cada uno).
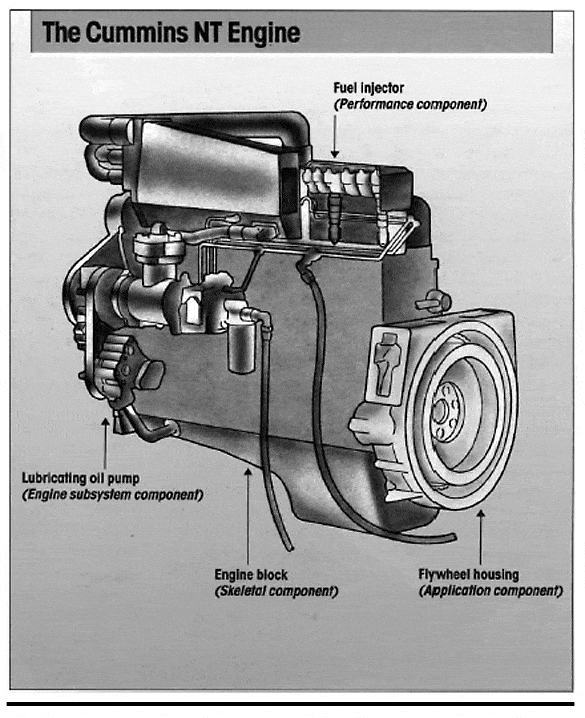
El motor Cummins NT
Componentes esqueléticos como el bloque, la cabeza y la biela, el corazón del motor. Estas piezas se caracterizan por su baja proliferación, volúmenes elevados y diseños relativamente estables.
Componentes del subsistema del motor como la bomba de agua y la bomba de aceite lubricante. Estas piezas garantizan y optimizan el rendimiento del motor y se caracterizan por un alto volumen y una baja proliferación dentro de la generación actual de motores maduros. Sin embargo, para los motores más nuevos, los diseños pueden ser bastante volátiles; hay frecuentes modificaciones de diseño para mejorar el rendimiento del motor.
Componentes de aplicación como colectores de escape y carcasas de volante, piezas que reflejan las preferencias individuales de los clientes. Estas piezas están muy proliferadas pero disfrutan de diseños moderadamente estables.
Componentes de rendimiento tales como turbocompresores y frenos de compresión. Estos componentes se caracterizan por su baja proliferación, volúmenes moderados y diseños razonablemente estables. Este grupo también incluye piezas como inyectores de combustible, que pueden requerir volúmenes altos o bajos, pero que siguen exigiendo métodos de fabricación fronterizos como electrodescarga o mecanizado por láser.
Tras digerir estas distinciones, desarrollamos cinco clases generales de componentes utilizando los tres parámetros de volumen, previsibilidad de la demanda y estabilidad del diseño: (1) productos de gran volumen con demanda predecible y diseño relativamente estable; (2) productos de volumen medio a bajo con demanda predecible pero diseño en rápida evolución; (3) piezas de volumen medio y bajo con demanda predecible y diseño estable; (4) componentes de bajo volumen con una demanda muy impredecible; y (5) productos que requieren procesos de fabricación no tradicionales.
La última clase de componentes, que requerían procesos especializados o únicos, parecía imposible de separar por volumen. Todos estos componentes fluirían a la misma zona de mecanizado, donde tendrían que coexistir, independientemente de la demanda. La maquinaria de, por ejemplo, el mecanizado láser es demasiado costosa y las habilidades técnicas demasiado especializadas como para esperar que cualquier planta de Cummins soporte más de una de estas áreas de producción. Las piezas simplemente tendrían que esperar en la fila; los corredores altos irían al frente de la cola.
Las cosas se pusieron más interesantes con las cuatro primeras clases de piezas. Considere una fábrica hipotética que ha hecho la transición a la fabricación celular y donde los patrones de demanda se indican en la tabla «¿Qué son las piezas disruptivas?»
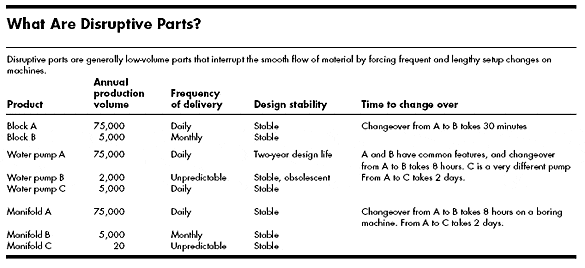
¿Qué son las piezas disruptivas? Las piezas disruptivas suelen ser piezas de bajo volumen que interrumpen el flujo suave del material al forzar cambios de configuración frecuentes y prolongados en las máquinas.
Dado su gran volumen y su diseño estable, el bloque A probablemente se fabricará en una línea de transferencia. Dado que el cambio del bloque A al bloque B es relativamente rápido, B podría fabricarse en la misma línea. Sin embargo, la situación de las bombas de agua es claramente diferente. Aunque la bomba de agua A es una pieza de gran volumen, es probable que una inversión en maquinaria dedicada o especial no dé sus frutos dada la corta vida útil de la pieza. En Cummins, los productos de gran volumen con diseños volátiles se fabrican cada vez más en celdas de mecanizado flexibles, al igual que los prototipos y la introducción de nuevos productos.
La bomba de agua B, que comparte muchas características de diseño con A pero con volúmenes más bajos, también es una candidata natural para esta misma celda flexible. Las configuraciones que solían tardar ocho horas ahora tardan menos de una. Sin embargo, la flexibilidad de la celda se desperdicia en una pieza como la bomba de agua C, con su diseño estable, volumen medio y demanda muy predecible. La forma más económica de producir C, hemos observado, es utilizar el equipo existente en una célula convencional, tal y como defiende Richard J. Schonberger en su artículo sobre fabricación frugal.1
En cuanto al departamento múltiple, presenta varios desafíos interesantes. Manifold A, el producto principal, es un excelente candidato para una célula de máquinas dedicadas, dado su alto volumen, diseño estable y demanda predecible. El colector B interrumpe el flujo suave del material en esta celda principalmente porque los operadores tardan ocho horas en instalar la mandrinadora en la misma línea. Un buen enfoque en casos como este es crear una «célula híbrida» con varias máquinas convencionales y una mandrinadora controlada numéricamente por ordenador. Las características comunes a todas las piezas se producen en los equipos convencionales. Las funciones que difieren de una pieza a otra se mecanizan en la máquina CNC.
No hay duda de que el equipo flexible ralentizará el tiempo de ciclo de la célula. Sin embargo, las configuraciones se reducen al mínimo. En general, el rendimiento de la célula es más rápido de lo que sería si la máquina flexible fuera reemplazada por una máquina de uso especial, que arranca el producto más rápidamente pero necesita mucho tiempo de inactividad para adaptarse al cambio. Las células híbridas también pueden manejar cosas como los patrones de orificios de montaje en los soportes del volante, que no cambian significativamente con el tiempo. La mayoría de los soportes de volante pueden seguir produciéndose en líneas de gran volumen, mientras que las variaciones pueden enviarse fuera de línea a máquinas flexibles. Cada vez más departamentos de producción necesitarían adquirir máquinas flexibles para manejar tales variaciones; las materias primas y los sistemas logísticos no se verían afectados materialmente.
Finalmente, Manifold C, el verdadero asesino. Su prolongado tiempo de configuración y su demanda prácticamente impredecible interrumpen las operaciones diarias. Descubrimos que los productos como C se separan mejor en un área de fabricación muy flexible y de bajo volumen. Dichos productos se fabricarán de principio a fin en este departamento de producción, eliminando cualquier ambigüedad sobre quién tiene la responsabilidad final de la producción.
Para ayudarnos a diferenciar las piezas, especialmente las de bajo volumen, hemos desarrollado un «sistema experto» sencillo y basado en reglas, que aparece de forma simplificada en la tabla «Asesor de opciones de mecanizado». Basándonos en las respuestas de los operadores a 14 preguntas, podemos ofrecer una recomendación cuantitativa sobre si se debe mecanizar una pieza específica en una celda convencional, en una celda de sistema de fabricación flexible (FMS) o en máquinas CNC en un área de bajo volumen.
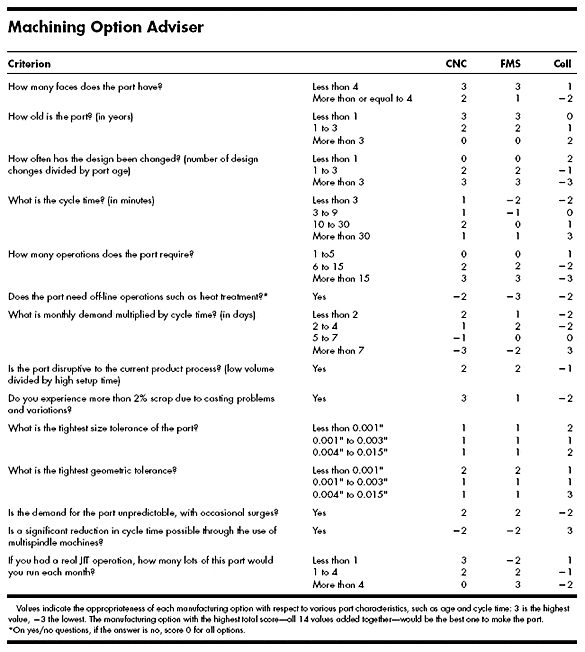
Asesor de opciones de mecanizado Los valores indican la idoneidad de cada opción de fabricación con respecto a las distintas características de las piezas, como la antigüedad y el tiempo del ciclo: 3 es el valor más alto,! 3 el más bajo. La opción de fabricación con la puntuación total más alta (todos los 14 valores sumados) sería la mejor para fabricar la pieza.
Tomemos el ejemplo de la pieza de bajo volumen X. Tiene menos de cuatro caras, por lo que obtiene una puntuación de 3 para una máquina CNC, 3 para una FMS y 1 para una celda de máquinas convencionales. Tiene diez años, por lo que puntúa 0 para CNC, 0 para FMS y 2 para celda. Tras la puntuación de cada criterio, los valores de cada opción de mecanizado (algunos valores son negativos) se suman al alza. La opción con mayor puntuación es la mejor forma de fabricar la pieza X. Al final, las puntuaciones para la parte X fueron: CNC, 16; FMS, 14; celda convencional, 0. Por lo tanto, la pieza pasaría a una celda de mecanizado soportada por CNC.
¿Máquinas herramientas flexibles para grandes volúmenes?
Algunas de las soluciones a las que hemos llegado en el taller de Cummins parecen violar lo que ha sido la sabiduría convencional desde el artículo de Ramchandran Jaikumar de 1986 «Fabricación postindustrial». Jaikumar criticó a los fabricantes estadounidenses de piezas por utilizar máquinas herramienta flexibles para ejecutar volúmenes bastante altos. La verdadera virtud de una máquina flexible, observó, radica en su capacidad para manejar simultáneamente muchos tipos diferentes de piezas, incluso tamaños de lote de una sola. «Las empresas estadounidenses utilizaron los FMS de forma incorrecta: para la producción de gran volumen de unas pocas piezas en lugar de para la producción de gran variedad de muchas piezas a bajo costo por unidad».2
Cummins es una de esas empresas que operan volúmenes bastante altos en máquinas flexibles, especialmente en celdas híbridas. Sin embargo, ha dado sus frutos generosamente para nosotros. En los primeros 18 meses después de su introducción, los nuevos frenos de compresión de nuestros motores sufrieron 14 cambios de diseño. En líneas menos flexibles, estos cambios probablemente habrían tardado varios años y muchos millones de dólares en incorporarse, lo que solo habría inhibido el desarrollo de modificaciones que mejoraran el rendimiento. De nuevo, la decisión de producir este componente en un FMS aumentó considerablemente el tiempo de ciclo. Sin embargo, redujo el tiempo de comercialización quizás dos años, redujo los gastos anuales de garantía en un estimado$ 300.000 y costes reducidos para el cliente en más de 30%.
Nada de esto es para refutar la visión fundamental de Jaikumar. Nosotros también utilizamos máquinas flexibles para manejar muchas piezas diferentes de bajo volumen, aunque no necesariamente para llegar a nuevos mercados personalizados. Hemos descubierto que las máquinas flexibles son igualmente interesantes en la consolidación de líneas de producción para productos obsoletos. En 1986, adquirimos un FMS de seis máquinas para consolidar la producción de muchas de estas piezas impredecibles y de bajo volumen. Resultó ser una forma bastante económica de mantener contentos a los antiguos clientes. (La producción de bombas de agua y componentes del sistema de lubricación para muchos de los motores industriales más antiguos y especializados de Cummins solía estar dispersa en varias líneas de máquinas antiguas; las configuraciones, los cambios y el tiempo de inactividad representaron más del 50%% de las horas de producción de esas máquinas.)
Lo que quiero decir es que las máquinas flexibles pueden ser importantes de formas que Jaikumar no ha abordado específicamente: como una protección contra los cambios de diseño, un impulso en la carrera hacia el mercado, un medio para atender a los clientes leales. También son una salvación para las células de mecanizado dedicadas, donde las variaciones de piezas, aunque no son realmente grandes, son lo suficientemente grandes como para hacer que el cambio sea problemático y en las que el tiempo de inactividad cuesta más a Cummins que la propia máquina flexible.
Vale la pena señalar que durante los últimos cuatro años, las máquinas CNC independientes (al igual que las computadoras) se han vuelto más inteligentes, económicas y fáciles de programar e integrar. Antes, comprar flexibilidad significaba comprar una célula completa y exótica, en la que las máquinas hablaban esencialmente su propio idioma: una especie de mainframe de mecanizado. Ahora, las máquinas CNC independientes con programación conversacional pueden hablar mucho más fácilmente con sus operadores, con su entorno e incluso con los sistemas de programación. A menudo cuestan menos que las máquinas dedicadas (que sin duda son mucho más rápidas) y pueden mantener las tolerancias casi igual de bien.
Volantes de inercia: prueba del pudín
Era hora de poner en práctica la teoría. Las carcasas del volante habían sido nuestro mayor dolor de cabeza. Los consultores de una firma de contabilidad Big Eight aconsejaron obtener una parte considerable de esta línea. En su lugar, decidimos atacar el problema. Dividimos los volantes en una línea de flujo de gran volumen y una celda de bajo volumen. De los 160 tipos de piezas originales mecanizadas en la zona, solo 11, que comprendían más de 85% del volumen, permaneció en la línea de alto volumen reorientada. Las 149 restantes se reprocesaron en una célula de mecanizado flexible recién adquirida.
Este proyecto, que duró unos tres años y$ 3 millones para completar, ha demostrado ser un éxito magnífico, como ilustra la tabla «Resultados del reenfoque de la carcasa del volante». Si bien el énfasis inicial se centraba más en mejorar la entrega que en reducir los costos, los costos de los productos se han desplomado más del 40%%, lo que da como resultado un retorno de la inversión de aproximadamente el 90%%. Con estas mejoras, Cummins se ha convertido en el fabricante de carcasas de volante de menor costo con un récord de entrega casi perfecto.
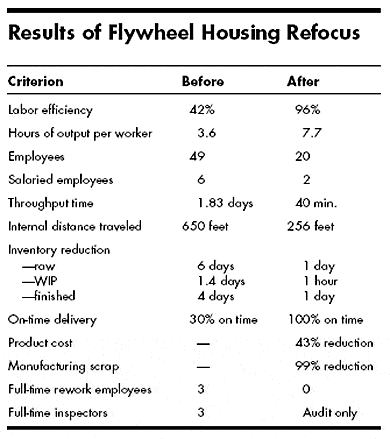
Resultados del reenfoque de la carcasa del volante
Los volantes de inercia también eran un problema en la fábrica de motores de nuestra empresa conjunta en India. Una vez más, tuvimos que racionalizar el área de producción de volantes de inercia, donde las máquinas de alto rendimiento y para usos especiales cuentan con una amplia variedad de piezas, incluidas carcasas de volante y cárteres de aceite, soportes, soportes y tapas. Y para agravar el problema estaban los componentes que tenían que ir a otro departamento porque requerían operaciones CNC intermedias.
Dividimos el área en cuatro celdas, cada una con un caudal bien definido: volantes, carcasas de volante, cárteres de aceite y piezas diversas. Las máquinas dedicadas a células individuales eliminaron el flujo cruzado de materiales. Estas medidas restauraron el enfoque del producto. A continuación, centramos el volumen mediante la integración de un centro de mecanizado CNC en la línea de carcasas del volante para mecanizar carcasas de bajo volumen. Subcontratamos carcasas de gran volumen a pequeñas unidades de fabricación local con una sobrecarga sustancialmente menor.
Los beneficios de esta reorganización fueron extraordinarios: 95% reducción de la manipulación de materiales; 30% reducción del espacio; 50% reducción del inventario de WIP; 50% reducción del tiempo de entrega. También calculamos reducciones significativas pero no cuantificadas en la mano de obra directa y en las entregas tardías.
En otra reorganización en nuestra planta de motores Columbus, consolidamos la producción de muchos componentes de sistemas de lubricación y agua obsolescentes y de bajo volumen en un FMS de seis máquinas. Anteriormente, estas piezas estaban dispersas en varias líneas de máquinas; las configuraciones, los cambios y el tiempo de inactividad representaban más de 50% de horas de producción. Hemos obtenido beneficios sustanciales gracias a esta consolidación: 50% reducción de mano de obra directa y manipulación de materiales; 70% reducción del espacio y del número de máquinas; 75% reducción del inventario de WIP; 50% reducción de la chatarra de fabricación y reducción del plazo de entrega de 42 días a 1 día.
En Cummins, nos dimos cuenta de que para enfrentar los nuevos desafíos de fabricación, necesitábamos nada menos que una reorganización total y continua de nuestras instalaciones. Lo conseguimos mediante un procedimiento de cuatro pasos.
1. Coloque la fábrica en células centradas en el producto, familias de enrutamiento o productos similares en grupos de máquinas agrupados estrechamente.
2. Una vez que la producción esté funcionando sin problemas, vuelva a organizarse, dividiendo la fábrica conceptualmente en diferentes clases de producción en función del volumen, la estabilidad del diseño y la previsibilidad de la demanda.
3. Asigne cada producto, según sus requisitos de producción, a la clase adecuada de maquinaria de producción. Fabricar piezas en la clase de equipo equivocada (piezas de bajo volumen en líneas de transferencia, por ejemplo) provoca una pérdida de flexibilidad, ineficiencias y, finalmente, falta de competitividad.
4. Gestione continuamente la transición de las piezas de una clase de producción a otra a medida que evolucionan los ciclos de vida del producto.
No hay nada radical en esta propuesta, que básicamente es la fabricación de JIT que va más allá del estrecho sentido de la fabricación celular y la reducción de la configuración. La aplicación orquestada de estos conceptos dará lugar a una fábrica flexible, el verdadero campo de batalla industrial de la próxima década.
1. Véase «Frugal Manufacturing», HBR septiembre-octubre de 1987, p. 95.
2. HBR noviembre-diciembre de 1986, p. 69.
— Escrito por Ravi Venkatesan