Calidad robusta
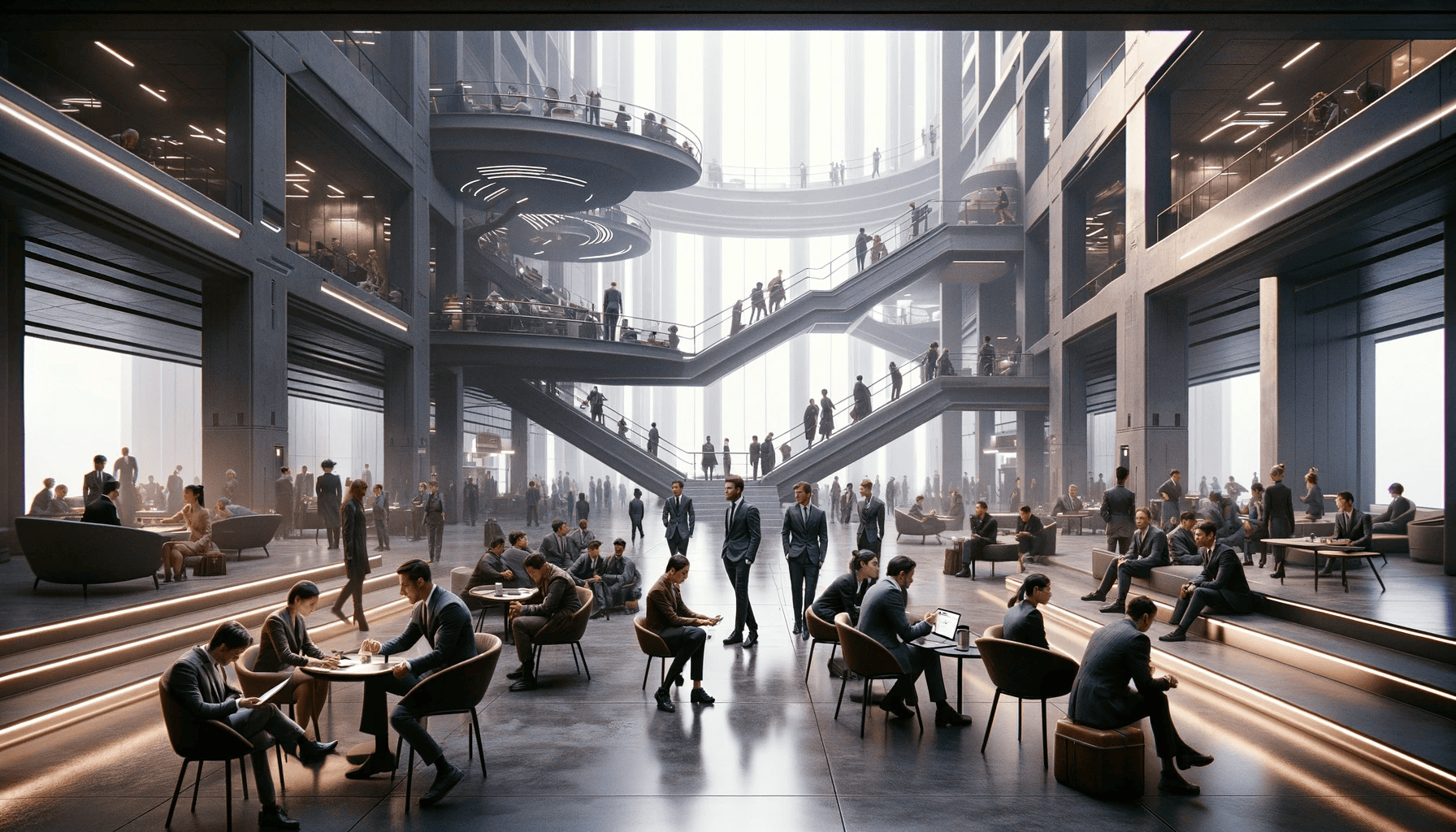
Cuando un producto falla, debes reemplazarlo o arreglarlo. En cualquier caso, debes rastrearlo, transportarlo y disculparte por ello. Las pérdidas serán mucho mayores que los costos de fabricación, y ninguno de estos gastos recuperará necesariamente la pérdida de su reputación. Taiichi Ohno, el renombrado ex vicepresidente ejecutivo de Toyota Motor Corporation, lo expresó de esta manera: Independientemente de lo que un ejecutivo crea que son las pérdidas de mala calidad, en realidad son seis veces mayores. ¿Cómo pueden minimizarlos las empresas manufactureras? Si los directivos estadounidenses aprenden solo un nuevo principio de la colección conocida ahora como Métodos Taguchi, que sea así: la calidad es una virtud del diseño. La «robustez» de los productos depende más de un buen diseño que del control en línea, aunque sea riguroso, de los procesos de fabricación. De hecho, aunque no tan evidente, la falta inherente de robustez en el diseño del producto es el principal impulsor de los gastos de fabricación superfluos. Pero los gerentes tendrán que aprender más de un principio para entender por qué.
Los imperativos de calidad de Taguchi
- Las pérdidas de calidad se deben principalmente a la falla del producto después de la venta; la «robustez» del producto depende más del diseño del producto que del control en línea, aunque sea riguroso, de los procesos de fabricación.
- Los productos robustos ofrecen una «señal» fuerte independientemente del «ruido» externo y con un mínimo de «ruido» interno. Cualquier refuerzo de un diseño, es decir, cualquier aumento notable en la relación señal-ruido de los componentes, mejorará simultáneamente la robustez del producto en su conjunto.
- Para establecer objetivos con las relaciones señal/ruido máximas, desarrolle un sistema de ensayos que le permita analizar los cambios en el rendimiento general del sistema de acuerdo con la promedio efecto del cambio en las piezas componentes, es decir, cuando se someten las piezas a valores, tensiones y condiciones experimentales variables. En los productos nuevos, los efectos medios se pueden discernir más eficazmente mediante «matrices ortogonales».
- Para crear productos robustos, establezca valores objetivo ideales para los componentes y, a continuación, minimice el promedio del cuadrado de desviaciones de los componentes combinados, promediado en las distintas condiciones de uso del cliente.
- Antes de que los productos pasen a la fabricación, se establecen las tolerancias. La pérdida general de calidad aumenta entonces por el cuadrado de la desviación del valor objetivo, es decir, por la fórmula cuadrática L=D2 C, donde la constante, C, viene determinada por el coste de la contramedida que podría emplearse en la fábrica. Esta es la «función de pérdida de calidad».
- No se gana prácticamente nada con el envío de un producto que apenas satisface el estándar corporativo sobre un producto que simplemente falla. Ponte en el objetivo, no intentes mantenerte dentro de las especificaciones.
- Trabaje sin descanso para lograr diseños que puedan producirse de forma coherente; exija coherencia a la fábrica. Es más probable que el apilamiento catastrófico se deba a una desviación dispersa dentro de las especificaciones que a una desviación constante en el exterior. Cuando la desviación del objetivo es coherente, es posible ajustarlo al objetivo.
- Un esfuerzo concertado para reducir las fallas de los productos en el campo reducirá simultáneamente el número de defectos en la fábrica. Esfuércese por reducir las variaciones en los componentes del producto y reducirá las variaciones en el sistema de producción en su conjunto.
- Las propuestas competidoras de equipos de capital o propuestas competidoras de intervenciones en línea pueden compararse sumando el coste de cada propuesta a la pérdida de calidad media, es decir, las desviaciones esperadas de la misma.
Cero defectos, productos imperfectos
Durante una generación, los gerentes e ingenieros estadounidenses han calculado que las pérdidas de calidad son equivalentes a los costos que absorbe la fábrica cuando fabrica productos defectuosos: el valor despilfarrado de los productos que no se pueden enviar, los costos añadidos de reelaboración,. La mayoría de los gerentes piensan que las pérdidas son bajas cuando la fábrica envía prácticamente lo que construye; tal es el mensaje del control estadístico de calidad y otros programas tradicionales de control de calidad que subsumiremos bajo el seductor término «cero defectos». Por supuesto, a los clientes no les importa un comodo el historial de una fábrica de mantenerse «dentro de las especificaciones» o minimizar la chatarra. Para los clientes, la prueba de la calidad de un producto está en su rendimiento cuando se golpea, sobrecarga, cae y salpica. Entonces, demasiados productos muestran un comportamiento temperamental y degradaciones de rendimiento molestas o incluso peligrosas. Todos preferimos fotocopiadoras cuyas copias sean claras con poca potencia; todos preferimos coches diseñados para conducir de forma segura y predecible, incluso en carreteras mojadas o con baches, con vientos cruzados o con neumáticos ligeramente inflados o demasiado inflados. Decimos que estos productos son robustos. Ganan una lealtad constante de los clientes. Los ingenieros de diseño dan por sentado las fuerzas ambientales que degradan el rendimiento (lluvia, baja tensión y similares). Intentan contrarrestar estos efectos en el diseño del producto: aislar cables, ajustar las bandas de rodadura de los neumáticos, sellar juntas. Pero algunas degradaciones del rendimiento provienen de la interacción de las propias partes, no de que les ocurra nada externo. En un producto ideal, en cualquier cosa ideal, las piezas funcionan en perfecta armonía. La mayoría de los productos reales, desafortunadamente, contienen perturbaciones de un tipo u otro, generalmente el resultado de una malla defectuosa de un componente con los componentes correspondientes. Un eje de transmisión vibra y desgasta prematuramente una junta universal; el motor de un ventilador genera demasiado calor para un microprocesador sensible. Dichas degradaciones del rendimiento pueden deberse a que algo va mal en la fábrica o a un fallo inherente en el diseño. Un eje de transmisión puede vibrar demasiado debido a un torno desalineado o a una forma mal concebida; un motor puede resultar demasiado caliente porque se ensambló incorrectamente o se introdujó en el diseño de forma impetuosa. Otra forma de decir esto es que el trabajo en curso puede estar sujeto a grandes variaciones en el proceso y el ambiente de la fábrica, y que los productos pueden estar sujetos a grandes variaciones en las condiciones de uso del cliente. ¿Por qué insistimos en que la mayoría de las degradaciones son el resultado de este último tipo de fallos, fallos de diseño y no de variaciones en la fábrica? Porque las variaciones ambientales o de proceso a las que se puede someter el trabajo en proceso en la fábrica no son tan dramáticas como las variaciones a las que los productos están sometidos en manos del cliente, obvias cuando se piensa en ello, pero ¿cuántos exponentes de Zero Defectos lo hacen? Zero Defectos dice: «El esfuerzo por reducir las fallas del proceso en la fábrica reducirá simultáneamente los casos de fallas del producto en el campo. Decimos que el esfuerzo por reducir las fallas del producto en el campo reducirá simultáneamente el número de defectos en la fábrica. Sin embargo, podemos aprender algo interesante sobre las raíces de la robustez y los fallos del control de calidad tradicional si enfrentamos Zero Defectos por sí solo. Es en oposición a Zero Defectos que surgieron los Métodos de Taguchi.
Robustez como consistencia
Según Zero Defectos, los diseños se arreglan esencialmente antes de que se haga sentir el programa de calidad; las graves degradaciones del rendimiento resultan de la falta de acoplamiento de las piezas y de la interfaz. Cuando los procesos de fabricación están fuera de control, es decir, cuando hay serias variaciones en la fabricación de piezas, no se puede esperar que los productos funcionen bien en el campo. Las piezas defectuosas hacen conexiones defectuosas. Todo un producto es la suma de sus conexiones. Por supuesto, no se pueden fabricar dos ejes de transmisión perfectamente por igual. Los ingenieros que trabajan dentro de la lógica de Zero Defectos presuponen una cierta variación en la producción de cualquier pieza. Especifican un objetivo para el tamaño y la dimensión de una pieza y, a continuación, las tolerancias que suponen permitirán desviaciones triviales con respecto a este objetivo. ¿Qué hay de malo en que un eje de transmisión que debería tener 10 centímetros de diámetro realmente llegue a 9,998? Nada. El problema, y está muy extendido, surge cuando los gerentes de los programas Zero Defectos hacen de esta necesidad una virtud. Se acostumbran a pensar en la calidad del producto en términos de desviación aceptable de los objetivos, en lugar del esfuerzo constante por alcanzarlos. Peor aún, los gerentes pueden especificar tolerancias demasiado amplias porque suponen que costaría demasiado para la fábrica reducirlas. Consideremos el caso de Ford vs. Mazda (entonces conocido como Toyo Kogyo), que se desarrolló hace unos años. Ford posee alrededor de 25% de Mazda y pidió a la empresa japonesa que construyera transmisiones para un automóvil que vendía en Estados Unidos. Se suponía que tanto Ford como Mazda debían construir con especificaciones idénticas; Ford adoptó Zero Defectos como estándar. Sin embargo, después de que los coches estuvieran en la carretera durante un tiempo, quedó claro que las transmisiones de Ford estaban generando costos de garantía mucho más altos y muchas más quejas de los clientes sobre el ruido. En su haber, Ford desmontó y midió cuidadosamente muestras de transmisiones realizadas por ambas compañías. Al principio, los ingenieros de Ford pensaban que sus indicadores no funcionaban correctamente. Todas las piezas de Ford estaban dentro de las especificaciones, pero las cajas de cambios Mazda no delataban ninguna variabilidad respecto a los objetivos. Podría que ¿por qué Mazda incurrió en menores costos de producción, chatarra, reelaboración y garantía?1 Precisamente esa fue la razón. Imagine que en algunas transmisiones Ford, muchos componentes cerca del límites exteriores de las tolerancias especificadas, es decir, bien según las definiciones de cero defectos, se ensamblaron aleatoriamente juntas. Entonces, muchas desviaciones triviales del objetivo tendían a «acumularse». Una variación trivial en una parte agravaba una variación en otra. Debido a las desviaciones, las piezas interactuaban con mayor fricción de la que podían soportar individualmente o con mayor vibración de la que los clientes estaban preparados para soportar. Los gerentes de Mazda trabajaron constantemente para llevar las piezas al objetivo. Intuitivamente, adoptaron un enfoque mucho más imaginativo para el control de calidad en línea que los gerentes de Ford; sin duda captaron la conformidad de fábrica de una manera que reemplazó el estilo de pensamiento de aprobación/rechazo, dentro de las especificaciones y fuera de las especificaciones asociado con Zero Defectos. Los gerentes de Mazda se basaron en la suposición de que la robustez comienza con el cumplimiento de los objetivos exactos consistentemente—no de permanecer siempre dentro de las tolerancias. Es posible que no se hayan dado cuenta de esto en ese momento, pero habría sido incluso mejor que perdieran el objetivo con una consistencia perfecta que golpearlo al azar, un punto que se ilumina con esta simple analogía. Sam y John están en el campo de tiro para practicar tiro al blanco. Después de disparar diez tiros, examinan a sus objetivos. Sam tiene diez disparos en un grupo apretado justo fuera del círculo de la diana. John, por otro lado, tiene cinco disparos en el círculo, pero están dispersos por todo el perímetro, tantos cerca del perímetro como cerca del centro muerto, y el resto de sus disparos están dispersos de manera similar a su alrededor (ver la sección «¿Quién es el mejor tiro?» diagrama).
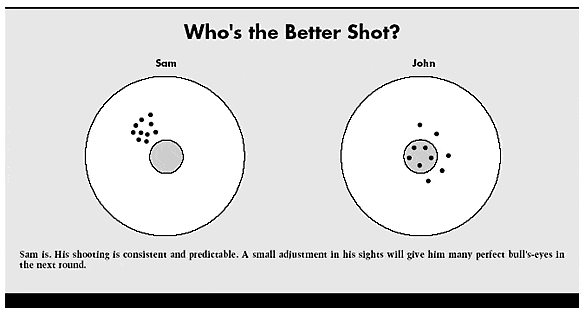
¿Quién es el mejor tirador? Sam lo es. Sus disparos son consistentes y predecibles. Un pequeño ajuste en su mira le dará muchos ojos de bueyes perfectos en la próxima ronda. Los teóricos de Zero Defectos dirían que John es el tirador superior porque su actuación no traiciona fallas. Pero, ¿a quién preferirías contratar como guardaespaldas? Los disparos de Sam son consistentes y prácticamente predecibles. Probablemente sepa por qué se perdió el círculo por completo. Un ajuste a sus miras dará muchos ojos de bueyes perfectos durante la próxima ronda. John tiene un problema mucho más difícil. Para reducir la dispersión de sus disparos, debe exponer prácticamente todos los factores bajo su control y encontrar la manera de cambiarlos en una combinación feliz. Puede decidir cambiar la posición de sus brazos, la tensión de su cabestrillo o la secuencia de sus disparos: respirar, apuntar, aflojar y apretar. Tendrá poca confianza en que obtendrá todos sus disparos en el círculo del ojo de buey la próxima vez. Cuando se extrapola a la fábrica, un rendimiento similar al de SAM promete una mayor robustez del producto. Una vez que se ha establecido la coherencia, que no es una tarea fácil, el producto de una atención incesante a los detalles del diseño y del proceso, ajustar el rendimiento al objetivo es una cuestión sencilla: el apilamiento se puede obviar por completo. Si cada eje de transmisión está a 0,005 centímetros, los operadores pueden ajustar la posición de la herramienta de corte. En ausencia de un rendimiento consistente, acercarse más al objetivo puede llevar mucho tiempo. Pero hay otra cara de esto. Existe una probabilidad mucho mayor de acumulaciones catastróficas por desviaciones aleatorias que por desviaciones que muestran consistencia. Suponiendo que ninguna pieza es muy defectuosa, es más probable que un producto fabricado a partir de piezas que están fuera de objetivo de la misma manera sea más robusto que un producto fabricado a partir de piezas cuyas desviaciones son dentro de las especificaciones pero impredecibles. Tenemos pruebas estadísticas de ello, pero un momento de reflexión debería ser suficiente. Si todas las piezas se fabrican de forma consistente, el producto funcionará de manera uniforme para los clientes y se perfeccionará más fácilmente en la próxima versión. Si todas las piezas se fabrican de forma errática, algunos productos serán perfectos y otros se derrumbarán. Así que el caso contra Zero Defectos comienza con esto: la robustez se deriva de la coherencia. Cuando la desviación es consistente, es posible ajustarse al objetivo; es más probable que se acumulen catastróficos por una desviación dispersa dentro de las especificaciones que por una desviación coherente en el exterior. Esta consideración por la coherencia, por estar en el objetivo, tiene una aplicación fascinante y práctica.
La función de pérdida de calidad
Análisis de Ford general las pérdidas en comparación con las de Mazda sugieren que cuando las empresas se desvían de los objetivos, corren un riesgo de pérdida cada vez más costoso. La pérdida general es pérdida de calidad más pérdida de fábrica. Cuanto más se desvía un fabricante de los objetivos, mayores serán sus pérdidas. Según nuestra experiencia, la pérdida de calidad (la pérdida que se produce después del envío de los productos) aumenta a un ritmo geométrico. Se puede cuantificar aproximadamente como la función de pérdida de calidad (QLF), basándose en una fórmula cuadrática simple. La pérdida aumenta en el cuadrado de la desviación del valor objetivo, L=D2 C, donde la constante viene determinada por el costo de la contramedida que la fábrica podría utilizar para alcanzar el objetivo. Si sabes qué hacer para alcanzar el objetivo, entonces sabes lo que cuesta esta acción por unidad. Si se retiene a gastar el dinero, con cada desviación estándar del objetivo, corre el riesgo de gastar más y más. Cuanto mayor sea la desviación de los objetivos, mayores serán los costes compuestos. Supongamos que un fabricante de automóviles elige no gastar, digamos,$ 20 por transmisión para conseguir una marcha exactamente en el objetivo. QLF sugiere que el fabricante acabaría gastando (cuando los clientes se enojaron)$ 80 para dos desviaciones estándar del objetivo ($ 20 multiplicado por el cuadrado de dos),$ 180 para tres,$ 320 para cuatro, y así sucesivamente. Esta es una simple aproximación, sin duda, no una ley de la naturaleza. No se puede esperar que los datos de campo reales reivindiquen con precisión el QLF, y si su empresa tiene una forma más precisa de realizar un seguimiento de los costos de las fallas de los productos, utilícelos. Pero el enorme valor de QLF, aparte de su inclinación al sentido común, es que traduce la noción de desviación de los objetivos del ingeniero en una simple estimación de costos que los administradores pueden utilizar. QLF es especialmente útil en las etapas iniciales importantes del desarrollo de nuevos productos, cuando se establecen tolerancias y se establecen objetivos de calidad.
Televisores Sony: Tokio contra San Diego
La lógica convincente de QLF se ilustra mejor con el rendimiento de los televisores Sony a finales de la década de 1970. El caso demuestra cómo los datos de ingeniería y los datos económicos pueden (y deben) verse en conjunto. Los ingenieros de productos de Sony han comprobado que los clientes prefieren imágenes con una densidad de color particular, llamémoslo una densidad nominal de 10. A medida que la densidad del color se desviaba de 10, los espectadores quedaban cada vez más insatisfechos, por lo que Sony estableció límites de especificación en nada menos que 7 y no más de 13. Sony fabricó televisores en dos ciudades, San Diego y Tokio. Los sets enviados desde San Diego se distribuyeron uniformemente dentro de las especificaciones, lo que significaba que era tan probable que un cliente comprara un juego con una densidad de color de 12,6 como uno con una densidad de 9,2. Al mismo tiempo, un conjunto de San Diego tenía la misma probabilidad de estar cerca de los límites de especificación corporativa de 13 o 7 que cerca del objetivo de satisfacción del cliente de 10. Mientras tanto, los envíos desde Tokio tendían a agruparse cerca del objetivo de 10, aunque en ese momento, alrededor de 3 de cada 1.000 conjuntos quedaban fuera de los estándares corporativos. Akio Morita, presidente de Sony, reflexionó sobre la discrepancia de esta manera: «Cuando le decimos a uno de nuestros empleados japoneses que la medición de una determinada parte debe estar dentro de una tolerancia de más o menos cinco, por ejemplo, se esforzará automáticamente por acercarla lo más posible a cero tolerancia. Cuando empezamos nuestra planta en los Estados Unidos, descubrimos que los trabajadores seguían las instrucciones a la perfección. Pero si dijéramos que lo hiciéramos entre más o menos cinco, lo obtendrían cerca de más o menos cinco, pero rara vez tan cerca de cero como lo hicieron los trabajadores japoneses». Si Morita asignara notas a las actuaciones de las dos fábricas, podría decir que Tokio tenía muchas más As que San Diego, aunque de vez en cuando obtuviera una D; 68% de la producción de Tokio estaba en el rango A, 28% en el rango B, 4% en el rango C y 0,3% en el rango. Por supuesto, San Diego hizo algunos sets fuera de las especificaciones; pero no entregó su Fs. Tokyo envió todo lo que construyó sin molestarse en comprobarlo. ¿Debería Morita haber preferido Tokio a San Diego? La respuesta, recuerde, debe reducirse a dólares y centavos, por lo que las convenciones de Zero Defectos no sirven de nada aquí. Supongamos que compró un televisor con una densidad de color de 12,9, mientras que su vecino compró uno con una densidad de 13,1. Si ves un programa en su set, ¿serás capaz de detectar alguna diferencia de color entre el tuyo y el suyo? Claro que no. La calidad del color no presenta un problema sorprendente en el límite de especificación de 13. Las cosas no se ponen más caras repentinamente para la planta de San Diego si un set sale a 13.1. Las pérdidas comienzan a acumularse cuando los clientes ven conjuntos en el valor objetivo de 10. Entonces, cualquier cosa que se aleje mucho de 10 parecerá insatisfactoria, y los clientes exigirán visitas de reparadores o exigirán juegos de reemplazo. En lugar de gastar unos pocos dólares por juego para ajustarlos a los objetivos, Sony tendría que gastar mucho más para hacer las cosas bien en los sets (alrededor de dos tercios de los sets de San Diego) que en realidad desagradaban a los clientes. (Ciertamente, la insatisfacción aumenta más entre 11,5 y 13 que entre 10 y 11,5). Lo que Sony descubrió es que no se gana prácticamente nada con el envío de un producto que apenas satisface el estándar corporativo sobre un producto que simplemente falla. San Diego envió juegos marginales «sin defectos», pero su calidad marginal resultó ser costosa. Usando QLF, Sony podría haber llegado a cifras aún más sorprendentes. Supongamos que la empresa estimó que el costo de la contramedida necesaria para poner bien cada juego (una contramedida de línea de montaje que sitúa cada conjunto en un 10 virtual) era$ 9. Pero por cada conjunto de San Diego con una densidad de color de 13 (tres desviaciones estándar del objetivo), Sony no gastó$ 9 pero$ 81. Se debería haber esperado que la pérdida total de calidad en San Diego fuera tres veces la pérdida total de calidad en la fábrica de Tokio.
Desviación: señal a ruido
Si Zero Defectos no funciona, ¿qué funciona? Hemos dicho que la calidad está diseñada principalmente en, no controlada desde fuera. En el trabajo de desarrollo, los ingenieros deben disciplinar sus decisiones en prácticamente cada paso comparando la pérdida de calidad esperada con el costo de fabricación conocido. Por otro lado, la fiabilidad de los cálculos del QLF está bastante restringida por la exactitud de las medidas más preliminares. Es imposible discernir correctamente cualquier función de pérdida sin establecer primero los objetivos correctamente. Cómo debería los ingenieros de diseño y los gerentes de fabricación establecen objetivos? Procedamos lentamente, reconsiderando lo que hacen los ingenieros cuando prueban componentes y subconjuntos y cómo establecen lo que ninguna pieza en particular «quiere ser» en el contexto de las cosas que se interponen en su camino. Cuando los ingenieros de Sony diseñaron sus televisores, asumieron que a los clientes exigentes les gustaría un diseño que mantuviera una buena imagen o «señal» lejos de la estación, en una tormenta eléctrica, cuando el procesador de alimentos estaba en uso e incluso cuando la compañía eléctrica suministraba baja tensión. Los clientes se sentirían consternados si la imagen se degradara cada vez que suben el volumen. Rechazarían un televisor que desarrollaba nieve y otros «ruidos» molestos cuando se veían afectados por condiciones de funcionamiento desagradables, que a su vez se consideran ruidos. En nuestra opinión, este lenguaje metafórico —la señal en comparación con el ruido— se puede utilizar para hablar de todos los productos, no solo de televisores. La señal es lo que el producto (o componente o subconjunto) intenta entregar. Los ruidos son las interferencias que degradan la señal, algunos de ellos procedentes del exterior, otros de sistemas complementarios dentro del producto. Son muy parecidos a los factores de los que hablamos que explican las variaciones en el rendimiento del producto: perturbaciones ambientales y perturbaciones generadas por las propias piezas. Por lo tanto, parece razonable definir la robustez como la virtud de un producto con una alta relación señal/ruido. A los clientes les molesta que les digan: «No se esperaba que usaras nuestro producto con mucha humedad o temperaturas por debajo del punto de congelación». Quieren un buen rendimiento en condiciones de funcionamiento reales, que a menudo no son perfectas. Todos asumimos que un producto que funciona mejor en condiciones adversas será mucho más duradero en condiciones normales. Las relaciones señal-ruido se diseñan en los productos antes de que la fábrica se intensifique. La fuerza de la señal de un producto (por lo tanto, su robustez) es principalmente responsabilidad de los diseñadores de productos. Las buenas fábricas son fieles a la intención del diseño. Pero los diseños mediocres siempre darán como resultado productos mediocres.
Elección de objetivos: matrices ortogonales
Entonces, ¿cómo maximizan los diseñadores de productos las relaciones señal-ruido? Las empresas de clase mundial utilizan un proceso de toma de decisiones en tres pasos: 1. Definen el objetivo específico, seleccionan o desarrollan la señal más adecuada y estiman el ruido concomitante. 2. Definen opciones factibles para los valores de diseño críticos, tales como dimensiones y características eléctricas. 3. Seleccionan la opción que proporciona la mayor robustez o la mayor relación señal/ruido. Por supuesto, es más fácil decirlo que hacerlo, por lo que tantas empresas en Japón, y ahora en Estados Unidos, han pasado a algún tipo de ingeniería simultánea. Definir y seleccionar las señales y los objetivos correctos no es una hazaña y requiere la experiencia de todos los especialistas en productos. Diseño de productos, fabricación, soporte de campo y marketing: todo esto debe ser resuelto simultáneamente por un equipo interfuncional. Los diseñadores de productos que han desarrollado una «sensación» para la ingeniería de productos particulares deben tomar la iniciativa en dichos equipos. Pueden salirse con la suya con unos pocos experimentos limitados, en los que la gente nueva tendría que realizar muchos más. Las empresas progresistas se esfuerzan por mantener a sus especialistas en productos trabajando en nuevas versiones en lugar de llevarlos a puestos directivos. Sus planes de compensación recompensan a las personas por hacer lo que mejor saben hacer. Pero las virtudes del trabajo en equipo plantean la cuestión más amplia de cómo desarrollar una estrategia experimental eficiente que no agote los recursos corporativos mientras trabajas para llevar los prototipos a la satisfacción del cliente. La intuición no es realmente una respuesta. Tampoco lo es la interfuncionalidad ni la teoría de la organización. Los diseñadores de productos necesitan una forma científica de conseguir robustez. Han dependido demasiado del arte. La forma más práctica de establecer relaciones señal-ruido se basa en el trabajo de Sir Ronald Fisher, un estadístico británico cuyas brillantes contribuciones a la agricultura no se han estudiado mucho en la actualidad. Lo más importante es su estrategia para la experimentación sistemática, incluyendo el plan asombrosamente sensible conocido como el «conjunto ortogonal». Tenga en cuenta la complejidad de mejorar la dirección de un automóvil. Los clientes quieren que responda de forma coherente. La mayoría de los ingenieros saben que la respuesta de la dirección depende de muchos parámetros críticos de diseño (rigidez del muelle, rigidez de los amortiguadores, dimensiones de los mecanismos de dirección y suspensión, etc.), todo lo cual podría optimizarse para lograr la mayor relación señal/ruido posible. Además, tiene sentido comparar el valor inicial del diseño con un valor mayor y otro menor. Si la rigidez del muelle tiene actualmente un valor nominal de 7, es posible que los ingenieros deseen probar la dirección a 9 y a 5. Un ingeniero de automóviles con el que hemos trabajado estableció que en realidad existen 13 variables de diseño para la dirección. Si los ingenieros compararan valores estándar, bajos y altos para cada variable crítica, tendrían 1.594.323 opciones de diseño. ¿Proceder con intuición? Más de un millón de posibles permutaciones ponen de relieve el desafío, el de una búsqueda ciega de una aguja en un pajar, y la dirección es solo un subsistema del automóvil. En Japón, los gerentes dicen que a los ingenieros «les gusta pescar con una caña»; los ingenieros se muestran optimistas de que «el próximo lanzamiento traerá al pez gordo»: un experimento más y darán con el diseño ideal. Naturalmente, las fallas repetidas conducen a más lanzamientos. El nuevo producto, que aún no es robusto para las condiciones de los clientes, se ve forzado a entrar en el mercado por la presión del tiempo, el dinero y la disminución de la cuota de mercado. Para completar la optimización de la robustez con mayor rapidez, la estrategia de búsqueda debe obtener la máxima cantidad de información de unos pocos ensayos. No vamos a repasar el álgebra aquí, pero la clave es desarrollar un sistema de ensayos que permita a los ingenieros de producto analizar el promedio efecto del cambio en los niveles factoriales bajo diferentes conjuntos de condiciones experimentales. Y esta es precisamente la virtud de la matriz ortogonal (véase la inserción, «Matrices ortogonales: definición de los objetivos correctos para el diseño»). Equilibra los niveles de rendimiento exigidos por los clientes con las numerosas variables (o ruidos) que afectan al rendimiento. Una matriz ortogonal para 3 niveles de rendimiento de dirección (bajo, medio y alto) puede reducir las posibilidades experimentales a 27. Los ingenieros pueden someter cada uno de los 27 diseños de dirección a una combinación de ruidos, como presión de neumáticos alta/baja, carretera rugosa/suave, temperatura alta/baja. Una vez completadas todas las pruebas, los valores de señal a ruido se pueden utilizar para seleccionar los mejores niveles para cada variable de diseño.
Arreglos ortogonales: Establecimiento de los objetivos adecuados para el diseño por: Lance A. Ealey
Los ingenieros de productos estadounidenses suelen proceder por el método de «un factor a la vez». Un grupo de ingenieros de dirección automotriz, habiendo identificado 13 variables críticas que rigen el rendimiento de la dirección, comenzaría a buscar mejoras en el diseño manteniendo todas las variables en sus valores actuales y registrando el resultado. En el segundo experimento, cambiarían uno de las variables (rigidez del muelle, digamos) a un valor inferior o superior, y si el resultado es una mejora (derrapando a 40 mph, no a 35), adoptarán que valor como constante de diseño. Luego viene el siguiente experimento en el que cambiarán una variable diferente pero no reconsiderarán la rigidez del muelle. Continuarán de esta manera hasta que hayan empujado el sistema de dirección lo más cerca posible de algún objetivo de rendimiento ideal (derrapar a 50 mph, no a 40). El problema obvio de estos resultados es que no tienen en cuenta las interacciones potencialmente críticas entre variables, y mucho menos las variaciones reales de las condiciones externas. Si bien una cierta rigidez del muelle proporciona un rendimiento amplio cuando la presión de los neumáticos es correcta, ¿qué tan bien funcionará esta rigidez cuando la presión de los neumáticos sea demasiado baja o demasiado alta? Por lo tanto, lo que necesitan estos ingenieros es un método eficiente para comparar los niveles de rendimiento de todos los factores de dirección que se están probando, de manera que se separen los promedio efecto de la rigidez del muelle en sus ajustes altos, bajos y actuales en los distintos sistemas de dirección posibles. A continuación, los ingenieros pueden seleccionar el ajuste de rigidez del muelle que tenga el efecto positivo más fuerte en la mejor combinación de variables. Si un determinado ajuste de rigidez del muelle funciona bien junto con cada ajuste de los otros 12 factores de suspensión, hay muy buenas posibilidades de reproducir resultados positivos en el mundo real. Esta es una ventaja importante con respecto al enfoque de «un factor a la vez». La matriz ortogonal puede considerarse como un mecanismo de destilación a través del cual pasa la experimentación del ingeniero. Su gran poder radica en su capacidad de separar el efecto que cada factor tiene sobre la media y la dispersión del experimento en su conjunto. Al aprovechar esta capacidad para clasificar los efectos individuales, los ingenieros pueden rastrear un gran número de factores simultáneamente en cada ejecución experimental sin confusión, evitando así la necesidad de realizar todas las combinaciones posibles o de esperar los resultados de un experimento antes de proceder con el siguiente. Considere la matriz ortogonal para la dirección. Cada una de las filas de la matriz que se muestra aquí constituye un experimento y cada columna vertical representa un único factor de prueba. La columna 1, por ejemplo, podría representar la rigidez del muelle. Los ingenieros prueban cada uno de los 13 factores de dirección en tres ajustes diferentes. (Para la rigidez del muelle, estos serían el ajuste actual, un ajuste más rígido y un ajuste más suave, anotados 1, 2 y 3 en la matriz). Los ingenieros realizan 27 experimentos en 13 variables, de la A a la M. Realizan 27 experimentos porque quieren exponer cada nivel de rendimiento (1, 2 y 3) entre sí un número igual de veces (o 3 × 3 × 3). El ingeniero debe realizar los 27 experimentos, siguiendo la disposición de los niveles de los factores mostrados aquí y dibujando sorteo para introducir un elemento de aleatoriedad en la experimentación.
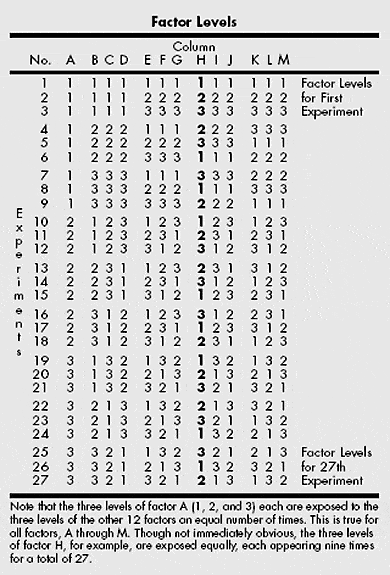
Niveles factor Tenga en cuenta que los tres niveles del factor A (1, 2 y 3) están expuestos a los tres niveles de los otros 12 factores un número igual de veces. Esto es cierto para todos los factores, de la A a la M. Aunque no es inmediatamente obvio, los tres niveles del factor H, por ejemplo, se exponen por igual, cada uno de los cuales aparece nueve veces para un total de 27. Es importante tener en cuenta que cada valor de rendimiento no está expuesto a todas las demás combinaciones posibles de valores de rendimiento. En este caso, por ejemplo, no hay ningún experimento en el que la rigidez del muelle a 2 esté expuesta a todas las demás variables en 2; no hay ninguna fila que muestre 2 en línea recta. Pero si miras hacia abajo cada columna, verás que cada nivel de rendimiento de cada variable está expuesto entre sí. igual número de veces. Antes de completar el experimento, los tres niveles de rigidez del muelle estarán expuestos por igual a los tres niveles de presión de los neumáticos, geometría de dirección,. El ingeniero que utiliza una matriz ortogonal no está interesado principalmente en los valores específicos producidos por los 27 experimentos. Por sí solos, es posible que estos valores no produzcan grandes mejoras con respecto al rendimiento existente. En cambio, está interesado en destilar el efecto que cada uno de los tres ajustes de rigidez del muelle tiene en el sistema en su conjunto. La «esencia» de este enfoque se extrae a lo largo del eje vertical de la matriz en lugar del eje horizontal. La matriz permite al ingeniero documentar los resultados: los niveles de factores que reducirán la variación del rendimiento, así como los que guiarán al producto de vuelta a su objetivo de rendimiento una vez que se haya alcanzado la coherencia. La matriz también se puede utilizar para encontrar variables que tienen poco efecto sobre la robustez o los valores objetivo: pueden y deben establecerse en sus niveles menos costosos. Si, por ejemplo, el valor medio de los primeros nueve ensayos sobre rigidez del muelle es 32,4, entonces eso podría caracterizar el nivel uno de rigidez del muelle. Si el valor medio para el segundo grupo de ensayos es 26,7 y el promedio del tercer grupo 28,9, entonces seleccionaríamos el nivel uno como el mejor valor para la rigidez del muelle. Este proceso de promediación se repite para encontrar el mejor nivel para cada una de las 13 variables de diseño. La matriz ortogonal es en realidad un sofisticado «sistema de conmutación» en el que se pueden conectar muchas variables de diseño y niveles de cambio diferentes. Este sistema fue concebido para permitir al diseñador relativamente inexperto extraer el promedio efecto de cada factor en los resultados experimentales, de modo que pueda llegar a conclusiones fiables a pesar del gran número de variables cambiantes. Por supuesto, una vez que se han establecido las características de un producto para que un diseñador pueda decir con certeza que los valores de diseño, es decir, las relaciones señal/ruido optimizadas, no interactúan en absoluto, las matrices ortogonales son superfluas. En su lugar, el diseñador puede proceder a probar cada variable de diseño de forma más o menos independiente, sin preocuparse por crear ruido en otras piezas o subensamblajes.
Prueba de verificación del sistema: el momento de la verdad
Después de maximizar las relaciones señal/ruido y optimizar los valores de diseño, los ingenieros crean prototipos. La solidez del producto completo se verifica ahora en la prueba de verificación del sistema (SVT), que quizá sea el evento más crítico durante el desarrollo del producto. En el SVT, los primeros prototipos se comparan con el producto de referencia actual. Los ingenieros someten tanto el prototipo como el punto de referencia a las mismas condiciones extremas que pueden encontrarse en el uso real. Los ingenieros también miden las mismas relaciones señal/ruido críticas para todos los competidores. Es muy importante que el nuevo producto supere la robustez del producto de referencia. Si el voltaje nominal ideal es de 115 voltios, queremos televisores que tengan una señal de 10 incluso cuando la tensión desciene a 100 ruidosos o suba a 130 igualmente ruidosos. Cualquier desviación de la señal perfecta debe considerarse en términos de QLF, es decir, como un riesgo financiero grave. El producto robusto, por lo tanto, es el que minimiza el promedio del cuadrado de la desviación del objetivo, promediado en función de las diferentes condiciones de uso del cliente. Supongamos que desea comprar una fuente de alimentación y aprender que puede comprar una con una desviación estándar de un voltio. ¿Deberías cogerlo? Si el valor medio de la tensión de salida es de 1.000 voltios, la mayoría de la gente pensaría que, en promedio, un error de solo un voltio es muy bueno. Sin embargo, si la salida promedio fue de 24 voltios, entonces una desviación estándar de uno parece muy grande. Debemos considerar siempre el cociente del valor medio dividido por la desviación estándar. El SVT proporciona una indicación muy clara, mucho antes de que comience la producción, de si los clientes percibirán que el nuevo producto tiene una calidad y un rendimiento de primera clase. Una vez que se verifica que el nuevo diseño tiene una robustez superior, los ingenieros pueden proceder a resolver problemas rutinarios, con la plena confianza de que el producto aumentará constantemente la lealtad del cliente.
Regreso a la fábrica
La relación entre el campo y la fábrica resulta ser sutil, lo contrario de lo que cabría esperar. Sabemos que si controla la variación en la fábrica, se reducen las fallas en el campo. Pero como dijimos al principio, un esfuerzo concertado para reducir las fallas de los productos en el campo reducirá simultáneamente el número de defectos en la fábrica. Esfuércese por reducir las variaciones en los componentes del producto y reducirá las variaciones en el sistema de producción en su conjunto. Cualquier refuerzo de un diseño, es decir, cualquier aumento notable de la relación señal-ruido de un producto, reducirá simultáneamente las pérdidas de calidad de una fábrica. ¿Por qué debería ser así? Por muchas razones, lo más importante son las simetrías entre diseño para robustez y diseño para fabricación. Piense en lo mucho más robustos que se han vuelto los productos desde la introducción de los plásticos moldeados y los circuitos de estado sólido. En lugar de servir muchos cables, tubos e interruptores interconectados, cualquiera de los cuales puede fallar, los ingenieros ahora pueden imprimir un millón de transistores en un chip prácticamente indestructible. En lugar de unir muchos componentes con tornillos y sujetadores, ahora podemos consolidar piezas en subconjuntos y montarlas en marcos moldeados que encajan entre sí. Todas estas mejoras reducen en gran medida las posibilidades de que el ruido interfiera con la señal; se desarrollaron para que los productos fueran robustos. Sin embargo, también han hecho que los productos sean infinitamente más fabricables. Los principios del diseño para la robustez suelen ser indistinguibles de los principios del diseño para la fabricación: reducir el número de piezas, consolidar subsistemas e integrar la electrónica. Un producto robusto puede tolerar mayores variaciones en el sistema de producción. Por favor, el cliente y complacerá al gerente de fabricación. Prepárate para las variaciones en el campo y allanarás el camino para reducir las variaciones en el taller. Nada de esto significa que el director de fabricación debe dejar de intentar reducir las variaciones del proceso o lograr las mismas variaciones con procesos más rápidos y económicos. Y hay excepciones evidentes que demuestran la regla: la producción de chips, por ejemplo, donde los controles de fábrica son cada vez más estrictos, aunque es difícil pensar en excepciones en productos como los automóviles y los productos electrónicos de consumo. La fábrica es un lugar donde los trabajadores deben tratar de cumplir, no desviarse, de los objetivos nominales establecidos para los productos. Es hora de pensar en la fábrica como un producto con objetivos propios. Al igual que un producto, se puede decir que la fábrica emite una señal implícita (la producción consistente de productos robustos) y que está sujeta a las interrupciones del ruido: temperaturas variables, máquinas degradadas, polvo,. Con QLF, las opciones de fábrica, como las opciones para el producto, pueden reducirse al costo de desviación de los objetivos. Considere, por ejemplo, que una amoladora cilíndrica crea una forma cilíndrica de forma más consistente que un torno. Los diseñadores de productos han defendido máquinas tan dedicadas; quieren la mayor precisión posible. Los ingenieros de fabricación han preferido tradicionalmente el torno menos preciso porque es más flexible y reduce los costes de producción. ¿Debería la dirección favorecer la rectificadora cilíndrica más precisa? ¿Cómo comparas las de cada grupo con respecto a la pérdida de calidad? En ausencia del cálculo de QLF, el método más común para establecer las tolerancias de fabricación es celebrar una reunión de concurrencia. Los ingenieros de diseño se sientan a un lado de la sala de conferencias, mientras que los ingenieros de fabricación están en el lado opuesto. Los ingenieros de diseño del producto comienzan a cantar «Tolerancia más estricta, tolerancia más estricta, tolerancia más estricta», y los ingenieros de fabricación responden con «tolerancia más floja, tolerancia más floja, tolerancia más floja». Presumiblemente, la fábrica optaría por un torno si la fabricación cantara más fuerte y durante más tiempo. Pero, ¿por qué seguir un proceso tan irracional cuando los diseñadores de productos y los fabricantes? lata poner un valor en dólares a la precisión de calidad? La administración debe elegir el nivel de precisión que minimice el costo total, el costo de producción y la pérdida de calidad, lo que es lo básico de QLF. Los gerentes pueden comparar los costes de los procesos de fábrica de la competencia añadiendo el coste de fabricación y la pérdida de calidad media (a partir de las desviaciones esperadas) de cada proceso. Obtienen una precisión económica mediante la evaluación de procesos de producción alternativos factibles, como el torno y la rectificadora cilíndrica. ¿Cuál sería la pérdida de calidad si la fábrica usara el torno? ¿Los ahorros valen la pena las pérdidas futuras? Se pueden aplicar principios similares a los sistemas más grandes. En lo que podría denominarse «diseño de parámetros de proceso», los fabricantes pueden optimizar los parámetros de producción (velocidad del husillo, profundidad de corte, velocidad de avance, presión, temperatura) de acuerdo con un conjunto ortogonal, al igual que la rigidez del muelle en un mecanismo de dirección. Cada fila de la matriz ortogonal puede definir una prueba de producción diferente. En cada ensayo, los ingenieros producen y miden varias piezas y, a continuación, utilizan los datos para calcular la relación señal/ruido de esa prueba. En un paso final, establecen el mejor valor para cada parámetro de producción.
Calidad en línea: Shop Floor de Shigeo Shingo por: Connie Dyer
¿Las tolerancias de ajuste aumentan necesariamente el espectro de unos costes de producción significativamente más elevados? No según Shigeo Shingo, el hombre que enseñó ingeniería de producción a una generación de gerentes de Toyota. Ahora con más de 80 años, Shingo sigue promoviendo activamente el «Control de Calidad Cero», mediante el cual pretende eliminar los costosos procesos de inspección o la dependencia del control de calidad estadístico a nivel del taller. Shingo aboga por el uso de mecanismos y rutinas de control de calidad en proceso de bajo costo que, de hecho, incorporan 100% inspección en el origen de los problemas de calidad. Argumenta a favor de verificar las causas en lugar de los efectos de los errores del operador y las anomalías de la máquina. Esto no se logra mediante costosos sistemas de control automatizados, sino mediante métodos a prueba de errores como poka-yoke. Poka-yoke en realidad significa «prueba de errores»; Shingo se resiste a la idea de que los empleados cometen errores porque son tontamente incompetentes. Shingo cree que todos los seres humanos tienen fallas en la atención. El sistema, no el operador, tiene la culpa cuando se producen tales defectos. El método poka-yoke básicamente incorpora la función de una lista de verificación en una operación para que nunca podamos «olvidar lo que hemos olvidado». Por ejemplo, si un operador necesita insertar un total de nueve tornillos en un subensamblaje, modifique el contenedor para que suelte nueve a la vez. Si queda un tornillo, el operador sabe que la operación no ha finalizado. Muchas ideas poka-yoke se basan en conceptos conocidos a prueba de errores; los mecanismos también están relacionados, en principio, con jidohka, o autonomía: el concepto de «máquinas inteligentes» de bajo costo que se detienen automáticamente cuando se completa el procesamiento o cuando se produce una anomalía. Shingo recomienda cuatro principios para implementar poka-yoke: 1. Control aguas arriba, lo más cerca posible de la fuente del defecto potencial. Por ejemplo, modifique ligeramente la forma de una pieza simétrica para asegurar el posicionamiento correcto con una plantilla o un sensor ajustados a una característica asimétrica. Además, conecte un dispositivo de monitoreo que detectará una anomalía del material o un estado anormal de la máquina y desencadenará el apagado antes de que se genere un defecto y se transmita al siguiente proceso. 2. Establezca controles en relación con la gravedad del problema. Una simple señal o alarma puede ser suficiente para comprobar un error que el operador corrige fácilmente, pero evitar que se siga avanzando hasta que se corrija el error es aún mejor. Por ejemplo, un contador de tableros de control cuenta el número de soldaduras por puntos realizadas y acciona las abrazaderas de plantilla; si se omite una, la pieza de trabajo no se puede quitar de la plantilla hasta que se corrija el error. 3. Piensa de forma inteligente y pequeña. Esfuércese por lograr la intervención más sencilla, eficiente y económica. No sobrecontrole: si los errores del operador se deben a la falta de operaciones, mejore los métodos antes de intentar controlar los resultados. Del mismo modo, si el costo del ajuste del equipo es elevado, mejore la confiabilidad del equipo y considere cómo simplificar las operaciones de ajuste antes de implementar un costoso sistema de inspección automatizada. 4. No demore la mejora mediante un análisis excesivo. Las soluciones Poka-yoke suelen ser el producto de la decisión y la acción rápida en el taller. Si bien las mejoras de diseño pueden reducir los defectos de fabricación a largo plazo, puede implementar muchas ideas poka-yoke a un costo muy bajo en cuestión de horas después de su concepción, lo que reduce eficazmente la brecha de calidad hasta que desarrolle un diseño más sólido. Desarrollados en cooperación por operadores, ingenieros de producción y personal de talleres de maquinaria, los métodos poka-yoke se emplean ampliamente en las operaciones de procesamiento y ensamblaje en Japón y representan uno de los pináculos creativos de la mejora continua de la planta de producción. En su estado más desarrollado, esta actividad de mejora puede respaldar los esfuerzos de ingeniería de calidad fuera de línea al alimentar un flujo continuo de datos sobre problemas de calidad reales en el proceso. ¿El resultado? Un proceso robusto, que produce una uniformidad mejorada de las piezas y, a menudo, permite a los gerentes acelerar la producción y reducir el tiempo de ciclo de forma simultánea.
¿Cuánta intervención?
Por último, está la cuestión de cuánto intervenir durante producción. Realice el tipo de intervención más común, la comprobación y el ajuste en línea de la maquinaria y el proceso. En ausencia de supervisión por parte del operador, las piezas tienden a desviarse progresivamente del objetivo. Sin orientación, los diferentes operadores tienen nociones muy variadas de (1) la frecuencia con la que deben revisar sus máquinas y (2) qué tan grande debe ser la discrepancia antes de ajustar el proceso para volver a acercar el valor de la pieza al objetivo. Aplicando QLF, puedes estandarizar la intervención. El costo de la comprobación y el ajuste siempre ha sido fácil de determinar; simplemente hay que calcular el costo del tiempo de inactividad. Con QLF, los gerentes también pueden calcular el costo de no interviniendo, es decir, el valor en dólares para la empresa de la reducción de la variación de las piezas. Volvamos a los ejes de transmisión. El intervalo de comprobación es de tres y el mejor objetivo de ajuste es 1/1000 de pulgada. Si la discrepancia medida con respecto al objetivo es inferior a 1/1000 de pulgada, la producción continúa. Si la discrepancia medida supera esto, el proceso vuelve a ajustarse al objetivo. ¿Esto realmente permite a los operadores mantener los productos cerca del objetivo de forma que se minimice el costo total? Se podría argumentar que medir cada tercer eje es demasiado costoso. ¿Por qué no cada décima parte? Hay una forma de averiguarlo. Supongamos que el costo de la intervención es de 30 centavos, y es casi seguro que los ejes se desvían del valor objetivo cada quinta o sexta operación. Entonces, de cada diez producidos, al menos cuatro ejes defectuosos se apagarán y las pérdidas de calidad se acumularán. Si el séptimo eje sale con dos desviaciones estándar, el costo será$ 1,20; si el décimo sale con tres desviaciones estándar, el costo será$ 2.70; y así sucesivamente. Quizás el mejor intervalo para comprobar sea cada cuarto eje o cada quinto, no cada tercero. Si el cuarto eje es solo una desviación estándar del valor objetivo, es probable que la intervención no valga la pena. La cuestión, una vez más, es que estas cosas pueden y deben calcularse. No hay ninguna razón para ser fanático de la calidad si no puedo justifica tu fanatismo por QLF. Cerca del objetivo, la producción debe continuar sin ajustes; la pérdida de calidad es pequeña. Fuera del límite, el proceso debe ajustarse antes de que continúe la producción. Este enfoque básico de la intervención también se puede aplicar al mantenimiento preventivo. El mantenimiento preventivo excesivo cuesta demasiado. Un mantenimiento preventivo inadecuado aumentará excesivamente la pérdida de calidad. El mantenimiento preventivo optimizado minimizará el coste total. En Japón, se dice que un gerente que cambia la calidad para ahorrar un poco los gastos de fabricación es «peor que un ladrón», quizás un poco duro, pero plausible. Cuando un ladrón roba$ 200 de su empresa, no hay pérdida neta de riqueza entre ustedes dos, solo un intercambio de activos. Las decisiones que generan enormes pérdidas de calidad desechan la productividad social, la riqueza de la sociedad. El enfoque disciplinado y cuantitativo de QLF con respecto a la calidad se basa en las actividades de participación de los empleados y las mejora para mejorar la calidad y la productividad. Ciertamente, las actividades de mejora centradas en la fábrica no aumentan en gran medida la robustez de un producto. Sin embargo, pueden ayudar a realizarlo reduciendo el ruido generado por la compleja interacción de los factores de calidad del taller: operadores, métodos operativos, equipos y materiales. Los empleados comprometidos con dar en el blanco constantemente echan un ojo más nítido a todas las características del entorno de la fábrica. Cuando se comprometen su ingenio y su conciencia de costos, las condiciones cambian drásticamente, los equipos prosperan y proliferan datos valiosos para respaldar un mejor diseño de productos y procesos. Un énfasis inicial en toda la empresa en un diseño sólido de productos puede incluso reducir el tiempo de desarrollo y facilitar la transición a la producción a gran escala. Con demasiada frecuencia, los gerentes piensan que la calidad es responsabilidad de unos pocos responsables de control de calidad que se encuentran en una esquina de fábrica. Ya debería ser evidente que la calidad es para todos, sobre todo para los estrategas de la empresa. Solo gracias al esfuerzo de cada empleado, desde el CEO en adelante, la calidad se convertirá en algo natural. La ventaja más difícil de alcanzar en la nueva competición global es el orgullo de la excelencia. 1. Vea el admirable relato de este caso de Lance A. Ealey en Calidad por diseño: métodos de Taguchi® y la industria estadounidense (Dearborn, Mich.: ASI Press, 1988), págs. 61 a 62.— Escrito por Genichi Taguchi Don Clausing