A la cabeza del piso de la fábrica
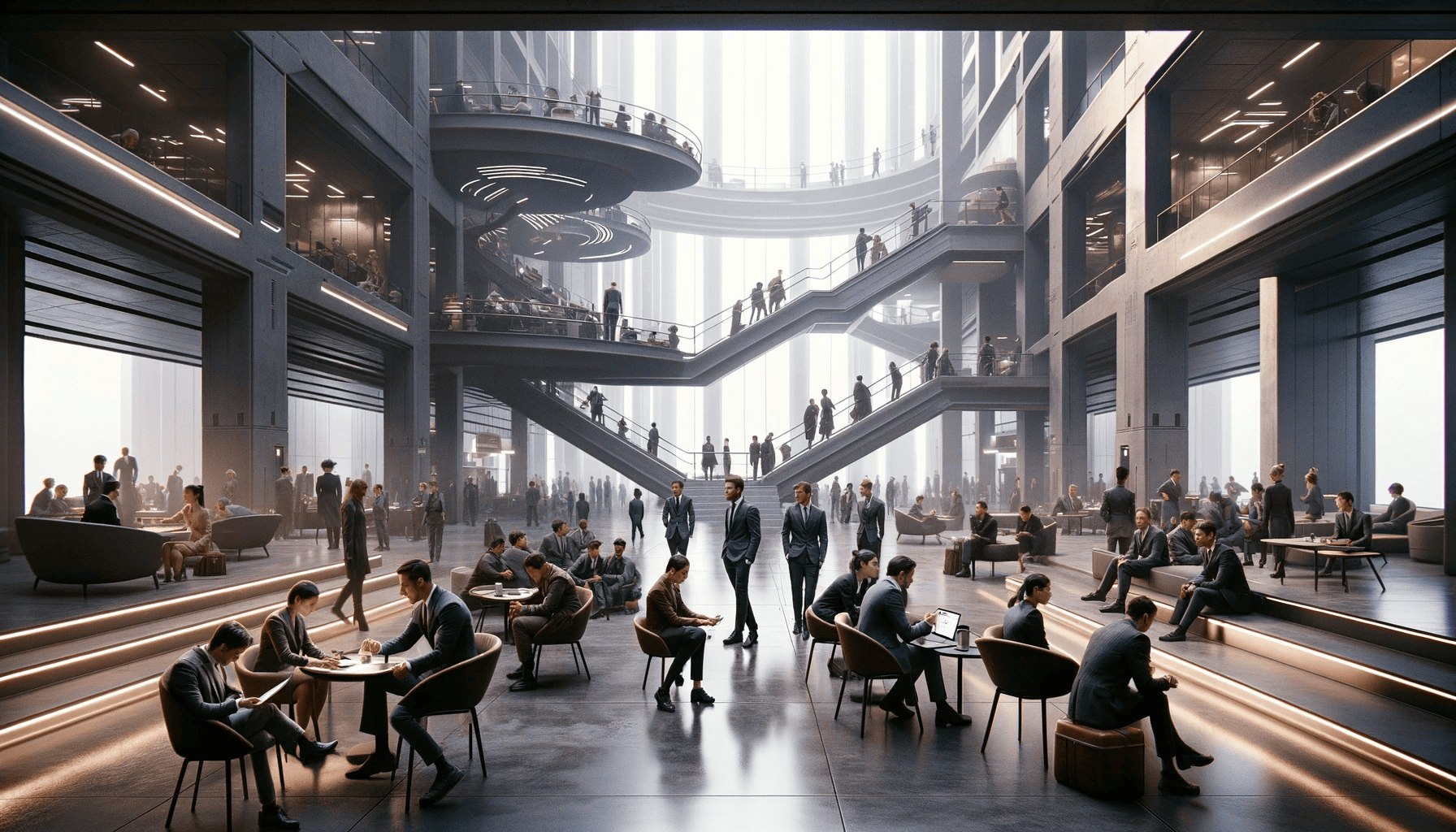
Arreglar una planta disfuncional no es fácil, pero se puede hacer si involucra a todos en la revisión.
••• A pesar de todo lo que se habla de la fabricación ajustada, sigue siendo la excepción: las fábricas están abarrotadas, los cuellos de botella retrasan la producción y los productos incorrectos se acumulan en el inventario mientras que no se pueden encontrar los correctos. Arreglar una fábrica disfuncional no es fácil, pero consideremos este sorprendente caso de Alemania, donde la resistencia a las innovaciones de gestión en la fábrica ha sido tradicionalmente más fuerte. En lugar de cerrar una planta con un rendimiento deficiente, el fabricante de materiales Isola Group dio a los trabajadores la oportunidad de empezar de nuevo, literal y simbólicamente. Inspirado en la herramienta japonesa conocida como las cinco S (para «ordenar», «almacenar», «brillar», «estandarizar» y «mantener»), los gerentes de la planta pidieron a los trabajadores que limpiaran la fábrica y sugirieran formas de hacerla más eficiente. Primero, salieron 70 toneladas de exceso de «cosas» —60 estantes de inventario vacíos, 100 metros cúbicos de material de embalaje innecesario, 150 palés de tambores vacíos— transportadas en 45 camiones. A continuación, a los trabajadores se les ocurrieron 800 ideas de mejora, la mayoría de las cuales se pusieron en práctica al final. Luego los empleados usaron más de 150 latas de pintura para hacer un lavado de cara al lugar. Luego los gerentes se quitaron la corbata. Todos llevaban el mismo uniforme: abrigos de fábrica y gafas de protección. El jefe de la obra, el planificador de producción y el controlador del sitio convirtieron su espacio de trabajo en la planta de producción en una «oficina de proyectos» y continuaron invitando a dar comentarios informales; pronto los trabajadores pasaban por aquí para ofrecer sugerencias o informar de problemas. El equipo de la oficina de proyectos también patrocinó sesiones más formales con trabajadores de todos los turnos para discutir problemas, analizar las causas fundamentales e identificar rápidamente soluciones. Las reuniones diarias sobre las pérdidas de rendimiento proporcionaron una rápida retroalimentación sobre las iniciativas de los trabajadores; todos los días, el equipo de la oficina de proyectos vigilaba si había fallos en los rendimientos del día anterior e ideaba contramedidas. Por último, el equipo preguntó: «¿Cuál es el verdadero nivel de rendimiento actual de la planta? ¿Y qué es un nivel alcanzable?» En el pasado, los controladores centrales habían establecido parámetros de referencia de rendimiento arbitrarios, ninguno de los cuales tenía sentido para los trabajadores. Así que el equipo seleccionó nuevos objetivos de productividad y rendimiento (objetivos basados en la evaluación de sus capacidades por parte de los empleados) y desarrolló y publicó gráficos en áreas comunes para que todos pudieran seguir el progreso de la planta. El hecho de que la dirección escuchara las ideas de los trabajadores (y las pusiera a prueba rápidamente) ayudó a levantar la moral y a mejorar directamente los procesos, reduciendo los tiempos de ciclo y eliminando prácticamente el inventario de trabajos en curso. A medida que la iniciativa cobró impulso, los empleados comenzaron a ofrecerse como voluntarios para trabajar horas extras en las mejoras. ¿Los resultados? Después de tres meses, la planta logró un aumento del rendimiento del 4%, del 91% al 95%, y cada punto porcentual de mejora representó un ahorro anual de unos 850 000 dólares en costes de materiales. Además, el EBITDA mejoró de un déficit de aproximadamente un 15% a alcanzar el punto de equilibrio. La planta va camino de ofrecer un EBITDA positivo del 10 al 15% antes de fin de año.